
Quality-control software commercialized by Araqev, a Purdue University-related company, helps end users print products in a few design iterations. This leads to less scrap material and machining time, eliminating the frustrations with 3DP, and improving satisfaction with the final product.
Once a customer has uploaded nominal design files and scanned point cloud data, Araqev’s software uses those inputs to fit machine learning (ML) models that can simulate shape deviations for future printed products.
“The ML models enable our software to derive modifications to the nominal designs, known as compensation plans, so when the modified designs are printed, they’ll exhibit fewer shape deviations compared to the case when the original designs are printed,” says Arman Sabbaghi, associate professor in Purdue’s Department of Statistics in the College of Science and Araqev’s CEO and president.
Araqev’s algorithms enable the transfer of knowledge encoded via ML models across different materials, printers, and shapes in an additive manufacturing system.
Global AM parts distribution network

Materials supplier Equispheres Inc. is entering a partnership with Taiyo Nippon Sanso Corp. (TNSC) to improve the economics and quality of additively manufactured parts in the Japanese market. Equispheres produces specialized additive manufacturing (AM) powder with attributes that achieve 3x faster build rates than legacy aluminum powders.
TNSC, a Japanese-based, global provider of gasses and related welding solutions, focuses on developing total solutions to improve the reliability and reduce the cost of AM part production. Material sales and engineering support for North America and Europe continue to be handled directly by Equispheres. The companies plan to collaborate on R&D projects to develop enhanced applications for the powder and provide further value to the industry.
Aconity3D, a manufacturer of custom, accurate metal AM equipment, also partnered to distribute Equispheres feedstocks to its customers.
The two companies achieved impressive production speeds for 3D printing using the AconityTWO system and Equispheres’ specialized aluminum powders with attributes designed explicitly for AM.
Equispheres powder is used to print the AconitySCAN, a key component of the Aconity3D line of printers, and reduced component production time from 53 hours to 17.5 hours with no impact on mechanical properties and cost savings of more than 50%.
Copper alloy for use in printers

Velo3D Inc. qualified the copper-chromium-niobium alloy GRCop-42 for use in its Sapphire family of printers.
The GRCop-42 alloy was developed by NASA in 1987 to manufacture parts needing high-strength and high-conductivity, such as rocket engine combustion chambers with regenerative cooling. Customers can use the newly developed additive material parameters to produce mission-critical parts with oxidation resistance and high creep strength at temperatures as high as 1,400°F.
Metal AM for engine component repair

GE Aviation’s Loyang facility in Singapore is the first maintenance, repair, and overhaul (MRO) facility worldwide approved to use metal additive manufacturing (AM) for commercial jet engine component repairs. The facility accounts for more than 60% of GE Aviation’s global repair volume.
3D-printed parts are typically printed using STL files generated from CAD drawings, but this only works when producing parts conforming to the blueprint. When repairing used parts, the repair must be customized for individual parts because parts wear differently during service.
Teams are already using additive technology to repair parts in GE Aviation’s CF6 engines, with the next goal being parts on the CFM56.
One example is repairing high-pressure compressor (HPC) blades running at high speeds and tight clearances within aircraft engines. Repairing blade tips formerly required a process of cutting, welding, and grinding to create the proper shape, but GE Aviation established an automated AM process saving time and costs associated with labor and machining. The team created image-analysis software that maps the shape of a used blade and creates customized instructions for the Concept Laser M2 to build a new tip with precise alignment and profile.
The team designed tooling to prepare and print parts efficiently and fine-tuned the repair process, including printing, pre- and post-processing, and inspection. The two big advantages that metal AM provides the site are speed and the near-net-shape product. By using the Concept Laser M2 metal 3D printers, the repaired blade is very close to the final shape when it comes out of the machine, so it takes less labor and equipment to achieve the finished profile.
Wire feed metal 3D printers
NUBURU and Essentium Inc. are developing and manufacturing a blue laser-based metal additive manufacturing (AM) platform for creation of production-grade metal parts with high resolution and fast throughput.
Blue laser technology is being integrated with high-speed extrusion (HSE) 3D printing technology for product development in the first phase, and manufacturing in the second phase. The blue laser is well suited for materials processing applications within AM. Copper, stainless steel, and aluminum reflect much of the infrared wavelengths transmitted by traditional industrial lasers, leading to lower print speed and quality. Blue laser technology enables printing with 10x the build speed and the ability to print with a very high metal density without any post processes.
HSE 3D printing platforms give customers an industrial-scale AM solution allowing them to generate production floor-ready parts at scale quickly and cost-effectively. The technology provides energy-efficient deposition, eliminates porosity, and minimizes warpage during a build.
Metal powders for AM

6K Additive and Morf3D are collaborating to qualify metal powders for additive manufacturing. 6K Additive’s metal powders will be approved for use by Morf3D’s aerospace and defense application customers. Morf3D will manage the printing, characterization, post-processing, and data generation framework to qualify 6K Additive’s sustainably produced powders.
Morf3D will use domestic, sustainably sourced 6K Additive powders to react quickly to customer needs once they’ve completed qualification. The sustainable sourcing of powders and high quality is a key aspect for customer requirements. UniMelt technology upcycles used and end-of-life powders, scrap material, and test parts into feedstock to produce its highly spherical powders. The circular economy reduces cost and waste while gaining access to premium quality metal powers for production.
Commercially available powders include Ti6Al4V (Grade 5 and Grade 23), SS316L, and nickel superalloys Ni718 and Ni625, along with the announced refractory materials.
Get curated news on YOUR industry.
Enter your email to receive our newsletters.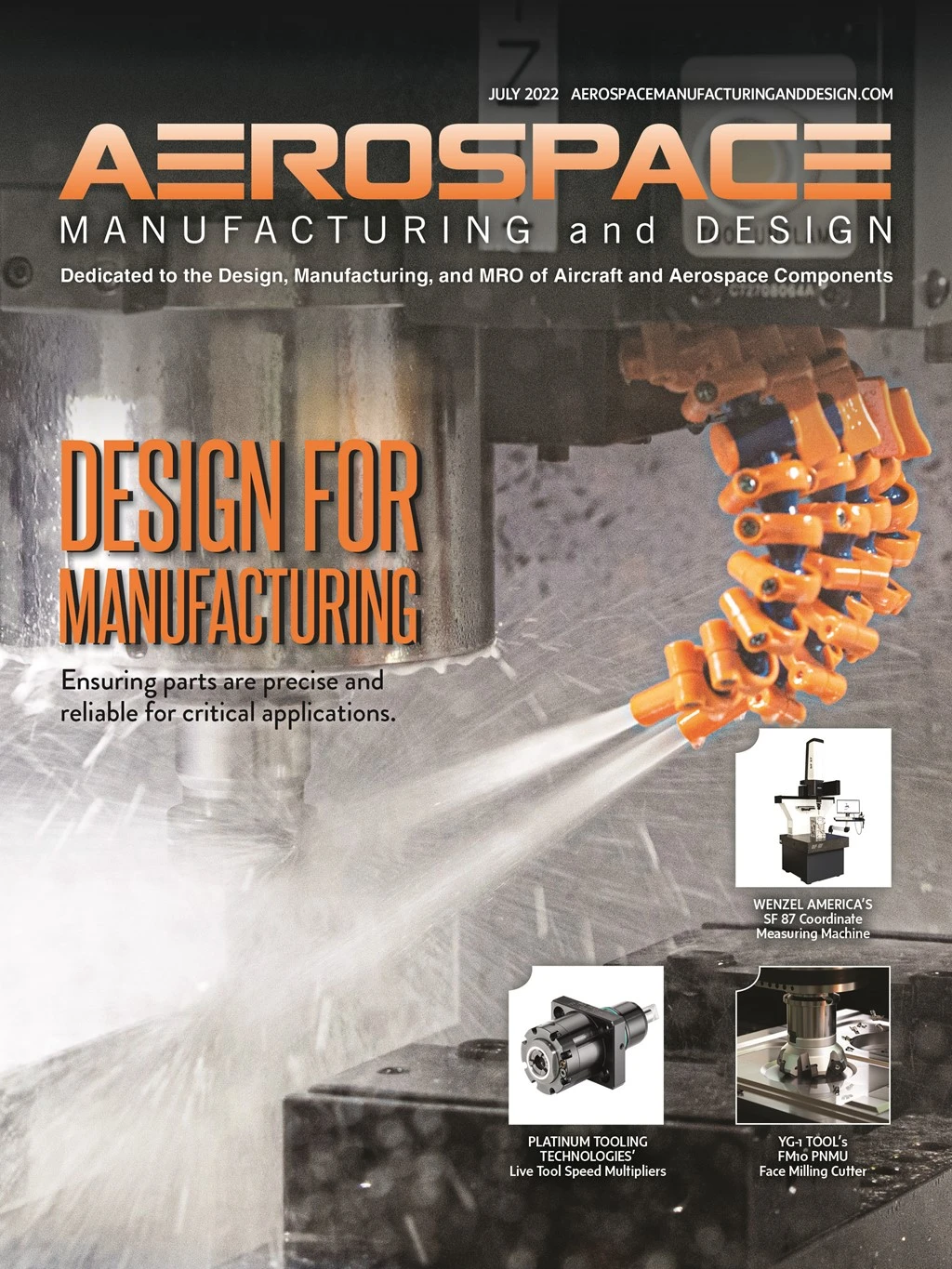
Explore the July 2022 Issue
Check out more from this issue and find your next story to read.
Latest from Aerospace Manufacturing and Design
- Heart Aerospace relocates to Los Angeles
- Fixtureworks introduces Stablelock Clamps
- Piasecki acquires Kaman's KARGO UAV program
- PI Americas’ long-travel XY piezo nanopositioners-scanners
- AAMI project call submission deadline extended to May 12
- Jergens launches cast iron tooling column additions
- Airbus to acquire assets relating to its aircraft production from Spirit AeroSystems
- FANUC America's Cobot and Go web tool