
Producing carbon fiber reinforced plastics (CFRP) often involves large, expensive equipment. The molten polymer is pressed between reinforcing carbon or glass fibers under pressure and high temperatures to form a homogeneous plate. Using this time-and-energy intensive method, the plastic is only heated indirectly by the massive mold, which has to be moved, heated, and cooled again. The often high investment costs for presses and other large systems mean that small- and medium-size batches are not profitable. However, there is an alternative. Researchers at the Fraunhofer Institute for Chemical Technology ICT in Pfinztal, Germany, can heat the CFRP directly in a vacuum with infrared radiation.
Energy acts immediately where it is needed. For the mold wall, the researchers found a material that transmits infrared radiation in the desired wavelengths with almost no internal heat expansion. Usually, vacuum-based variotherm manufacturing processes take 30 minutes to several hours, depending on the component’s thickness. Using the ICT approach, it takes less than 60 seconds.
“Our method is faster, more economical, and more energy efficient than the current state of the art,” says Sebastian Baumgärtner, mechanical engineer at the institute.
Processing in a vacuum protects the material, the plastic does not oxidize, as it does in open procedures, and trapped air and possible exhaust gases are sucked out, making the process stable and easy to use.
“All forms of electromagnetic radiation are suitable for heating CFRP in our approach, including microwave radiation,” Baumgärtner explains.
The industry saves energy, costs, and materials and can manufacture faster. The method is suitable for both large and small series.
“It will particularly benefit small- and medium-sized companies that do not want to pay for expensive system technology,” Baumgärtner adds.
In a test plant, the researchers have produced 40cm x 40cm CFRP sheets.
“Our system fits on a normal shop floor,” Baumgärtner explains.
Unlike with large presses, no superstructures, substructures, or special foundations are needed, and the system produces distortion-free plates.
“This is a major challenge when manufacturing with CFRP. We heat and cool symmetrically, use a mold wall with minimal thermal expansion, and operate at relatively low process pressures in order to avoid squeeze flow,” Baumgärtner says.
The smooth surface of the mold wall also creates an almost reflective CFRP plate surface.
Fraunhofer Institute for Chemical Technology ICT
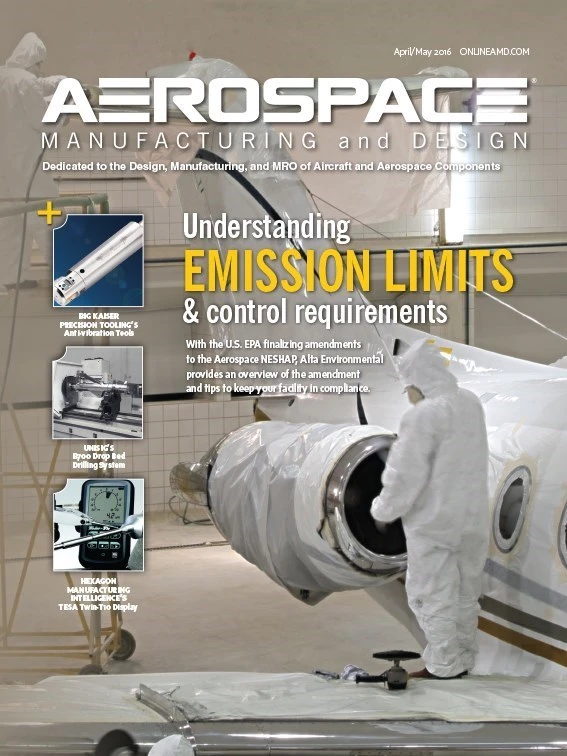
Explore the April May 2016 Issue
Check out more from this issue and find your next story to read.
Latest from Aerospace Manufacturing and Design
- 2024 Favorites: #10 Article – How 3D-printed aviation parts can accelerate return to air
- 2024 Favorites: #10 News – Boom Supersonic completes Overture Superfactory
- OMIC R&D hosts Supporting Women in Manufacturing Day 2024
- 4D Technology's AccuFiz SWIR interferometer
- Seventh Lockheed Martin-built GPS III satellite launches
- KYOCERA AVX's CR Series high-power chip resistor
- UT researchers receive Air Force grant for wind tunnel
- Monticont's linear voice coil servo motor