
GIE Media

1) What are circle segment end mills?
Circle segment end mills featuring a cutting edge that is the segment of a large-diameter arc were introduced approximately 25 years ago. Since its cutting-edge shape resembles a barrel profile, terms such as barrel milling cutters or barrel end mills soon became common when referring to these types of end mill.
2) What advantage do circle segment end mills offer vs. traditional ball-nose end mills?
Barrel end mills are intended for advanced-finish and semi-finish machining of 3D surfaces. A prominent advantage of a barrel end mill over a ball-nose end mill is that the number of stepovers – and subsequently, machining time – can be significantly reduced without degrading the surface finish parameters. The large-diameter arc of the end mill cutting edge substantially reduces cusp height.

3) Can any CAM system be used with a circle segment end mill?
The most important thing to remember is that programming circle segment tooling requires a supporting CAM software system. Each CAM defines different relevant processes, for example: Surface, 5-axis, Adv3D, etc. The advantage of the barrel end mill is realized when used for 5-axis, finish-milling operations.
4) What should a CAM programmer take into consideration?
Barrel milling should not always be the answer to finishing all 3D machined surfaces. Some part shapes are not conducive to barrel milling operations. Sometimes, the blend radii of the machined part or the kinetics of the machine result in a complicated CAM tool path which may increase the cycle time compared to using conventional ball-nose milling. This is where the need for a highly skilled programmer making good and effective decisions comes into play.
5) What industry segments can benefit from this technology?
- Aerospace/Power generation: Blisks, impeller blades, and turbines blades
- Medical: Orthopedics, implants, and prosthetics
- Die & Mold: Mold base, core & cavity
6) What are ISCAR’s tool offerings?
ISCAR’s barrel line comprises a variety of solid carbide end mills and Multi-Master heads in different shapes: Oval, Taper, and Lens.
- Multi-Master types: EOB-Oval, ELB-Lens
- Solid Carbide types: EOB-Oval, ELB-Lens, ETB-Taper
- Tool diameters: 0.312" to 0.500" (8mm to 16mm)

Product Features
- Reduces the number of cuts, decreasing process time
- Achieves a much smoother machined surface
- Large radius geometry in the cutting zone increases axial depth of cut during semi-finish, finishing
- Provides extended tool life
- Suitable for machining exotic materials such as titanium, Inconel, stainless steels
For more information: https://www.iscarusa.com
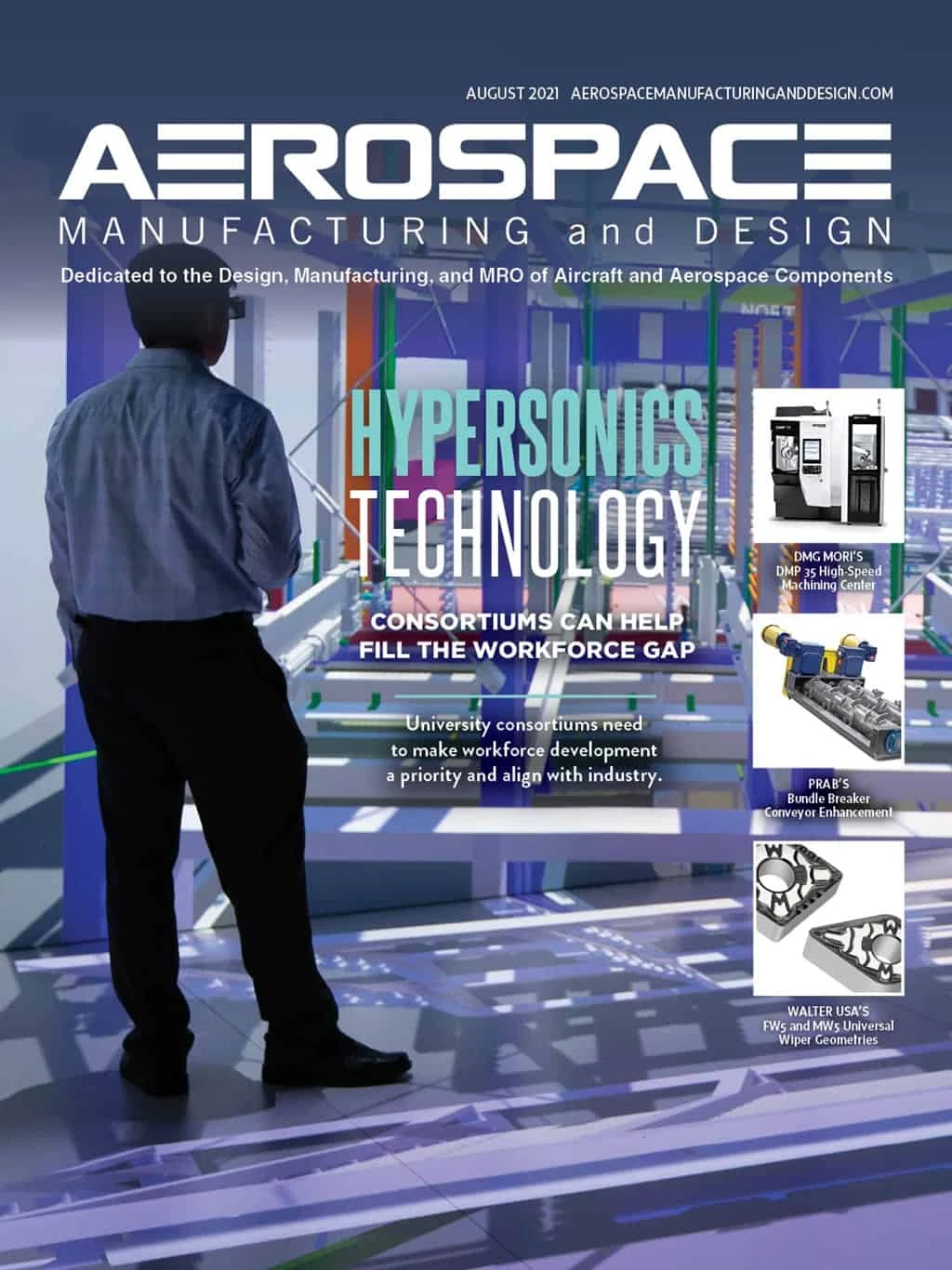
Explore the August 2021 Issue
Check out more from this issue and find your next story to read.
Latest from Aerospace Manufacturing and Design
- Safran Defense & Space opens US defense HQ
- Two miniature absolute encoders join US Digital’s lineup
- Lockheed Martin completes Orion for Artemis II
- Cylinder CMMs for complex symmetrical workpieces
- University of Oklahoma research fuels UAS development
- Motorized vision measuring system
- Everyone's talking tariffs
- Boom Supersonic to launch Symphony engine testing in Colorado