
Improving the productivity of a manufacturing process by speeding up the operation of an old machine can be very difficult, driving plant managers to purchase new equipment. It’s often possible, however, to replace the control system, maintaining the old mechanics, and get the performance of a new machine for much lower cost. Hydraulics distributor CMA/Flodyne/Hydradyne (CMAFH) of Hanover Park, Illinois, recently assisted in such an upgrade for a manufacturer of fastening components. The machine was a press used to imprint patterns on the surface of metal fasteners with a punch that fits into the bottom of a 4" bore hydraulic cylinder (Figure 1). As the punch comes down it reshapes the top of the fastener and its edges to provide a locking feature.
Motion controller selection

In the past, the manufacturer used a programmable logic controller (PLC) to operate a two-position, bang-bang valve to drive the cylinder, but company engineers found imprecise results that limited production to around 60-to-70 parts per minute. As a result, the company moved to a proportional valve and closed-loop controller that operated the valve based on cylinder position/acceleration. The controller would open the valve quickly and then back off the valve as the cylinder got closer to making contact with the fastener. This method enabled an increase in production to approximately 140 parts per minute. But to meet competitive pressures, company managers demanded the rate be increased, driving the need for a new electro-hydraulic motion controller.
Company engineers called CMAFH, with whom they had worked on automation solutions for more than 20 years, to recommend a new controller for the company’s old bang-bang machine.
Hooking up the controller
The Delta RMC75E motion controller (Figure 2), recommended by CMAFH engineering manager Norman Dziedzic, accurately controls position and force, to control acceleration with more precision than the closed-loop controller previously used. Dziedzic programmed the motion controller to move the cylinder to a predetermined position while monitoring the force being applied by the punch. When the force reaches a particular value, the controller is switched to force control mode to ensure that adequate force is ultimately applied to the fastener. The old closed-loop control system used position control only, with some input from a load cell within the tool to verify that a certain minimum force was applied to the part.
“The Delta controller operates similar to that, but is easier to control,” says Richard Mellor, engineer at the fastener company. Every motion step made by the other controller was initiated by the PLC, and there was lag time in passing position information. “The beauty of the Delta controller is that the motion program now resides in the controller,” Mellor adds.
Now, the PLC just does overall machine control, triggering the Delta RMC to press the part at the appropriate time. When the pressing operation is complete, the Delta controller knows, based on the position and force ranges inputted to the controller, whether the pressed part is a good part or a bad one, and notifies the PLC. The Delta RMC75E gets cylinder position feedback from a linear magnetostrictive displacement transducer (LMDT) via a synchronous serial interface (SSI) to the controller. To measure force, the system uses a fatigue-rated (rugged) force transducer (shown in Figure 1).
Programming, tuning

Dziedzic set up the motion program initially, and he fine-tuned the loop parameters working with a fastener company engineer. The two also developed the code to implement quality testing of the finished parts.
“I find the Delta very easy to program, but I have 30 years in as a controls engineer. If you’ve had anything to do with PLC or message display packages, it’s relatively intuitive to find your way around,” Mellor says
For tuning the motion, Dziedzic relied heavily on Delta Computer Systems’ Plot Manager software, which allows an engineer to view multiple key motion parameters versus time on a single graph (Figure 3). The plot shows three press cycles, where the red curve is the actual position of the press cylinder, the blue curve is the actual velocity of the cylinder, and the force being applied by the die to the work piece is shown by the black line. The cyan line is the target cylinder position. When the motion system is perfectly tuned, the actual cylinder position curve overlaps the target position, indicating that any positioning error caused by the mechanical aspects of the system – for example, the compressibility of the fluid or the friction of the moving parts – has been compensated for by the control algorithm. In Figure 3, the flat yellow line indicates the command force which must be applied to the part to make the press operation successful. The circle marked A highlights the point in time when the actual position (red line) begins to deviate from the target position (cyan line) as the tool comes into contact with the part. This is also when the force (black line) begins to climb. Then, at point B, the change in actual velocity (blue curve) shows force control taking over from position control. Area C in the plot shows when the actual force meets the target command force to signal a successful operation. Area D shows harmless motion transients that are caused by retracting the cylinder quickly to prepare for pressing the next part.
Using the Plot Manager, motion characteristics that occur too quickly to be visible to the naked eye can be analyzed and corrected if necessary, enabling the manufacturing process to be accelerated.
Results

One of the fastener company’s other key requirements on the controller upgrade project was to provide a means of accessing process data using the controller in order to do a pass/fail test on the finished parts.
“We track final position reached and maximum force achieved,” Dziedzic says. Previously, the company needed an external analog device to do this. Now, the Delta RMC75E eliminates this need by making process parameters available for the PLC to read directly over Ethernet. “The fact that the Delta controller can do this in addition to controlling the cylinder provides a huge benefit to them.”
“We have been very happy with the performance increase we have gotten with the Delta motion controller,” Mellor adds. “Even if we hadn’t gotten the performance, Delta’s ease of use in system setup and tuning would have made the difference.”
With the Delta RMC75E controlling the operation of the cylinder, the machine can now process up to 180 fasteners per minute.
“We can move faster because we have more control over the proportional valve, yielding tighter control loops and better control of the gain in the system,” Mellor says.
Another advantage of using the Delta RMC is operation repeatability; the controller is able to control the force exerted in each cycle to a tolerance of ±40 lb out of 10,000 lb applied.
Delta Computer Systems Inc.
CMA/Flodyne/Hydradyne
About the author: Richard Meyerhoefer is regional application specialist at Delta Computer Systems Inc. He can be reached at 360.254.8688 or rmeyerhoefer@deltamotion.com.
WANT MORE?
Enter your email to receive our newsletters.
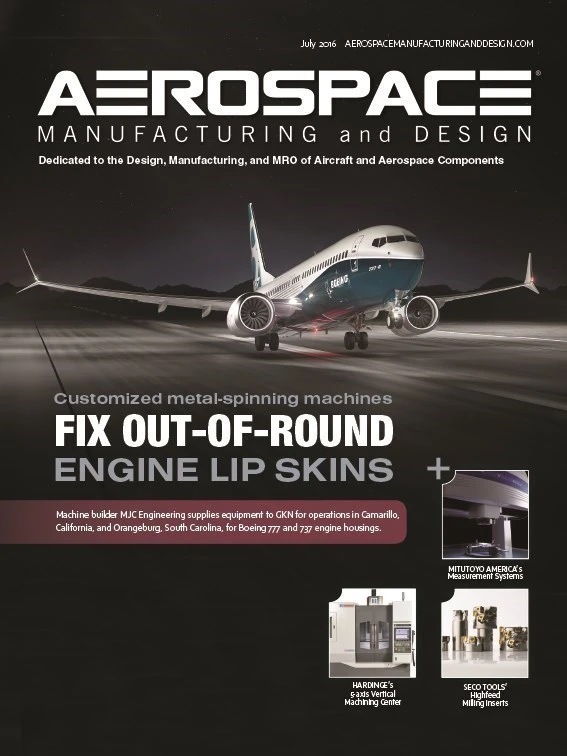
Explore the July 2016 Issue
Check out more from this issue and find your next story to read.
Latest from Aerospace Manufacturing and Design
- GE Aerospace awarded subcontract for FLRAA next phase
- KYOCERA Precision Tools publishes 2025-2026 Indexable Cutting Tools Catalog
- BOC Aviation orders 120 Airbus, Boeing jetliners
- Mazak’s INTEGREX j-Series NEO
- Embraer tests wing for new technologies demonstrator
- Mitutoyo America’s SJ-220 portable surface roughness tester
- #55 - Manufacturing Matters - A Primer on Defense Contract Manufacturing
- Registration is open for April’s Manufacturing Lunch + Learn!