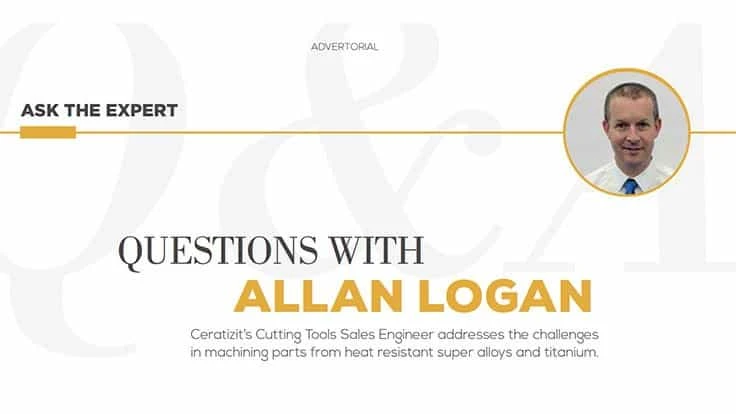

Insight for turning critical, rotating aerospace engine parts.
1. What specific challenges do shops face when turning rotating engine components?
Top of mind are the complex geometries they must produce, the titanium alloys and nickel-based superalloy materials being machined, and the surface quality requirements they must achieve. Productivity is also a challenge due to part geometry that often requires multiple or special tools.
2. How does cutting tool geometry affect productivity?
The rule of thumb for metal cutting is 10% of the heat should go into the material, 80% into the chip, and 10% into the tool. But heat-resistant materials don’t shed heat well in chips created when turning, resulting in rapid tool wear. A round insert is the ideal geometry due to its cutting edge length that dissipates heat, even though the material removed or depth of cut is the same.
3. What turning insert grades are best for these parts – ceramic, CBN, PCD, or carbide?

In first-stage machining, where material removal is key, ceramic grades can run the highest surface feet per minute compared to carbide. For finishing, carbide may not be as productive but it’s more stable and tougher than ceramic with better dimensional accuracy.
CBN lasts longer when finishing nickel-based alloys because it can run at elevated surface speeds compared to carbide and still get reliable performance. PCD in the right application is suitable for finishing titanium alloys as it can run at elevated speeds compared to carbide, but it costs more. Carbide is best for roughing titanium alloys, and carbide finishing heat-resistant super alloys minimizes the possibility of redepositing metal that can happen with ceramics.
4. How does tool choice relate to chip control, management, and safety?
Without good chip control, you’ll be stopping the machine to remove chips more often. If chips aren’t broken, they can create a bird’s nest or string that wraps around the tool or part, requiring the operator to remove them manually before turning can continue. It’s important for machine operator safety for a tool to break chips in a controlled way so they are carried away in a chip conveyor.
5. Is high-pressure coolant an option, and if so, what are the benefits?
In the past, a tool put coolant into the cutting area, but it wasn’t directed precisely to the cutting edge. Now, tool nozzles allow high-pressure coolant to be aimed at the cutting edge to provide a hydraulic wedge between the chip and insert, kicking the chip off the insert much quicker, carrying heat away faster, and shortening chip and insert contact time.
By using high pressure coolant with precision Direct Coolant nozzle technology, you can run twice as fast in titanium alloys or run the same speed but get double the tool life.

Get curated news on YOUR industry.
Enter your email to receive our newsletters.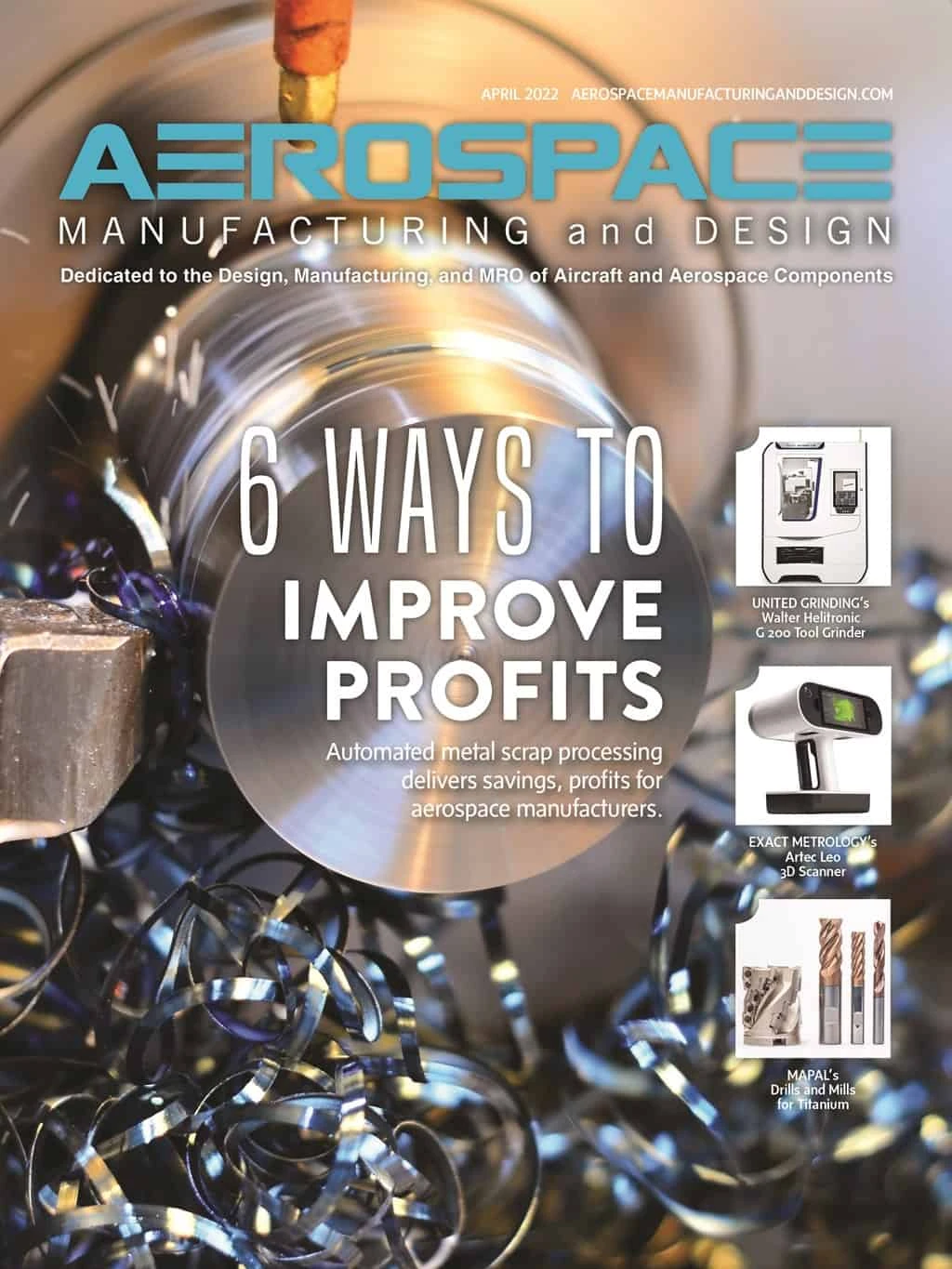
Explore the April 2022 Issue
Check out more from this issue and find your next story to read.
Latest from Aerospace Manufacturing and Design
- Beyond Aero refines its hydrogen-electric light jet
- Americase's advanced protective solutions
- Social media - what are your thoughts
- GE Aerospace secures Air Force engine contract
- Thomson Industries' online sizing and selection tool
- #53 - Manufacturing Matters - 2024 Leaders in Manufacturing Roundtable
- Join us for insights on one of the hottest topics in manufacturing!
- You can still register for March’s Manufacturing Lunch + Learn!