
Quality control (QC) and the processes associated with maintaining it must be an integral piece of any organization involved in aerospace. QC is so critical in aerospace that a standard was created to set system requirements for the challenges organizations face up and down the industry: AS9100. Any organization designing, developing, or providing services in aviation, space, or defense is held to this standard. While AS9100 has many different aspects, one that can be particularly interesting to manage is the concept of suppliers.
The aerospace industry supply chain is complex. The assembler may be getting parts from a fabricator which sourced its material from another supplier. The chain can go many levels deep, so adhering to a standard ensuring quality up and down the line can be very advantageous. It can also be very complicated.
AS9100 standard
The standard states any organization who earns AS9100 certification must “ensure that externally provided processes, products, and services conform to requirements.” In other words, organizations are responsible for any outside processes, products, or services with direct involvement in the business’ operations. The standard continues,
- The organization shall be responsible for the conformity of all externally provided processes, products, and services, including from sources defined by the customer
- The organization shall ensure, when required, customer-designated or approved external providers, including process sources (e.g., special processes), are used
- The organization shall identify and manage the risks associated with the external provision of processes, products, and services, as well as the selection and use of external providers
- The organization shall require external providers apply appropriate controls to their direct and sub-tier external providers, ensuring requirements are met
All the requirements are in the interest of QC and the complexities involved with maintaining that quality among suppliers. An organization adhering to the guidelines must be thoroughly vetted. A supplier must be assured the supplier they’re working with also has achieved AS9100 certification or has a comparable quality management system to ensure their business practices meet the mark.

For certain customers, a fabricator may have a specified list of approved suppliers. Typically, the suppliers on this list are AS9100 compliant. If they aren’t, the customer will need to specially approve a supplier that a fabricator uses.
To confirm the suppliers a fabricator uses remains compliant, they must be reviewed every year. This can be a daunting task depending on the number of suppliers a fabricator uses regularly.
On the very top level, if they have AS9100 certification, it must be up to date. Diving a bit deeper, however, a fabricator can also audit its suppliers. They can do an external audit on the supplier to make sure their requirements are being met. In the case where a corrective action is issued by the fabricator against the supplier, that may need to be audited as well.
Counterfeit identification
In addition to external audits a fabricator must do with its suppliers to remain AS9100 compliant, internal processes must be in place related to suppliers as well. As a fabricator, an organization must ensure everyone on staff is trained in the prevention of counterfeit parts. As part of the onboarding process, it’s recommended that anyone handling or inspecting parts from suppliers go through training on this topic, then put best practices into action. First and foremost, products must be inspected at receiving. During this inspection, all the certifications should be examined to ensure the part lot and the date code match the documents received. The manufacturer’s logo needs to match; parts need to meet print requirements. If there’s suspicion of counterfeit parts, the quality manager should have an open door to report any inconsistencies to the purchasing management. At this point, all parts received in the batch should be dispositioned as nonconforming and separated from the good parts, so they don’t enter the supply chain. Then, the nonconforming part must be reported to the appropriate authorities and a note made not to work with the questionable supplier again.
Outward communication

The best way to prevent inconsistencies and confusion upon receiving is to ensure accuracy when communicating with suppliers. Processes and internal reviews should be devised so nothing is overlooked or misstated when sending requirements to the suppliers. It’s difficult to stress the importance of this exercise. A fabricator must be confident that all communication sent for requirements is 100% correct. The planning department should review everything before it’s sent to the supplier.
However, there still should be a rigorous inspection process when the materials come in. Even though it may have been communicated by the fabricator to the supplier correctly, if the material comes in with incorrect specifications and it’s not caught, it’s a hit on the fabricator’s quality. Anything that’s outsourced to a supplier making its way through the door needs to be inspected by a quality department before it enters the workflow.
Maintaining compliance with AS9100 requires a yearly review of performance and certifications. During this annual audit, the governing board goes through and verifies everything the fabricator does in its processes and job instructions meet the standards key to the precision of the entire industry.
About the author: Derek Jenkins is the quality manager for WB Industries, a custom metal fabrication company that works to industry standards including NASA, Boeing, Lockheed Martin, AMS, AISC, IBC, ASTM, and MIL specs.
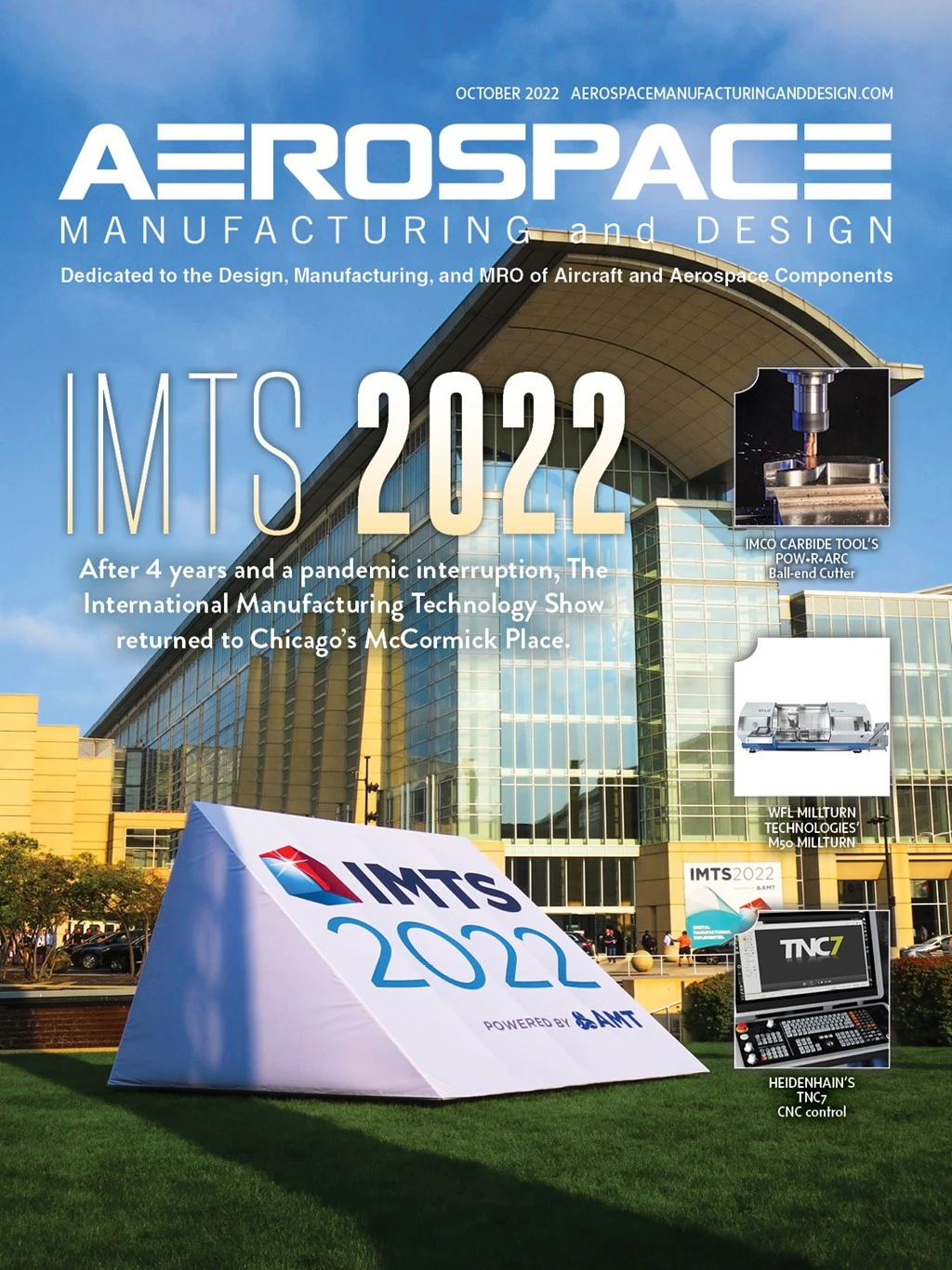
Explore the October 2022 Issue
Check out more from this issue and find your next story to read.
Latest from Aerospace Manufacturing and Design
- AAMI project call submission deadline extended to May 12
- Jergens launches cast iron tooling column additions
- Airbus to acquire assets relating to its aircraft production from Spirit AeroSystems
- FANUC America's Cobot and Go web tool
- Chicago Innovation Days 2025: Shaping the future of manufacturing
- High-density DC/DC converters for mission-critical applications
- #59 - Manufacturing Matters: Additive manufacturing trends, innovations
- ACE at 150: A legacy of innovation and industry leadership