
based on customer needs and applications.
Advanced case-hardening surface treatment can significantly enhance wear and fatigue resistance, increasing material performance to improve the reliability and durability of aluminum, stainless steel, and titanium.
Traditionally, surface treatment has involved carburizing, salt-bath nitrocarburizing, or gas nitriding. Each process has advantages and disadvantages, but those seeking more precise control of diffusion layer formation, case hardening depth, and preserving component dimensions are increasingly turning to advanced pulse plasma nitriding.
Although pulse plasma has been used for decades, new controls for the DC pulsing signal and improved chamber design and construction allow more precise temperature control and uniform distribution of the heat zone throughout the hot-wall chamber – resulting in consistent, uniform nitriding batch-to-batch with less gas consumption.
The benefits are more precise control of the diffusion layers, and its broader appeal to heat treat more diverse materials that include titanium, stainless steel, and aluminum.
Commercial heat treat shops and high-volume part producers can select from multiple system configurations offering flexibility, efficiency, repeatability, and throughput optimization.
The number and range of aerospace pulse plasma applications is rapidly growing. Low-temperature (350°C to 430°C) pulse plasma nitriding and nitrocarburizing of tools and components made of rust- and acid-resistant stainless steel increase wear resistance without sacrificing corrosion resistance. High-temperature (600°C to 900°C) pulse plasma nitriding of titanium or titanium alloy components supports turbine parts to aircraft undercarriage components to satellite components.
Traditional process disadvantages
Case-hardening steel and steel alloys via traditional approaches – carburizing, nitrocarburizing – requires heating the part to hotter than A1 temperature (727°C) on the Iron-Carbon diagram, usually between 900°C to 930°C. Since the solubility of carbon is higher in the austenitic state than the ferritic state; a fully austenitic state is required for carburizing.
The high temperatures and time-at-temperature associated with carburizing can distort parts. Therefore, a post-carburizing heat treatment is required, at a minimum, to reduce internal part stresses. Depending on the part, and its geometric tolerances, limited machining may also be required.
An alternative to carburizing is nitriding, a lower-temperature, time-dependent, thermo-chemical process that diffuses nitrogen into the metal’s surface. One method, salt bath nitriding, requires liquid immersion, and is typically conducted at 550°C to 570°C. Donating the nitrogen is a nitrogen-containing salt, such as sodium cyanide, often greater than 50% in concentration. This requires intense washing to remove the residual cyanide, mandating costly disposal of salt and washing lye, environmental handling costs, and safety and operational liabilities.
Gas nitriding (500°C) and gas nitrocarburizing (540°C to 580°C) are universally accepted procedures, and typically require a high concentration of ammonia (NH3) and considerable carrier gas flow (normal pressure process) compared with pulse plasma nitriding. The elemental nitrogen gas diffuses into iron and forms hard nitrides. The reduced temperature, compared to carburizing, doesn’t require quenching, lowering the chance for distortion and cracking. However, gas nitriding requires flammable gases such as ammonia, high gas consumption, and it can’t treat rust- and acid-resistant steels.
Recent advancements in pulse plasma nitriding provide a new level of precision and control, resulting in uniform and consistent case hardening and enabling the use of environmentally friendly gases. (See sidebar below)

Nitriding stainless steel
Stainless steel has a natural passivation layer of chromium oxide which inhibits corrosion. Bringing nitrogen into the material requires removal of the chromium oxide layer. Stainless steels can be nitrided in salt baths, but only by sacrificing some corrosion resistance. With gas nitriding, removing the passivation layer requires applying a special chemistry.
In PVA TePla’s PlaTeG PulsPlasma nitriding, the treatment is applied directly through controlled ionic bombardment of the surface. With a nitriding temperature <450°C, and with exact control of the gas mixture, the material surface can be treated without reducing the material’s corrosion resistance.
Increased throughput
Nitriding in batches typically requires waiting for the prior batch to be treated, cooled, and unloaded before a new batch can be started. Innovation in furnace design, through an optimized mechanical operation, increases efficiency and production capacity. While the actual time for nitriding doesn’t change, efficient loading and unloading play an important part. Shuttle and tandem extensions can streamline the batch process.
With a shuttle extension, an additional vacuum chamber bottom may be added to a furnace. During a running nitriding process, users can unload an earlier batch and load/prepare a subsequent batch on the second vacuum chamber. The cycle time for two consecutive batches is reduced because of the overlapping time for unloading/loading a vacuum chamber with the treatment time of the running process.
With a tandem extension, two complete vacuum chambers are operated alternately by the vacuum pumps, the process gas supply, the plasma generator, and the system’s control unit. During unattended operations, an automatic process can be started and controlled for both batches in succession. With this type of operational structure, it’s possible to increase overall nitriding capacity by 30% to 60% annually.
Because plasma nitriding uses environmentally friendly nitrogen and hydrogen, the furnaces can be collocated with furnaces placed next to drilling machines as pulse plasma nitriding systems produce no polluting gases.
Pulse plasma offers significantly more precision in nitriding through the control of the mixture of gases, glow discharge intervals, the design of the pulsed signal, and the use of a highly insulated hot-wall nitride furnace. With innovative furnace designs to streamline batch management in nitriding operations, aerospace manufacturers that depend on nitriding components can benefit from greater uniformity of results, better-protected materials, and increased throughput.
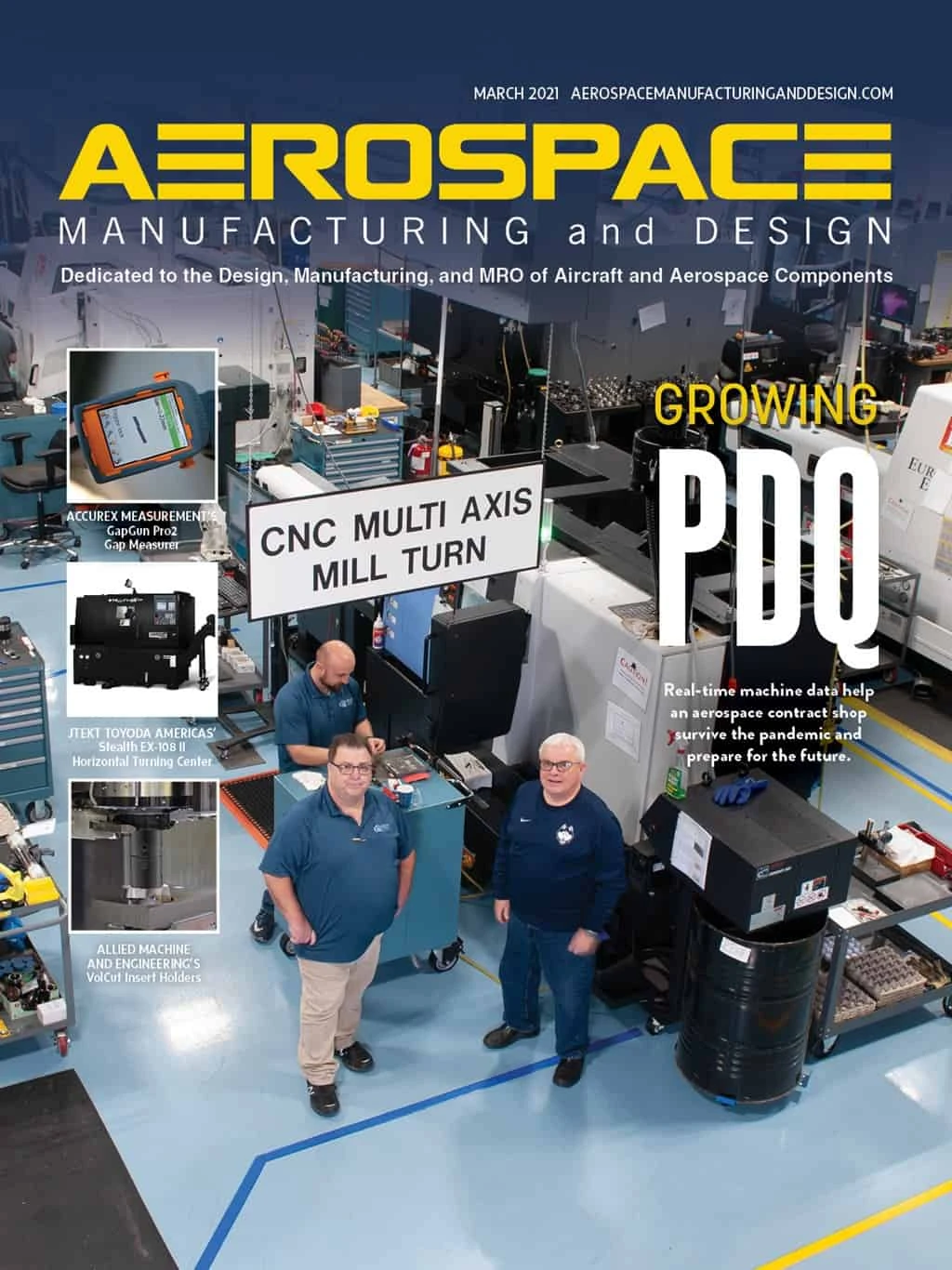
Explore the March 2021 Issue
Check out more from this issue and find your next story to read.
Latest from Aerospace Manufacturing and Design
- Essential strategies to protect your data
- NASA selects instruments for Artemis lunar terrain vehicle
- Twin-cutter boring head
- Bell awarded funding for X-plane build phase of SPRINT program
- Shaft coupling clamps
- #46 Lunch + Learn Podcast with SMW Autoblok
- Gleason Corp. acquires the Intra Group of Companies
- Thread milling cutter reduces cutting pressure, vibration