
Manufacturers of complex, highly engineered products such as aircraft components commit to perfection – every time. There is no wiggle room.
With extremely complex aircraft production, manufacturers must carefully manage quality processes, applying much attention to every step. That demands a deep understanding of how to manage and adapt to dynamic production, quality, safety, and supply chain issues while meeting regulatory requirements.
Managing complex, frequently changing production orders is difficult due to the many factors that can impair delivery of quality products. Quality processes must be dynamic in inspection and every facet of design, production, and test. Thanks to Industry 4.0 strategies and modern manufacturing solutions, these quality challenges have become much easier to manage and overcome.
One size doesn’t fit all
The traditional focus of aircraft production has been on the materials. The root of most quality issues could be attributed to brittle fractures, corrosion, metal fatigue, or other factors. Today’s aircraft production, however, comprises advanced, highly engineered technologies using resistant materials. Product creation uses highly specialized, complex processes and electronic systems. A generic operations management software solution may no longer address those extreme levels of complexity.
Significantly more complex parts can be sourced from a global supply chain, so greater consideration must be applied throughout the assembly process to bring it all together. Uncertainty creates new challenges for supply chain visibility and quality management. Assuring quality of so many component parts and the finished product requires a better, more integrated approach to quality.
Data-driven quality excellence
Industry 4.0 represents an evolution in manufacturing with advanced technologies increasingly necessary to meet stringent quality requirements. Enabling technologies include Industrial Internet of Things (IIoT), digital thread, augmented reality (AR), and predictive analytics.
Quality 4.0 describes a data-driven approach to quality performed during production, involving the product, processes, planning, compliance, and standards. It builds upon, rather than replaces, traditional quality methods, using many of the same new technologies as its industrial counterpart, including machine learning, connected devices, cloud computing, and digital twins to transform an organization’s work processes and eradicate possible product or process defects. The emergence of Quality 4.0 promises to further change workplace culture by increasing reliance on data and more deeply integrating quality as part of the entire approach to creating products.
Quality 4.0 integrates operational and quality assurance (QA) concerns from the start and through the design phase. This includes how a product is conceptualized and engineered. Recent industry findings show most of the market doesn’t have automated design transfer processes. Manual processes leave room for error, whether internal or from communicating designs and changes with the supply chain.
Beyond design, Quality 4.0 uses process-focused machine learning to reduce waste, minimize rework, and optimize production parameters. In addition, it addresses product performance issues after delivery, using feedback from the field to update product software remotely, maintain customer satisfaction, and ultimately secure repeat business. It’s becoming an inseparable companion to Industry 4.0.
However, quality doesn’t apply only to select segments of manufacturing. The inclusive nature of Quality 4.0 can instill a comprehensive approach to quality in the manufacturing organization, making the transformative power of data an integral part of the corporate mindset. Compliance at all levels of an organization contribute to an overall culture of quality.
Power of closed-loop systems
No production process can operate perfectly, 100% of the time. Changing conditions trigger unforeseen incidents that need to be remedied. Those experienced in quality understand it’s all about the process toward perfection. How are you ensuring quality is built into the process to identify issues early? What do you do after identifying a defect? Did any external factors contribute to this issue? What changes can you make to the inspection plan or test procedure to prevent this issue from recurring?
Initiate a mindset where every production process has an associated, related quality process. Imagine a future where a one-to-one relationship exists, measuring quality continuously. It then would be possible to achieve perfect quality, regardless of what events randomly occur. Metrics and key performance indicators (KPI) are reviewed daily at every work center to identify areas for potential improvement before issues occur.
In this closed-loop system, every production process has a quality corollary that provides feedback to stop the process, allow it to proceed, or make an adjustment in real-time. This system isn’t subject to fatigue or manual error. A closed-loop quality system designed for aircraft production is essential to achieving higher levels of quality, improving cycle times, and ensuring regulatory compliance with AS9100 standards.
The path forward
A decade ago, the idea of focusing QA on product design, market research, suppliers, services surrounding the product, or other factors affecting customer satisfaction were out of the question. Product designs were understood as emanating from a higher authority; quality was about executing those designs on the assembly line, regardless of their shortcomings.
Today, many companies are rethinking how business gets done. What was status quo in 2018 may never be possible again. Increasingly, manufacturers are getting smarter. Greater knowledge is available, and that means better intelligence to build products right the first time, with greater efficiency and performance.
It’s critical that quality remains a core focus of digital transformation in manufacturing, integrated into specific aspects of the Industry 4.0 vision, including process design, intelligent poka-yoke, integration of quality data in the digital thread and, ultimately, integration of quality management practices throughout the manufacturing process.
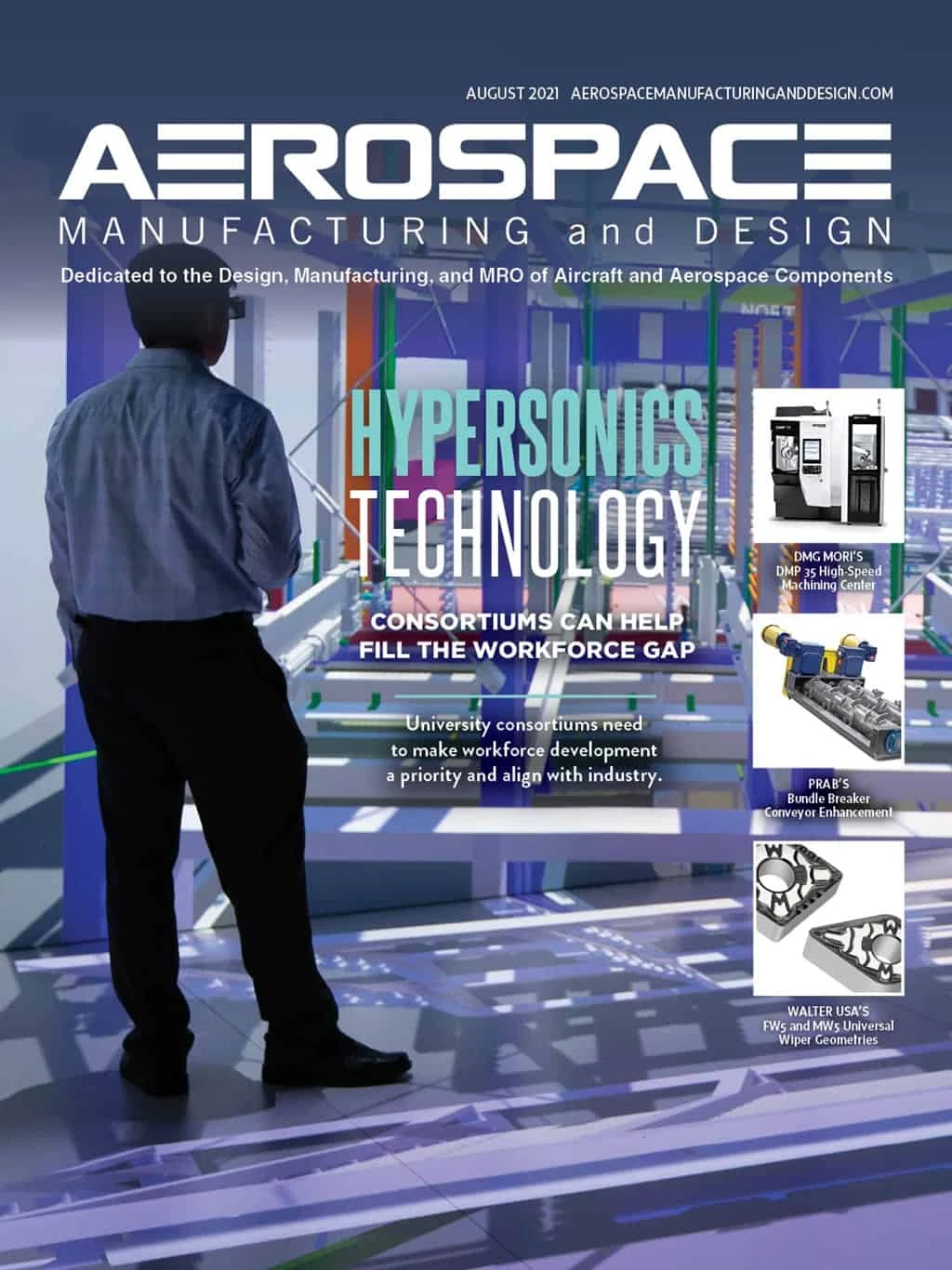
Explore the August 2021 Issue
Check out more from this issue and find your next story to read.
Latest from Aerospace Manufacturing and Design
- Taiwan’s China Airlines orders Boeing 777X passenger, freighter jets
- Reamer re-tipping extends life of legacy tooling
- Revitalizing the Defense Maritime Industrial Base with Blue Forge Alliance
- Safran Defense & Space opens US defense HQ
- Two miniature absolute encoders join US Digital’s lineup
- Lockheed Martin completes Orion for Artemis II
- Cylinder CMMs for complex symmetrical workpieces
- University of Oklahoma research fuels UAS development