
GIE Media

1 What is BIG DAISHOWA’s most effective round tool holder for high metal removal rates?
Our mechanical milling chuck series offers the highest gripping strength, the most mass, and the highest resistance to bending. From there we need to get more specific about the machine and cutting tool size. For smaller machines (30/40/HSK-A63) choices are based on material. Our Hi-Power series has the highest gripping strength but is more suited for material with lower cutting speed requirements, while the MEGA DS is better suited for aluminum applications where high speed and coolant delivery are critical. For larger machines (50/HSK-A100+) we add a third option, MEGA Perfect Grip. The Perfect Grip holders combine features for high-speed applications along with high gripping strength plus high-volume coolant delivery. This platform gives you all the tools to utilize machines to their limits.
2 How does a mechanical milling chuck operate?
Standard designs for a milling chuck include a solid core (including the taper), a needle bearing cage, and an external nut for clamping. As the nut rotates, the needle bearing cage rolls at a very slight angle to compress the bore of the tool holder core. This basic design is offered by many manufacturers, but we take the design a step further for rigidity and ease of use. When clamping our MEGA DS, HMC Type S, or HMC Type J, the nut makes physical contact with the holder core. This expanded base reduces bending for higher performance and gives operators confidence the holder is fully clamped.
3 What does BIG DAISHOWA offer to improve performance on extended reach applications where component size limits access?
Length-to-diameter ratios more than 6:1 make it more difficult to machine at appropriate speeds. Often the concession to eliminate chatter is to just slow down spindle speeds. BIG DAISHOWA’s Smart Damper system is a mechanical damping design we’ve incorporated into turning, boring, and milling. The SDF milling program uses damped shell mill components mounted on a variety of base taper and length combinations. With passive damping in place and cutting chatter eliminated, it’s possible to restore cutting speeds for insert life and cycle time reductions.
4 When does BIG DAISHOWA recommend using shrink-fit or hydraulic chucks?
When the size of milling chucks is too large for an application, we turn to slimmer clamping options such as shrink-fit or hydraulic chucks. The holders rely on about the same interference fit for gripping but get there from opposite directions. The shrink holder requires heat to expand the steel bore long enough to insert a cutting tool, whereas the bladder in a hydraulic chuck expands inward during clamping. Both holder types have about the same amount of interference, putting them near the same gripping strength. Our focus then shifts to application for selection. Where shrink is a good choice for clearance-restricted roughing applications, the hydraulic chuck can offer better surface finishes and tool life for finishing work. If a facility is not currently equipped and trained for use of shrink-fit holders, we recommend operator-friendly hydraulic chucks for roughing and finishing in difficult-to-reach locations.
5 Should I be concerned about balance for high-speed roughing applications?
Tool assembly balance is always a consideration, but additional balancing isn’t always required. ISO 16084 separates balance requirements between roughing and finishing applications. In our case, all the hydraulic, shrink-fit, and MEGA system tool holders are hard turned after heat treatment and balanced to meet the ISO specification. Additional hard balancing of the assembly may only be required in the most extreme conditions.
For more information: BIG DAISHOWA

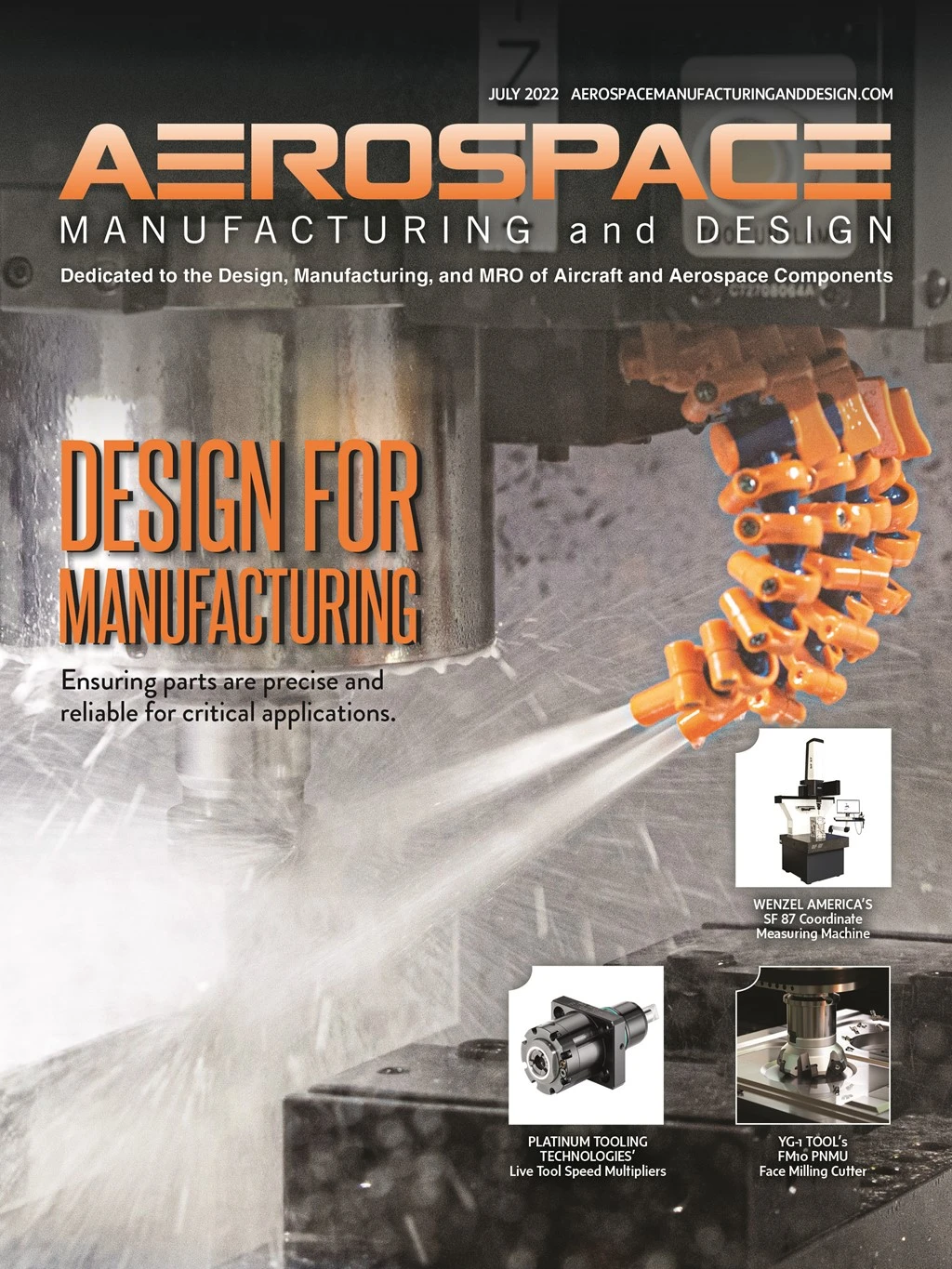
Explore the July 2022 Issue
Check out more from this issue and find your next story to read.
Latest from Aerospace Manufacturing and Design
- Boeing to build US Air Force’s sixth-generation fighter jet
- Sandvik Coromant introduces CoroMill Plura barrel
- #54 - Manufacturing Matters - HMI Solutions for EV Industry from EAO
- Aerospace Industry Outlook returns for spring 2025
- Drop in for an interactive webinar on automation in manufacturing
- SW’s wing rib technology for the aerospace industry
- Mach Industries launches Mach Propulsion
- Murata Machinery USA's MT1065EX twin-spindle CNC turning center