
At IMTS 2024, the Chiron Group will show its comprehensive product lineup, including the Micro5 and Mill 2000.
The Mill 2000, a vertical machining center designed for 5-axis machining, offers precision, productivity, and versatility. The swivel spindle reaches speeds up to 30,000rpm with 180Nm of torque. Within the working space dimension of X/Y/Z = 78.74" x 38.38" x 28.15" multiple clampings or large workparts are machined with feed rates up to 246fpm and tool change time of 1.5s.
The Micro5 has a footprint of 10.76ft² and an energy consumption of 0.5kW. Automated with the Feed5 automation system, the modular design of Micro5 can grow from prototyping to large-scale production, with high autonomy.
Chiron GroupIMTS 2024 booth #338190
Process-reliable clamping and automation

The Vise Power Clamp (VPC) tooling system was developed to boost the economic efficiency of workpiece production. With the loading station, it guarantees a reliable and trouble-free automation process. The key components consist of the two VPC chuck sizes (52mm and 96mm) and the matching VPC chucking spigots. All workpiece holders prepared with the common 52mm or 96mm pitches can be clamped in the matching VPC chucks. Preparation is simple: screw the VPC chucking spigots into the workpiece holder, the fixture or the workpiece itself, and tighten. The VPC chuck also includes an integrated Z-support, status monitoring, and a circumferential seal.
The VPC chucks can be attached to the machine table directly or through a base plate. Workpiece holders and workpieces are clamped in the chuck with 15kN of force. Workpieces can be exchanged in seconds with a repeatability of <0.003mm. The VPC chucking spigots are made of high-quality hardened steel and have a long life cycle. The ground functional surfaces ensure optimal run-in behavior into the VPC chuck. With the help of adapter pallets, the VPC tooling system can be combined with other EROWA UPC or MTS tooling systems.
EROWA Technology Inc.IMTS 2024 booth #339080
Automation and software solutions

GF Machining Solutions will feature its latest advancements in tooling, automation, and software from System 3R at IMTS 2024. For 24/7 production, System 3R Automation offers scalable automation solutions to shorten lead times and maximize return on investment (ROI). System 3R’s software solutions give users a quick, precise overview of their entire process chain. Various software solutions ensure information about workpieces, magazine positions, offset values, and NC programs is always readily available.
The company’s software portfolio packages include WorkShopManager, CellManager, EasyCellManager, CellManager Light, and BatchBuilder. For integration of all shop operations, WorkShopManager provides an overview of the process chain and management of the entire automation system. CellManager works with up to 12 machines in a cell and supports machines such as milling, sinker and wire EDM, laser, coordinate measuring machines (CMM), and cleaning. EasyCell Manager works with up to four machines, supporting milling and laser texturing. EasyCellManager Light is for robotless systems encompassing as many as 12 machines in a cell with machines such as milling, wire and sinker EDM, laser, and CMM. BatchBuilder lets users create job batches to run in their robot cells with various types of milling, sinker and wire EDM, laser, and CMM machines. Key benefits of the software include full process optimization, ease of use, and added scheduling flexibility with process chain monitoring.
GF Machining SolutionsIMTS booth #339458
Automated workholding changeover

The Automated Change (AC) Line streamlines transitions between workholding devices with speed and accuracy, reducing downtime.
Hainbuch AmericaIMTS booth #431636
3D printing technology

MC Machinery will display its latest EDM and precision milling technology, including wire and sinker EDMs, machining centers, and automation at IMTS 2024. Also featured will be the new Mitsubishi AZ600 wire-laser metal 3D printer, which melts welding wire with a laser beam to create high-quality 3D structures. Featured machines at IMTS 2024 will include:
Sinker EDMs – The SV12P and SG12 sinker EDMs optimize performance, improve productivity, reduce electrical consumption, and accurately estimate machining time. The SVP Series incorporates a sensor monitoring the total electrode contact area within the workpiece, allowing the system to change power conditions based on real-time feedback, resulting in up to 40% less electrode wear and up to a 30% reduction in machining time. At IMTS, the SV12P will be outfitted with EROWA Robot Compact 80 milling and sinker automation.
Also featured will be the OPS Ingersoll Gantry EAGLE 800 sinker EDM, geared toward large-part and molding applications. Along with low electrode wear and fast cycle times, the Gantry Eagle series has on-board components designed to reduce wear and tear, also decreasing maintenance and downtime. It also has a large, easy-to-access working area that requires less floor space than other sinker EDM models.
Wire EDMs – The MV1200-R wire EDM features the latest machine construction, submerged threading, fiber optic machine communication, and power supply technology. This machine will be shown with the Mitsubishi Electric 6-axis robot automation system. The MV2400-R wire EDM features a larger tank capacity and low operational costs. The MV4800-S wire EDM is suited for large part applications up to 20" high (standard), and 32" high (optional) and can perform submerged cutting up to 20" deep. With an annealing length of more than 27", the system can thread through the workpiece at the start point and through the gap. The MX600 Oil Advance Plus wire EDM combines machine accuracy and surface finish, with wire capability down to 0.0008" (0.02mm) diameter. The MX600 features a Nano-Pulse power supply and DMX-S Super Digital Control sensor, specifically shaping each spark producing surface finishes down to 1.6µ" Ra.
Precision milling – The Roku HC658II full-bridge style design combines a 32,000rpm spindle with graphite protection. The ANDROID II linear drive milling machine is designed for hard steel and carbide machining with accuracies within ±1µm, with a 60,000rpm spindle. The Ingersoll Eagle V550 graphite machining center features high-speed, high-precision 5-axis machining for small graphite electrodes and hard machining of mold/die components. Complete with the Heidenhain 640 controller, the V550 makes quick work of challenging electrode manufacturing.
Wire-metal laser 3D printer – Using commercially available welding wire as feedstock, the AZ600 has rapid prototyping, mold and die, one-offs, short runs, mass manufacturing, maintenance, repair, and tooling applications. With the same wire-feeding technology used in Mitsubishi’s wire EDMs, a simple command on the machine’s CNC control feeds the exact amount of wire to the target location.
MC MachineryIMTS booth #338129
Integrated manufacturing system

ANCA CNC Machines is celebrating its 50th anniversary in business, the recent opening of its newest Tech Center in Temecula, California, and the release of new products, including the MicroX ULTRA, the ANCA Integrated Manufacturing System (AIMS), and AIMS Connect, at IMTS.
ANCA Integrated Manufacturing System (AIMS), the smart manufacturing solution for cutting tool production, enables manufacturers to connect, automate, and create. A modular system of hardware and software components for automated, closed loop manufacturing, AIMS server controls production processes and AutoComp, the intelligent compensation module, maintains part quality automatically, while the new AIMS Connect function covers job management.

ANCA’s GCX machine and gear tool technology is a turnkey solution for producing skiving cutters. This offering includes features for designing gear cutting tools, manufacturing, integrated tool measurement, and skiving machine setup parameters. This configuration enables short setup times, simulation, and monitoring, plus quality enhancing features such as the ANCA Motor Temperature Control (MTC) and integrated balancing (iBalance) for longtime grinding profile accuracy within ±0.0015mm.
The MicroX ULTRA, a 6-axis micro tool grinder with nanometer control, optimizes mechanical layout and axis travel, integrates tool measurement and progressive automation, and enables volume production of tools down to 0.03mm.
The new EPX-SF, ANCA’s edge preparation and surface finishing solution, addresses productivity targets, delivers superior IP cutting tool performance, and succeeds in precision-critical industries. The machine offers 11-axis automation and smart recipe fine-tuning to optimize media utilization while providing precise edge control. The machine reduces edge roughness to <100nm and refines edge radii to microns with controllable K-factor. The EPX-SF’s cyclic mode with pulse rotation defends against surface burrs and edge imperfections. With adjustable positive and negative angles, the EPX-SF spindle traverses the cutting path, optimizing potential chip flow and reducing the surface roughness of the cutting workpiece. Within ANCA’s automation ecosystem, the EPX-SF integrates into production lines, operating autonomously with robotic assistance for round-the-clock tool loading/unloading.
ANCA CNC MachinesIMTS 2024 booth #237406

Expanded offerings at IMTS

Sandvik Coromant will showcase an expanded offering of technology and services at the upcoming IMTS 2024. Booth visitors can expect an immersive experience bringing together products, expertise, and digital machining technology for a wide range of industries. In addition to its team of Yellow Coat experts, senior leadership from Sandvik Coromant will be in attendance, including Michael Eneberg, global VP of Sales and Marketing, and Magnus Ekbäck, VP of Strategy and Business Development, providing attendees with direct access to the company’s strategic vision and decision makers.
Sandvik CoromantIMTS booth #338348
Precision, repeatability, and versatility

Mitsui Seiki is bringing three machines to IMTS 2024. These machines, used in tandem or on their own, enable users to produce highly accurate parts again and again.
The Vertex 55X III can perform multiple functions in one machine and can be adapted to integrate seamlessly into any machining cell. To demonstrate this, the 55X at IMTS will showcase a field retrofittable pallet system with shared tool capacity, and a total of 12 pallets and 140 tools.
The HU100-TS 5-axis Tilt Spindle Machining Center has powerful linear and rotary axes configured with a high torque spindle. The updated line provides rigidity and accuracy to mill materials such as titanium, Inconel, stainless steel, and challenging alloys common in ultra precision, high-value applications.
The J350G Jig Grinder offers flexibility, accuracy, reliability, and operator-friendly operation. With a U-axis range of -3mm to +50mm relative to the spindle center, this solution provides the versatility to grind small- and large-diameter holes, as well as free-form complex features, using a single wheel in a continuous, automatic mode.
Mitsui SeikiIMTS booth #338700
CNC tooling storage solution

Tool Caddy is a compact storage solution for assembled CNC tooling. The narrow,. stainless-steel cart has up to 82 locking, horizontal pockets for all major spindle interfaces. The horizontal arrangement of the tool pockets improves machinist safety. Traditional tool racks and carts keep tools in a vertical position with the cutter tip pointing up, creating a risk of injury for operators reaching over sharp edges to access tools in the middle or back of the cart.
The Tool Caddy design makes it easy and convenient for the operator to access each toolholder without risk of cuts while using only 4ft² of floor space. Each tool pocket is angled to safely support the tool, while allowing coolant to run off the tool tip and collect in the integrated drip pan. This feature also improves safety by keeping fluid spills off the shop floor.
Tool Caddy is convenient for tool storage next to the machine, by the pre-setter, or for organizing special tool sets. It is available for CAT 40, CAT 50, HSK 63, HSK 100, BT, and Capto tool holders.
Kaiser ManufacturingIMTS 2024 booth #432141
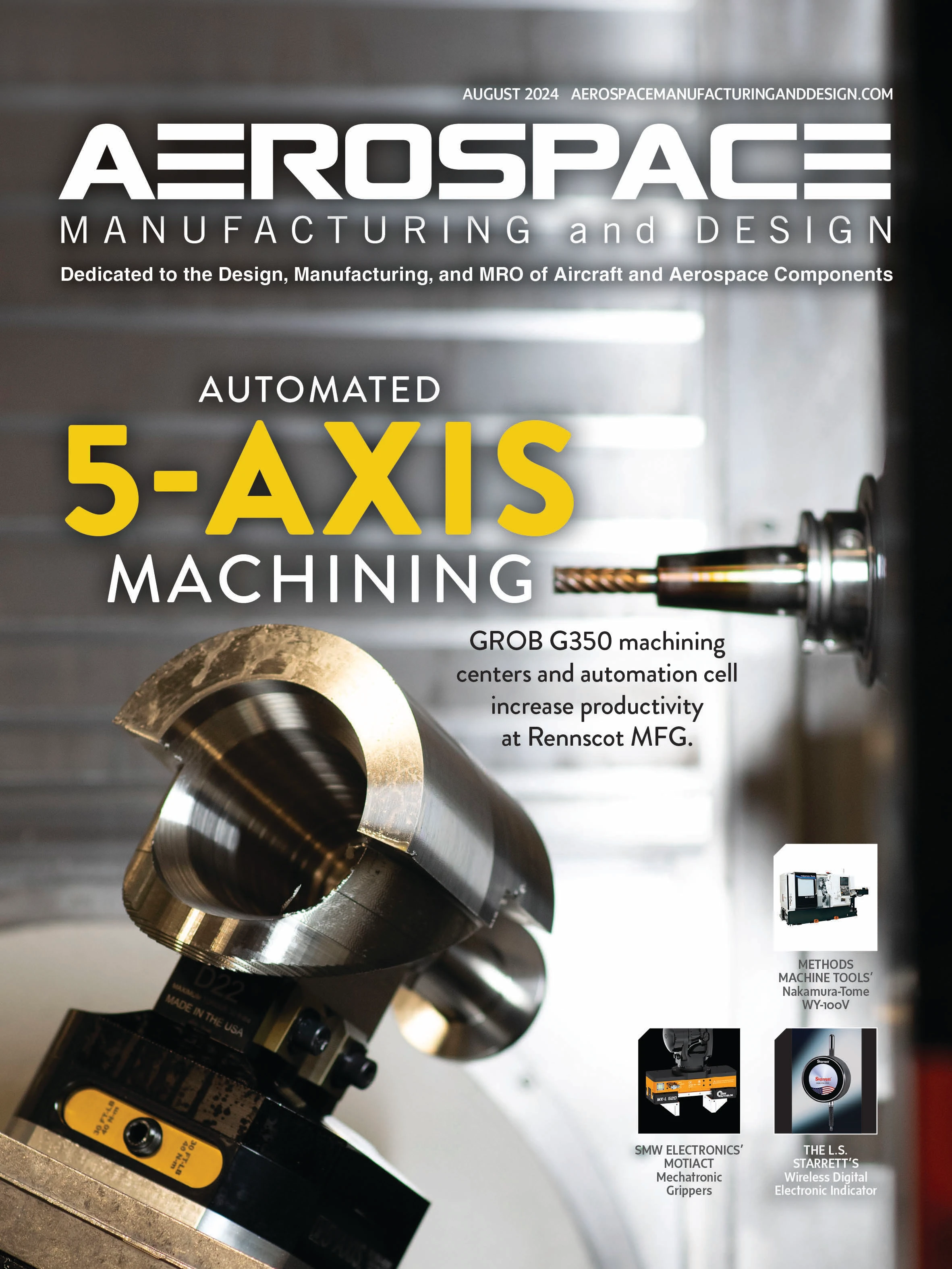
Explore the August 2024 Issue
Check out more from this issue and find your next story to read.
Latest from Aerospace Manufacturing and Design
- America Makes announces QTIME project call
- Innovation meets precision for 40% faster machining
- Upcoming webinar: Pro tips from a supply chain strategist
- Heart Aerospace relocates to Los Angeles
- Fixtureworks introduces Stablelock Clamps
- Piasecki acquires Kaman's KARGO UAV program
- PI Americas’ long-travel XY piezo nanopositioners-scanners
- AAMI project call submission deadline extended to May 12