
Flash memory storage for aerospace applications must log essential data with mission-critical reliability, despite being subject to vibration, shock, extreme temperatures, moisture, dust, and altitude.
Whether flash storage records data for military jets, helicopter black boxes, or unmanned aerial vehicles (UAVs), failing in harsh conditions can compromise a mission or, if safety is jeopardized, generate liability concerns.
Flash, controller, and firmware must unfailingly perform to strict military standards such as MIL-STD-810G environmental testing. Even flash storage failure on nonessential features such as commercial in-flight entertainment and WiFi services could result in serious reputational damage, along with high field service and warranty costs.
Customizing memory devices for mechanical ruggedness ensures reliability while providing applicable storage capacity and form factors. Products should be built with a controlled bill of materials (BOM), so the flash, controller, and firmware are all locked in the part number.
While most of the flash storage industry promotes testing to ensure product performance within specified temperature ranges, aerospace flash manufacturers exceed minimum standards to commit to high reliability. One of the most common causes of memory device failure for aerospace original equipment manufacturers (OEMs) is testing that doesn’t appropriately replicate real-world conditions.
The only way aerospace OEMs can ensure their products will withstand real-world vibration and temperature abuse is to put the flash storage components through the paces with a highly accelerated life test (HALT) and highly accelerated stress screen (HASS).
HALT and HASS techniques avoid problems of slower, traditional methods that only test to minimum specifications. They quickly expose weak links in a product by testing well beyond minimum specs so that any reliability problems can be fixed before they become expensive performance, field service, warranty, or liability issues.

Accelerated qualification testing
In HALT, engineers expose products to extreme environmental conditions they might experience after installation. Testers repeatedly raise and lower temperatures and expose devices to high levels of vibration. Conditions also can be adjusted to meet specific needs.
HALT’s four steps – thermal step testing, rapid thermal cycling, vibration step testing, and combined environment testing – use one computer to manage testing conditions while another runs host applications in which the memory will be used to emulate real operating conditions as closely as possible.
HASS testing, a screening method to monitor the quality and uniformity of manufacturing by finding production flaws and product defects, often follows HALT as the two are complementary.
HASS stresses are based on the limits identified through HALT, and combinations of stresses are applied simultaneously. The screening pushes the product beyond its operating limits to cause product failures and reveal inherent defects.
Because HASS stresses are more rigorous than those rendered by conventional approaches, testing accelerates detection of design issues. Problems can be corrected and the flash storage device ruggedized to prevent failure.

Leveraging tests
Typically, HALT and HASS tests ensure that when a design goes to production, it exceeds promised specifications in temperature, vibration, or other areas.
When non-volatile flash storage supplier Delkin Devices performs HALT and HASS as well as design verification testing and ongoing reliability testing, engineers analyze results in-house so design changes can be made before the flash storage is used in aerospace OEM devices.
Often these tests can determine improvements that will allow a product’s design to exceed specifications. For example, traces can be modified, or pad sizes changed to improve soldering when testers discover breaks or bad electrical connections. Alternatively, connectors can be changed or repositioned to improve overall part performance or longevity.
Aerospace OEMs can ensure a storage device will work as expected in operating conditions by partnering with a manufacturer offering accelerated testing reliability services, which helps determine failure modes and root causes plus the functional operating limits and destruct limits of flash storage cards. This information can be used to make necessary corrective improvements to significantly improve product reliability.
For aerospace OEMs, the test process up to the release of a new design is often like verifying all parts in the chain. Designers improve or replace the presumed weakest link before testing resumes. Then the second weakest link is determined and improved. This process continues until a part well exceeds its specifications to ensure the design and material are solid, with assurance that the part in mass production excels.
Given the extended life cycles of aerospace military programs, flash storage products with long-term availability are desired to avoid or minimize re-qualifications and ensure consistent performance and host compatibility. Custom testing and product modifications should be performed to withstand the unique conditions.
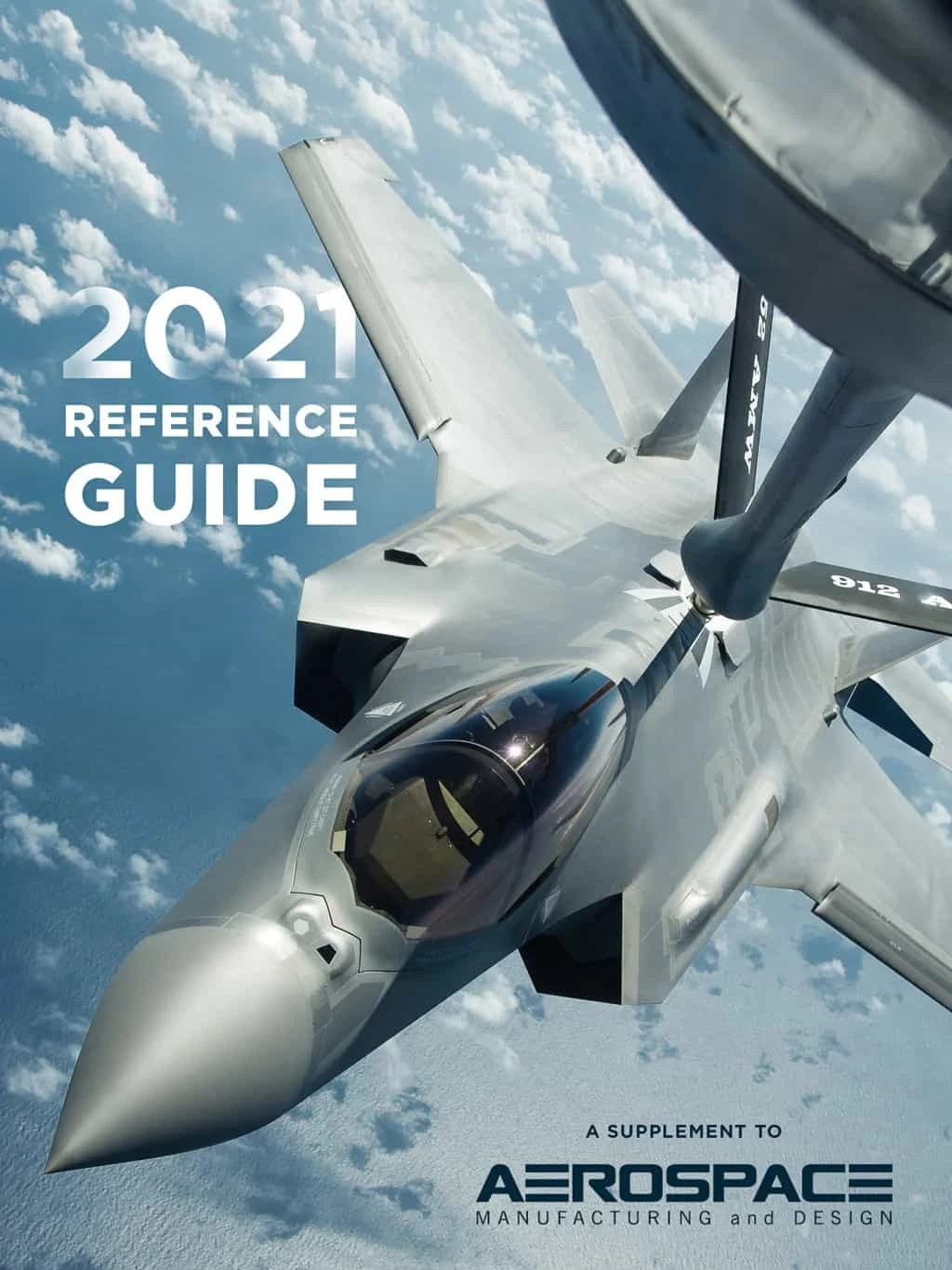
Explore the AMD Reference Guide 2021 Issue
Check out more from this issue and find your next story to read.
Latest from Aerospace Manufacturing and Design
- GE Aerospace secures Air Force engine contract
- Thomson Industries' online sizing and selection tool
- #53 - Manufacturing Matters - 2024 Leaders in Manufacturing Roundtable
- Join us for insights on one of the hottest topics in manufacturing!
- You can still register for March’s Manufacturing Lunch + Learn!
- Ohio creates Youngstown Innovation Hub for Aerospace and Defense
- Tormach’s Chip Conveyor Kit for the 1500MX CNC Mill
- How to Reduce First Article Inspection Creation Time by 70% to 90% with DISCUS Software