
Whether aerospace manufacturers machine components for commercial, defense, or space projects, they face several similar challenges. Reducing costs, getting the most from their tools, eliminating tool runout and pullout, and shortening setup and cycle times are all priorities when processing tight-tolerance parts from unique and challenging materials.
New materials require an innovative approach
What worked in the past doesn’t work today. Tighter tolerance requirements and difficult materials introduce new and daunting variables into the machining operations, forcing manufacturers to come up with new ways to optimize their processes. This means in aerospace production, all things matter – from the manufacturer’s specifications to qualification plans and machine accuracy to repeatability.
The majority of materials, such as Rene 41, 718 stainless steel, 625 Inconel, titanium, carbon fiber, sandwiched materials, and others used in the aerospace industry sector are extremely hard on cutting tools, so shops constantly strive for the longest possible tool life. When it comes to toolholding, the key to increased cutter life is a holder providing ultra-low total indicated runout (TIR). The goal is to get as close to zero TIR as possible because with every 0.0001" of TIR reduction, tool life can increase upwards of 50%.
Optimized processes, finer surface finishes, reduced costs
In addition to extending tool life in challenging materials, toolholders with ultra-low TIR provide the necessary precision aerospace manufacturers need to meet stringent industry part and assembly tolerances. With a TIR ≤3μm at 3xD, the REGO-FIX powRgrip toolholding system provides tighter toolholding for finer surface finishes while providing easier setups even in difficult applications such as composites, various material stack-ups, and splicing. Change outs are fast, too.
Given its low TIR and significant vibration damping qualities, powRgrip is also a perfect fit for today’s aerospace applications involving tool overhangs from 6" to 12". Such precision also optimizes the machining of complex, critical aerospace components, allowing shops to benefit from the use of high speed cutting (HSC) or high performance cutting (HPC) strategies. The lower the TIR, the less tool vibration, and when vibration is low, the longer cutting tools last, reducing overall tooling costs.
Simple, safe, and secure
The powRgrip system uses a table-top unit with press-fit technology to apply up to nine tons of clamping pressure for an industry-leading 1,100Nm clamping torque rating in 10 seconds or less. Using the system is as easy as inserting the tool into the collet, placing the collet into the toolholder, putting the assembly into the table-top unit, and pressing the Press In button. Additionally, there are no tool setting heat, chemicals, or fumes associated with the powRgrip system for total operator safety. Tools can be handled as soon as they’re loaded.
Across the board in a variety of challenging materials and precision processes, the powRgrip toolholding system improves production results and profitability for aerospace manufacturers in every sector of the industry.
REGO-FIX also offers a free test and trial of a powRgrip system. A standard trial runs three to four weeks and doesn’t obligate shops to any purchase.

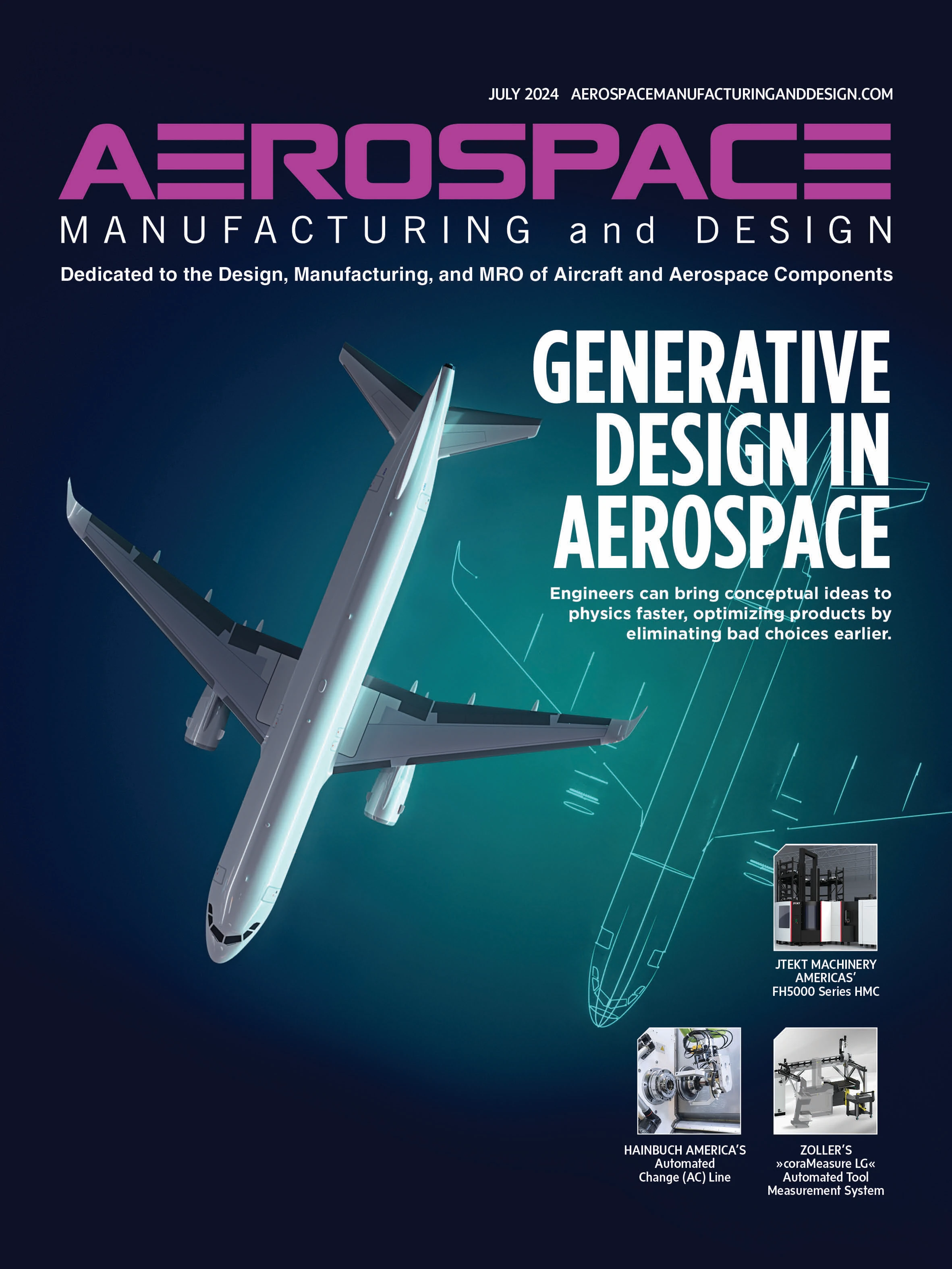
Explore the July 2024 Issue
Check out more from this issue and find your next story to read.
Latest from Aerospace Manufacturing and Design
- Titanium drop bottom furnace installation underway
- Solid carbide taps for demanding materials
- The Partner Companies acquires Precision Eforming
- Hall Effect angle sensors
- July is for learning – so drop in for this month’s second Manufacturing Lunch + Learn
- Essential strategies to protect your data
- NASA selects instruments for Artemis lunar terrain vehicle
- Twin-cutter boring head