
Prusa Research announced production of its new Prusa Pro HT90 3D printer for industrial 3D printing. The printer’s delta kinematics boast versatility, higher speeds, better print quality, unlimited third-party material compatibility (no vendor lock), and user data security. The printer offers three running modes: offline, local, and fully online. In the online mode, the printer is fully integrated into the secure Prusa Connect remote print management system. The HT90 has already been beta-tested by selected companies and is actively used in production.
Software defined process qualification for laser powder bed fusion
Dyndrite has been selected by AFWERX for an AFVentures Open Topic 24.D Phase I cohort award. The Dyndrite selection will focus on defining and commercializing a Software Defined Process Qualification (SDP Qual) Process for laser powder bed fusion (LPBF) to address the most pressing 3D metal printing qualification/requalification challenges in the Department of the Air Force (DAF). A rigorous qualification process is essential to ensure that all standards for quality and safety are consistently met. Dyndrite addresses these needs by incorporating scriptable workflows into qualification, and by automating laborious manual tasks that could increase the time and resources associated with qualification.
IMTS Booth #432307
3D-printed components for Airbus A350

Liebherr-Aerospace has successfully integrated a 3D-printed flex shaft in the Airbus A350 high lift system. The unit has been approved by Airbus and the European Union Aviation Safety Agency (EASA) for serial production. The flex shaft was produced from titanium powder using Additive Layer Manufacturing (ALM). Using this method, Liebherr replaced a traditionally manufactured assembly of seven parts with a single additively manufactured part, improving reliability and weight reduction. The flex shaft is part of the high lift system integrated in the flap system’s active differential gearbox. The flex shaft transmits the rotary movement to a position sensor and compensates for an angle and axis misalignment between gearbox and sensor.
Vision Miner acquires AddWise
Vision Miner has acquired AddWise for $14 million. This move solidifies Vision Miner’s position in the additive manufacturing (AM) industry, enhancing its in-house manufacturing capabilities and expanding its global footprint. “By combining our eight years of experience and success in the industry with AddWise’s advanced manufacturing capabilities, we’re now better positioned than ever to deliver the most innovative and reliable industrial 3D printing solutions to our global customer base,” says Patrick Smith, founder & CEO of Vision Miner.
Additive manufacturing market to be worth $93.36B by 2031
According to a new market research report, the additive manufacturing (AM) market is expected to be worth $93.36 billion by 2031, at a compound annual growth rate (CAGR) of 20.3% from 2024 to 2031. The growth of the AM market is driven by the increasing need to produce complex parts, reduce manufacturing expenses, and minimize waste. The use of 3D printers to produce functional end-use parts, composite 3D printing, use of 3D printing in regenerative medicine, and spending in the aerospace & defense sector are expected to offer significant growth opportunities for players operating in the AM market. However, restricted build sizes, material constraints, high pre- and post-processing costs, concerns of piracy, and a lack of skilled labor may restrain growth. On-demand production of spare parts, increased product customization, and the use of artificial intelligence (AI) in 3D printing are prominent trends.
New sales partnership, powder handling system

Xact Metal announced its sales and service partnership with Indicate Technologies in North America and the launch of a new powder handling system. The partnership aims to expand access to metal 3D printing for small- to medium-sized companies and decentralize additive manufacturing. With a focus on the western United States and experience handling 3D printers, the Indicate Technologies team will provide training, technical support, and maintenance for Xact Metal printers.
Xact Metal also introduced an improved powder handling system that stands separately from the XM200G metal 3D printer. Powder containers can be pulled directly from the XM200G and fit onto the system for automatic, hands-free sieving. The refreshed powder can then be transferred to a fresh capsule by opening shut-off valves, simplifying powder handling.
IMTS Booth #433234
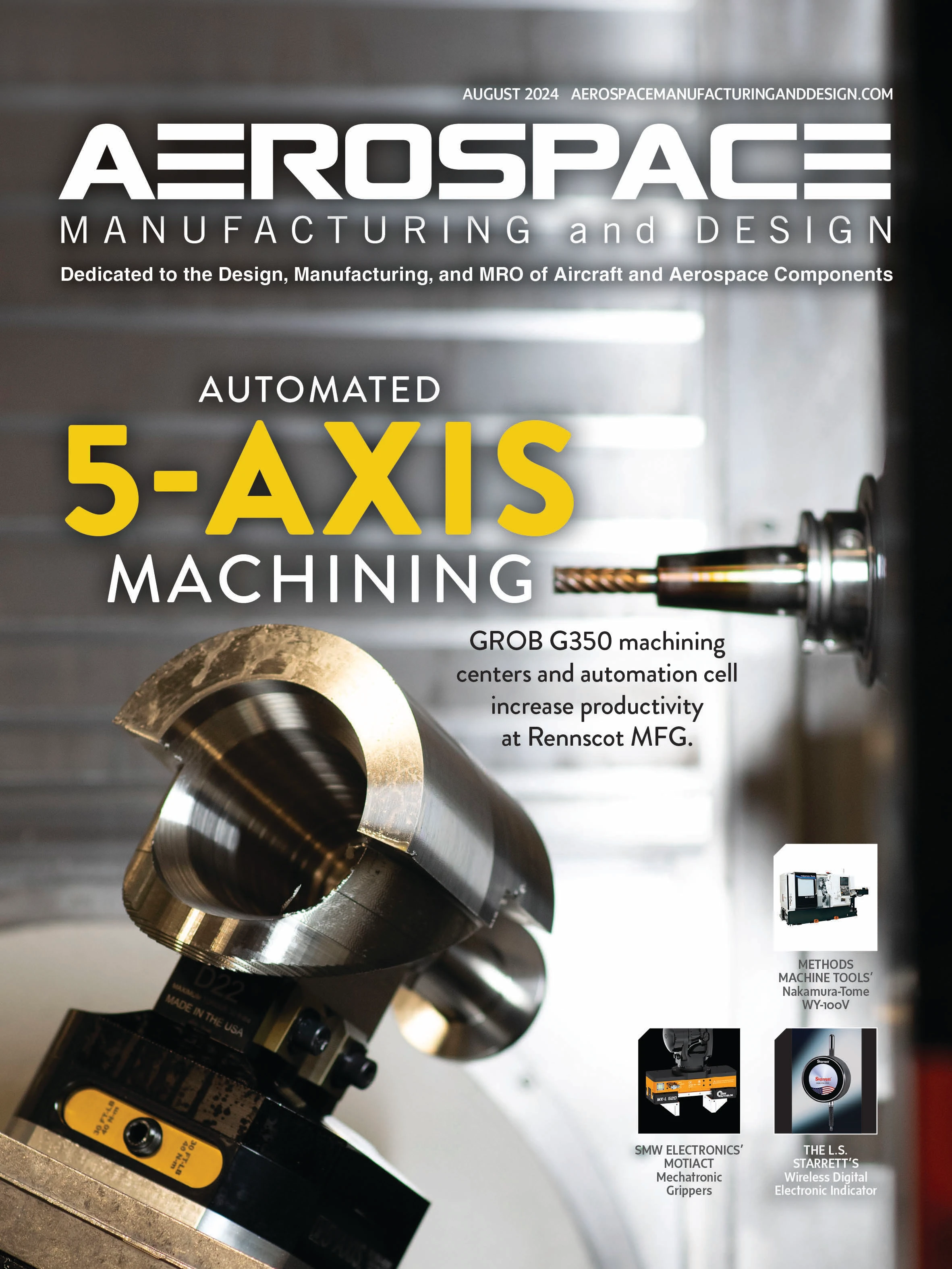
Explore the August 2024 Issue
Check out more from this issue and find your next story to read.
Latest from Aerospace Manufacturing and Design
- Piasecki acquires Kaman's KARGO UAV program
- PI Americas’ long-travel XY piezo nanopositioners-scanners
- AAMI project call submission deadline extended to May 12
- Jergens launches cast iron tooling column additions
- Airbus to acquire assets relating to its aircraft production from Spirit AeroSystems
- FANUC America's Cobot and Go web tool
- Chicago Innovation Days 2025: Shaping the future of manufacturing
- High-density DC/DC converters for mission-critical applications