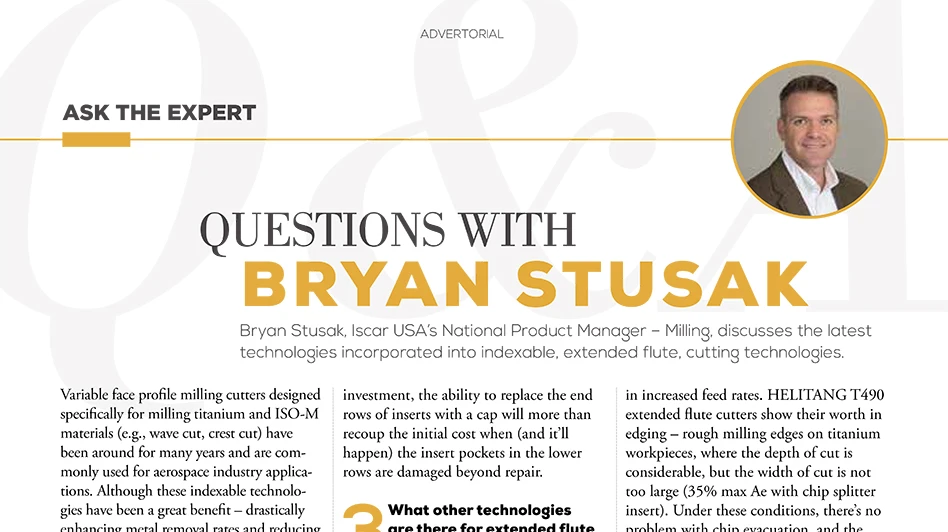
GIE Media

Variable face profile milling cutters designed specifically for milling titanium and ISO-M materials (e.g., wave cut, crest cut) have been around for many years and are commonly used for aerospace industry applications. Although these indexable technologies have been a great benefit – drastically enhancing metal removal rates and reducing cycle times – there’s still more room to improve these types of cutting tool technologies and drive productivity to higher levels.
1 What are some design characteristics being applied to extended flute cutting tools?
Many of the design attributes are designed to take advantage of the modern, purpose built, machine tools they’re used on. Coolant pressure/flow rates are one of the main variables to account for on modern machines designed for productive machining of exotic materials. Cutters such as ISCAR’s XQUAD line of extended flute cutters have coolant nozzles which can be changed to maximize/equalize coolant delivery to each cutting edge.
2 What other characteristics can be beneficial for indexable extended flute cutting tools?
End cap designs that keep an expensive cutting tool investment in service. The longer gage lengths of an extended flute cutting tool means increased bending and/or toppling of the cutting tool assembly, especially for 2-piece assemblies that consist of a tool holder and extended flute shell mill. This is evident in the bottom row (or end row) of inserts showing much more wear and/or failing. Even though a modular design (with end cap) will slightly increase initial investment, the ability to replace the end rows of inserts with a cap will more than recoup the initial cost when (and it’ll happen) the insert pockets in the lower rows are damaged beyond repair.
3 What other technologies are there for extended flute milling applications?
The desire to improve performance of extended flute cutters led to the development/introduction of inserts with a chip splitting (CS) action. The cutting edges of these advanced inserts feature specially designed CS grooves to create smaller chip segments. Further developments led to the introduction of inserts with the full wave (FW) cutting edge design, which generates even smaller chip segments, further reducing radial tool pressure vs. chip splitting groove technology.
The reduction of power is typically around 35% less than traditional cutters. Iscar offers the unique FW geometry for rough milling in unstable conditions (high overhang, poor workholding, etc.) in both its MILLSHRED P290 and HELITANG T490-13 inserts. In many such cases, CS cutters demonstrate improved dynamic behavior (i.e., less vibration) that results in better performance. These lines are excellent problem solvers, especially when machining deep cavities and pockets where chip evacuation can be an issue.
Iscar’s family of HELITANG T490 extended flute cutters, primarily tools with size 13mm inserts, is an exception to this general rule. The principle of tangential clamping contributes to improving the cutter rigidity and optimal loading of the screw to secure the inserts while usually ensuring a higher insert density that results in increased feed rates. HELITANG T490 extended flute cutters show their worth in edging – rough milling edges on titanium workpieces, where the depth of cut is considerable, but the width of cut is not too large (35% max Ae with chip splitter insert). Under these conditions, there’s no problem with chip evacuation, and the extended flute cutter carrying tangential clamped inserts wholly meets the requirements of high-efficiency roughing.
Iscar’s CS geometry (serrated) for rough milling in unstable conditions (high overhang, poor workholding, etc.) is available in both MILLSHRED P290 and HELITANG T490-13 inserts. In many such cases, CS cutters demonstrate improved dynamic behavior (i.e., less vibration) that results in better performance. With advancements in carbide substrates and coatings, these tools far exceed HSSCo and powder metals with better tool life and increased speeds for increased production in today’s competitive landscape.
4 What tool offerings does Iscar promote for various applications?
Shouldering applications:
MILLSHRED P290 Line: 0.750" to 4.000" diameters; End mill, extended flute shell mill, and face mills designs; 12mm and 18mm insert sizes; 2 types of insert offerings: FW serrated and straight edge
HELITANG T490-13: 1.0" to 8.0" diameters; End mill, extended flute shell mill, and face mills designs; 13mm insert size; FW serrated and CS offerings.
For more information: ISCAR USA

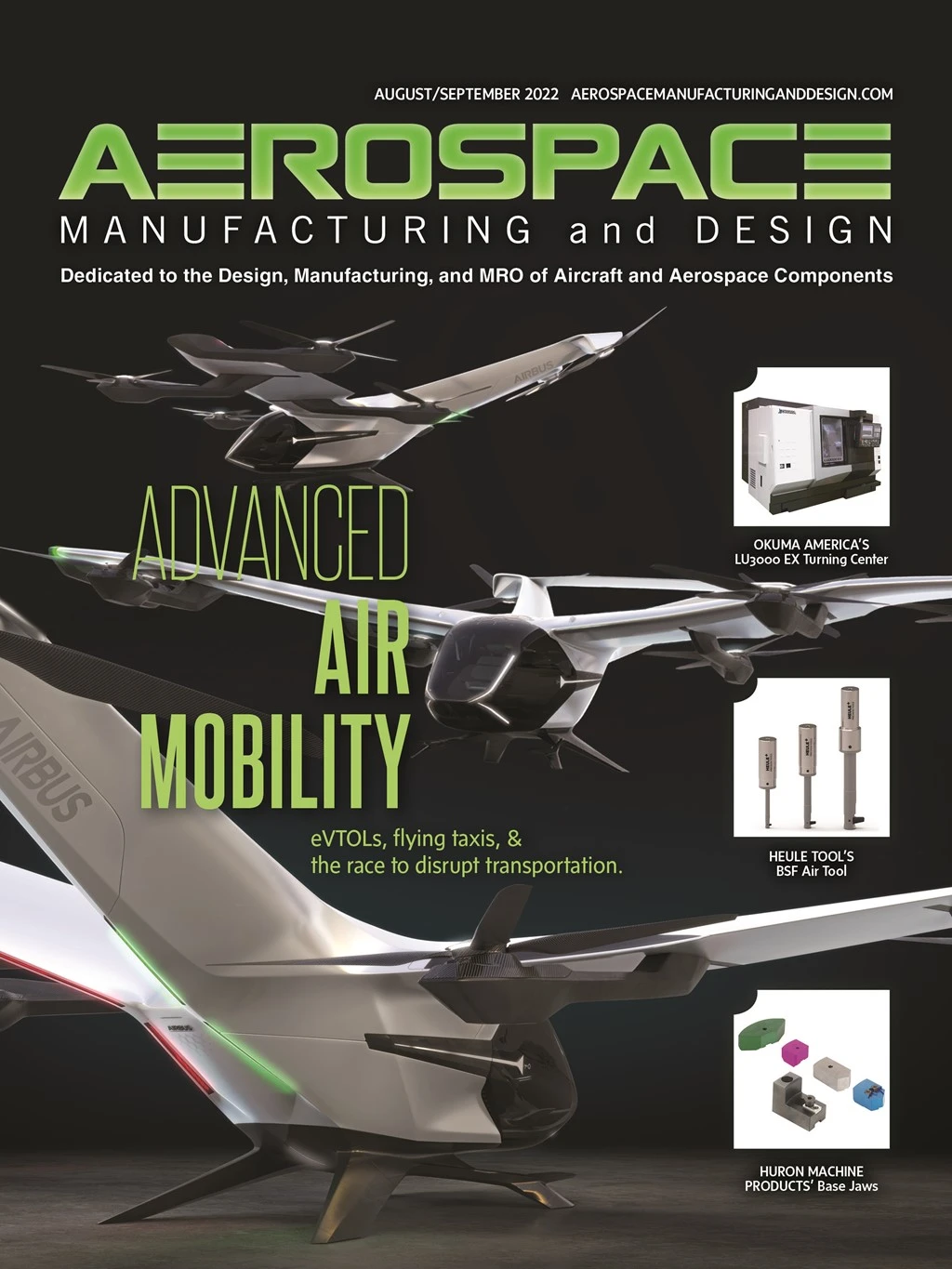
Explore the August September 2022 Issue
Check out more from this issue and find your next story to read.
Latest from Aerospace Manufacturing and Design
- Mastering high-temp alloys with Kennametal Inc.
- Boeing to sell portions of digital aviation solutions
- SMW-Autoblok’s KNCS-matic 3-jaw power chuck
- 3 Questions with an Expert with Allied Machine & Engineering
- Electra raises $115M to pioneer Ultra Short aircraft
- Walter’s WT26 partial- and full-profile thread turning inserts
- April Manufacturing Lunch + Learn with Iscar
- April Manufacturing Lunch + Learn with Insaco