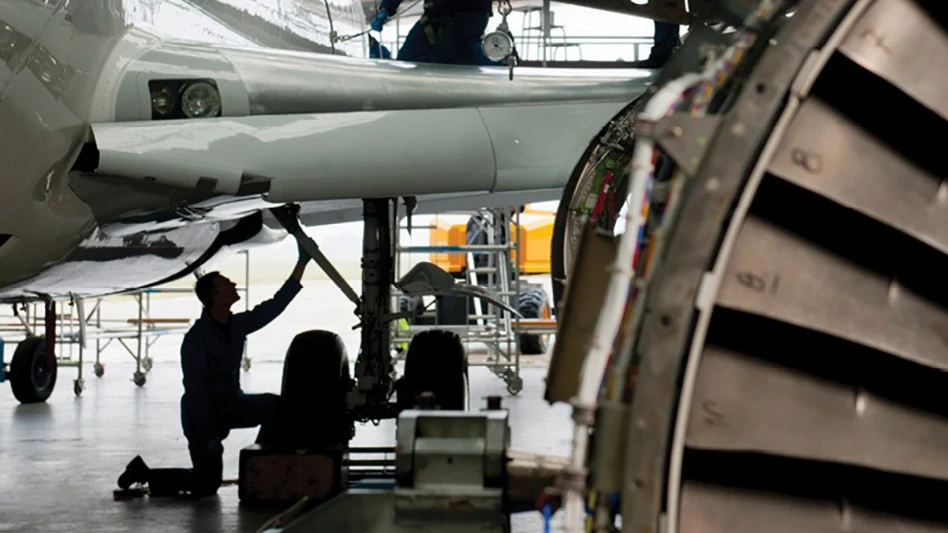
SHUTTERSTOCK

Photo credit: SHUTTERSTOCK
For an industry characterized by technological advancements, many aerospace manufacturers are slow to elevate waste management and recovery processes. Too often, these processes are considered secondary to production. That approach will gradually cut into an organization’s bottom line, as environmental compliance becomes more tightly regulated and the shift to the circular economy accelerates.
Aerospace manufacturing facilities have the potential to produce hundreds of waste streams – enough to keep a plant’s entire environment, health, and safety department awake at night. Lacking adequate processes to cost-effectively manage waste streams and environmental compliance puts aerospace manufacturing companies at risk for millions of dollars in penalties and fines.
Unfortunately, the battle for capital expenditure continues to be the biggest hurdle facing environmental compliance managers and providers of waste reduction solutions. Here are five suggestions for getting stakeholders on board and implementing waste stream processing advancements in aerospace manufacturing plants.
1. Educate stakeholders about liability risks and begin to shift perceptions about environmental compliance from burdensome expenses to lower raw materials costs and increased metal scrap value.
Environmental responsibility and sustainability are equally important to a manufacturer’s bottom line, due to the steep financial penalties associated with failing to comply with local, state, and federal waste regulations. However, establishing processes supporting sustainability also lowers costs, and in many cases, even generates revenue.
Hazardous waste is one of the most strictly enforced regulations across the country – be sure stakeholders are aware of the scope of metal scrap and fluid disposal liabilities. Storing spent cutting fluids on-site is an environmental risk, but chips and turnings saturated with hazardous fluids can also become a liability for the manufacturer if a lawsuit is filed against a recycler that disposes of hazardous materials improperly.
The more used coolant or machine oil a manufacturer sends to the recycler, the greater the chance of being implicated if disposal problems arise. By proactively addressing fluid and chip remediation, manufacturers can help mitigate liability risks by proving good intent.

2. Establish an environmental compliance program.
At minimum, manufacturers should use ISO 14001 as a baseline to develop an environmental compliance program. Although ISO 14001 doesn’t state specific requirements for environmental performance, it establishes criteria companies can follow to develop an effective environmental management system.
Third-party accredited certification is available for the standard, though it’s not a requirement. Plants will benefit from the guidance the standard provides without completing the certification process. ISO 14001 provides assurances to company management, employees, regulators, customers, and the public that the operation’s environmental impact is being measured and improved. Meeting the criteria of the standard also reduces waste management costs and lowers consumption of energy and materials.
3. Identify aspects of operations that’ll mitigate risks or yield material savings.
A company’s machining operation is a smart place to begin an environmental, health, and safety assessment. Equipment such as screw machines, gantry mills, CNC lathes, and drills can generate large quantities of hazardous scrap metal and coolant wastes. Reclaiming and recycling these materials improves workplace safety, reduces environmental impact, and can yield significant bottom-line benefits.
Grinding/honing operations, cleaning processes, and even recycling practices related to wash and mop water, should also be assessed. As water becomes an increasingly precious commodity, implementing strategies for recycling and reclaiming process water and reducing wastewater volumes will contribute to lower water and disposal costs.
4. Enlist assistance from a total solutions provider of waste stream processing equipment to identify back-end investments that’ll benefit operations the most.
Although acquiring off-the-shelf processing equipment may be convenient, in the long run it may not provide the best value throughout its service life. Partnering with a total solutions provider optimizes return on investment and lowers total cost of ownership.
Companies weighing waste stream processing equipment options should seek a supplier that performs laboratory testing. Testing metal scrap processing and fluid recycling systems prior to purchase can confirm:
- How much fluid the system can recover
- How much it’ll lower new fluid purchases
- Moisture content before and after processing, and how much that’ll increase scrap value
Industrial water treatment solutions are as unique as each application’s water chemistry. Suppliers incorporating laboratory analysis into the specification process are more likely to deliver a solution optimized for the application, reduce equipment lead times, and deliver proof of capabilities prior to installation. A higher level of equipment specification also affords higher rates of equipment reliability.
5. Enhance waste stream processing by leveraging the latest metal scrap processing, fluid recycling, and water processing technologies available.
Metal scrap modification – Decreasing the volume of metal scrap is essential to effectively managing solid waste material. Increasingly, aerospace manufacturers are updating their processing system to reduce metal scrap at the front end of the process. Using a crusher or shredder unit at the CNC conveyor discharge adds value by:
- Reducing frequency of handling, transferring hoppers loaded with material
- Making the machine work zone safer
- Preventing equipment damage caused by material, belt jamming
- Decreasing the volume of the metal scrap so more material can be loaded in containers – companies get higher value for scrap because the recycler is hauling away a full 40,000 lb container, not a container full of voids
Processing the material in a crusher or shredder also transforms the metal scrap into shovel-grade material suitable for further processing in a wringer. A modern centrifuge or chip wringer uses up to 700g of centrifugal force to remove upward of 98% of the free liquids from the material. Dry chips, which are more valuable to a scrap dealer, can then be sent pneumatically or by gravity to lugger boxes, semi-trucks, or a storage silo.
Manufacturers are also leveraging briquetter systems – squeezing more value out of waste material and meeting environmental compliance. Briquetters incorporating dual compression technology use high compressive force from two opposing cylinders to form highly dense, dry pucks. The pucks have an average solid density of 85% to 90% and are up to 99% dry, making them more valuable to scrap dealers with up to 25% more value compared to loose metal scrap. Briquetters also reclaim valuable waste fluids from the material that can be recycled and reused.
Cutting fluid recycling – After cutting fluids have been reclaimed through wringing or compression, a cutting fluid recycling or filtration system enables manufacturers to reuse the fluids. This can substantially reduce new fluid purchases and the need to store hazardous fluids on-site until disposal. Haul-away costs also drop. Also, centralized systems that incorporate coolant management capabilities help kill bacteria and control viruses, yeast, and molds that can contribute to health problems.
Water treatment – Water used in manufacturing processes can be recycled and reused if treated properly. On-site water treatment and reuse within the operation establishes sustainable practices that’ll lower operating costs and protect the environment. Wastewater, which faces strict disposal regulations and is expensive to dispose of, can also be treated on-site.
Industrial water and wastewater treatment isn’t one-size-fits-all. Systems must be custom designed for the unique characteristics of a plant’s water and wastewater. However, manufacturers that position operations to meet Zero Liquid Discharge goals will realize significantly lower water and disposal costs.
Conclusion
Aerospace manufacturers can no longer afford to view investments in waste stream processing as expenses and continue to defer them in favor of production enhancements. As the industry moves toward achieving sustainability mandates, waste stream management will play a larger role in profitably meeting those objectives. Begin incorporating environmental compliance initiatives into a continuous improvement plan today to ensure consistent waste stream processing improvements that’ll benefit the operation long term.
About the author: Mike Hook is the sales & marketing director for PRAB and has more than 15 years of mechanical design and application experience. He can be reached at mike.hook@prab.com.
Get curated news on YOUR industry.
Enter your email to receive our newsletters.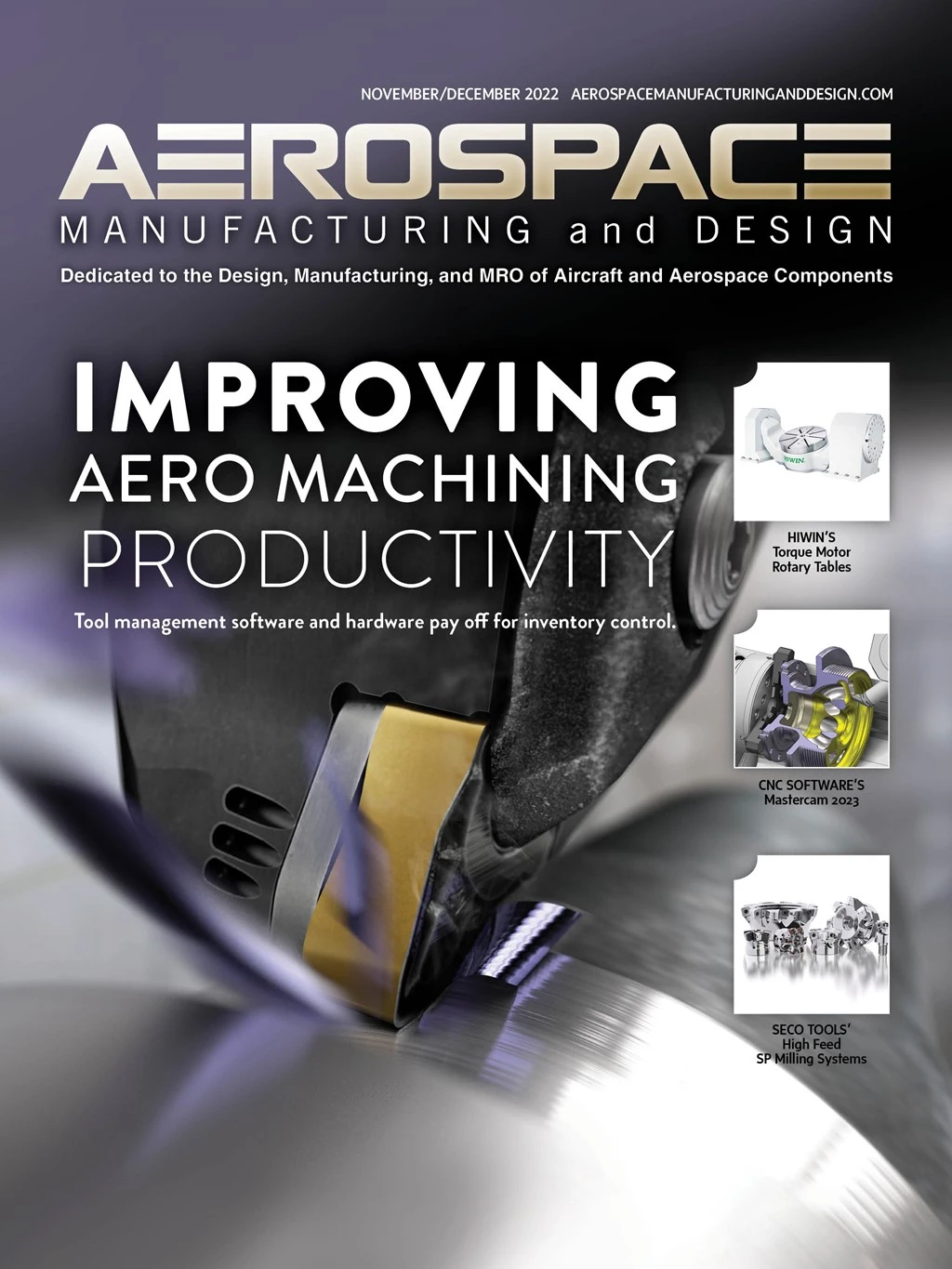
Explore the November December 2022 Issue
Check out more from this issue and find your next story to read.
Latest from Aerospace Manufacturing and Design
- GE Aerospace secures Air Force engine contract
- Thomson Industries' online sizing and selection tool
- #53 - Manufacturing Matters - 2024 Leaders in Manufacturing Roundtable
- Join us for insights on one of the hottest topics in manufacturing!
- You can still register for March’s Manufacturing Lunch + Learn!
- Ohio creates Youngstown Innovation Hub for Aerospace and Defense
- Tormach’s Chip Conveyor Kit for the 1500MX CNC Mill
- How to Reduce First Article Inspection Creation Time by 70% to 90% with DISCUS Software