
1. What are the main causes of vibration during machining, and how do they impact metalworking operations?
Managing vibration during machining operations is crucial for maintaining precision, tool longevity, and overall efficiency. Quick changes in direction, stops, and starts (either of the table or the cutting tool) cause deflection that impact the initiating moments of a cut. Inconsistent forces during a cut, such as unbalanced tools or workpieces, as well as the state of engagement of multi-tooth cutters, naturally cause some resonance. Because of some instability in the cutting process, chatter, or the buildup of oscillations in the machine tool structure and cutting process, limits metal removal rates.
2. What technologies do modern machine tools use to address vibration, and how do they improve machining processes?
Modern machine tools employ advanced technologies such as accelerometers to monitor vibration, adaptive controls to adjust spindle speed, Turcite-lined box ways for better vibration resistance, cast iron machine beds for superior damping, compact spindles, and precision hybrid bearings. Additionally, dynamically balanced spindles and dual-contact spindle systems enhance rigidity and reduce vibration, leading to improved machining accuracy and tool life.
3. How does the BIG-PLUS dual contact spindle system reduce vibration?
BIG-PLUS is a dual contact spindle system where the shank contacts the spindle taper and the spindle face simultaneously. With BIG-PLUS simultaneous contact, machining rigidity is greatly enhanced due to the larger contact diameter of the tool holder flange face. This larger face contact, combined with the taper contact, works together to resist deflection. With less deflection, greater machining accuracy and superior finish can be achieved.
4. What workholding solutions are effective in combating vibration, and what benefits do they offer?
Mineral cast workholding solutions are effective in combating vibration by removing weight and introducing damping qualities, offering significantly better attenuation rates compared to standard gray cast iron. These solutions are composed of mineral particles and epoxy resin, creating a dense yet lightweight composite. This structure maintains the integrity of precision machined surfaces and clamping components, resulting in higher output and improved machining quality.
5. How does tool overhang influence vibration in machining, and what solutions can mitigate its effects?
Tool overhang, or the length-to-diameter ratio, increases susceptibility to detrimental vibration as the overhang grows. To mitigate its effects, use the largest possible diameter at the minimum possible length, the lightest weight tooling possible, and the smallest possible insert points. For situations where this isn’t feasible, upgrading to tooling with damping characteristics, such as the SMART DAMPER system, is beneficial. The SMART DAMPER system incorporates a passive damping mechanism that functions as a counter action by way of high resonance friction action, minimizing the effects of high-frequency oscillations, absorbing vibration effectively, and allowing higher machining accuracy.
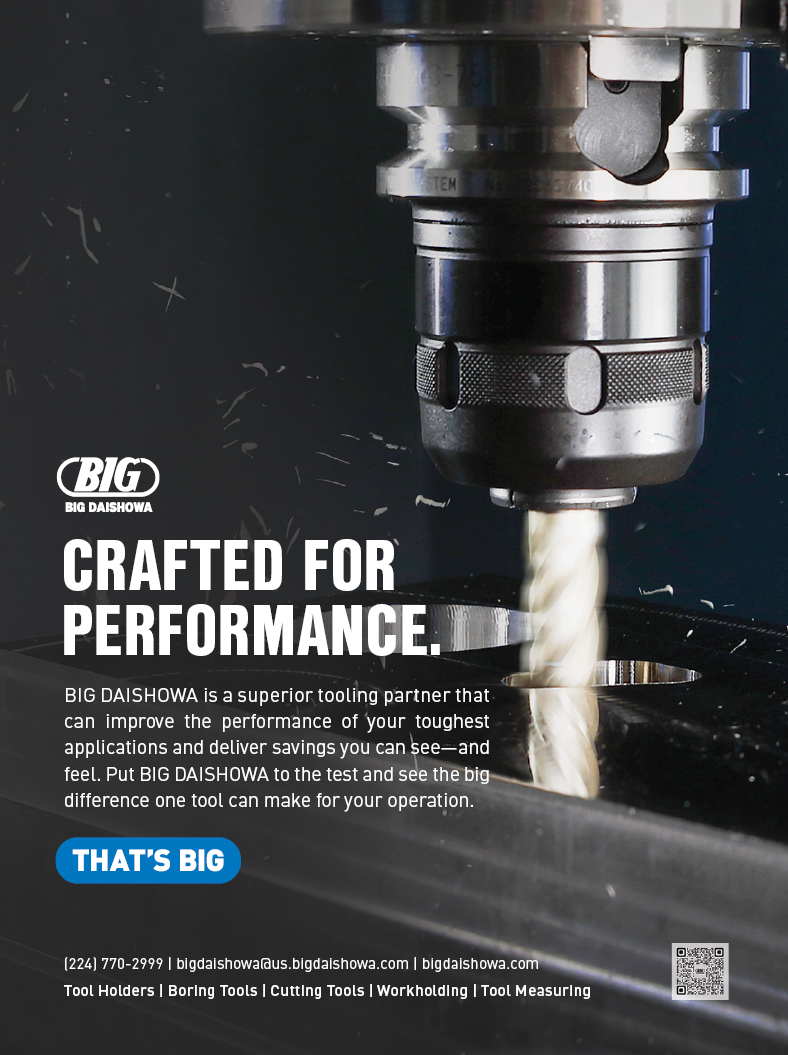
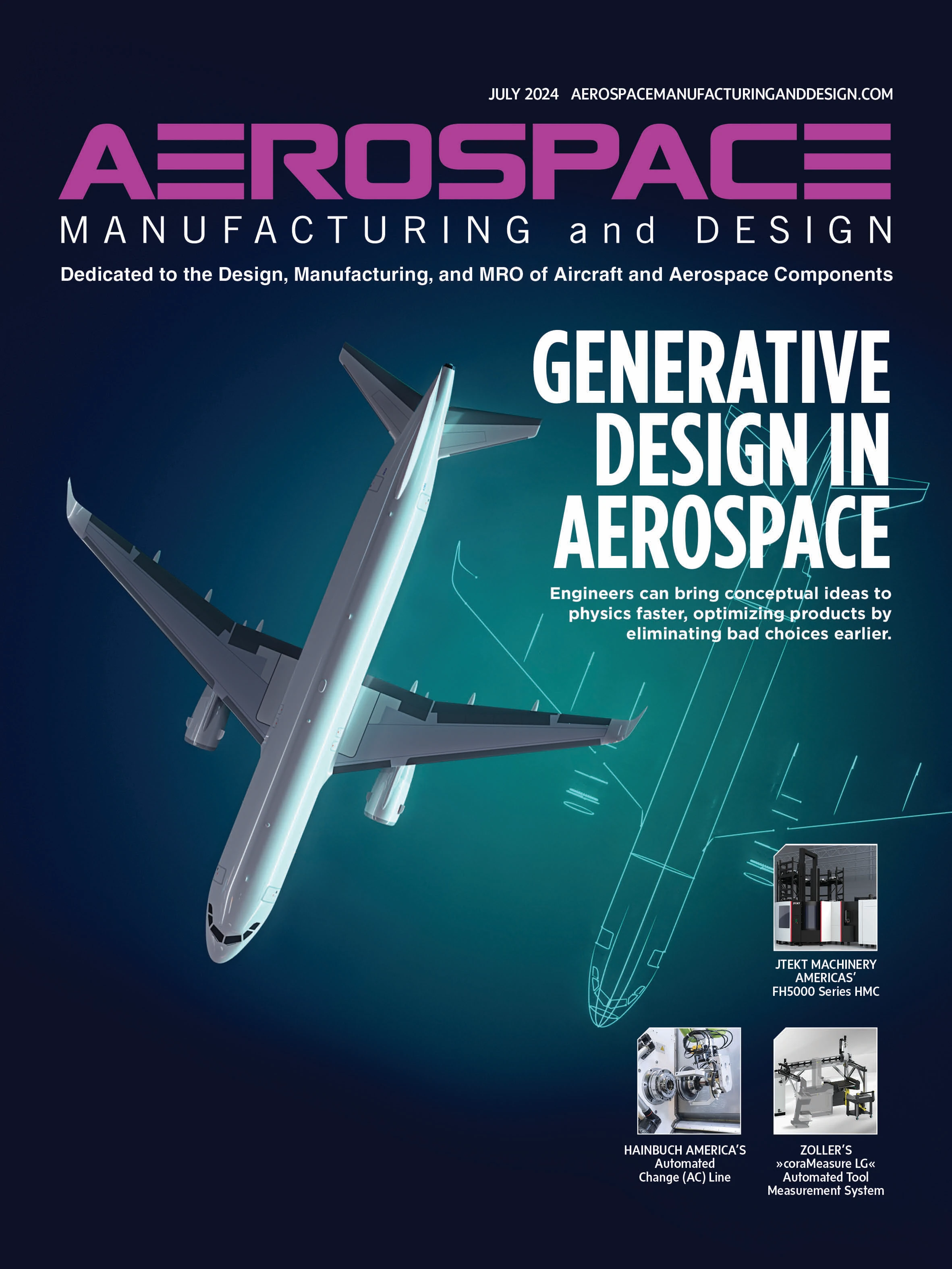
Explore the July 2024 Issue
Check out more from this issue and find your next story to read.
Latest from Aerospace Manufacturing and Design
- AAMI project call submission deadline extended to May 12
- Jergens launches cast iron tooling column additions
- Airbus to acquire assets relating to its aircraft production from Spirit AeroSystems
- FANUC America's Cobot and Go web tool
- Chicago Innovation Days 2025: Shaping the future of manufacturing
- High-density DC/DC converters for mission-critical applications
- #59 - Manufacturing Matters: Additive manufacturing trends, innovations
- ACE at 150: A legacy of innovation and industry leadership