

Stainless steels are used across industries manufacturing precision parts, with grinding needed to produce profiles with improved finishes, closer tolerances, and sharper edges.
In CNC tool grinding, I estimate approximately 10% of total machine utilization in the United States is dedicated to grinding surgical cutting instruments made of stainless steel, including bone drills, cranial cutters, bone reamers, rasps, burs, shavers, cannulated drills, and more. While your shop may not be involved in medical device grinding, the materials’ properties present the same challenges for aerospace use.
A common stainless steel is 440, a martensitic grade that can achieve a hardness up to 60HRC, depending on the specific hardening process applied.
Heat-treated 17-4 stainless steel is another material commonly used, offering a hardness up to approximately 45HRC.
The 316 series is an austenitic stainless steel widely used in the medical device industry, though it’s less commonly used for cutting instruments. Its relatively high chromium and nickel content make grinding more challenging. The hardness of 316 stainless steel typically falls in the 30s on the HRC scale.
Anyone in the grinding industry will agree harder materials are generally easier to grind. Softer materials tend to cause premature wheel loading, leading to smearing, whereas harder materials allow the abrasive grains to efficiently chip away at the surface.
The fundamental rule for grinding stainless steel – and likewise for high-speed steel (HSS) – is to use cubic boron nitride (CBN) grinding wheels. CBN is a synthetic material, similar to diamond, and ranks as the second hardest material after diamond. However, diamond is unsuitable for grinding ferrous metals due to its tendency to degrade through chemical reactions at high temperatures.
The easiest wheel bonds to work with are resin or hybrid bonds. They’re durable, provide excellent corner retention, and support reasonable feed rates.
For flute grinding, vitrified bonds are a suitable choice, provided there’s an onboard dressing process capable of autonomously reconditioning the wheel. Selecting a manufacturer with proven expertise in this area is essential. In some cases, feed rates can be increased 50% to 100% with vitrified wheels.
Excess heat generated during grinding affects all hardened steels. To mitigate this, it’s important to increase coolant oil volume compared to what’s used for grinding carbide. This can easily be achieved by installing a booster pump in the inbound coolant delivery line to enhance pressure, flow, and cooling efficiency.
MyGrinding Inc.
https://www.mygrinding.com
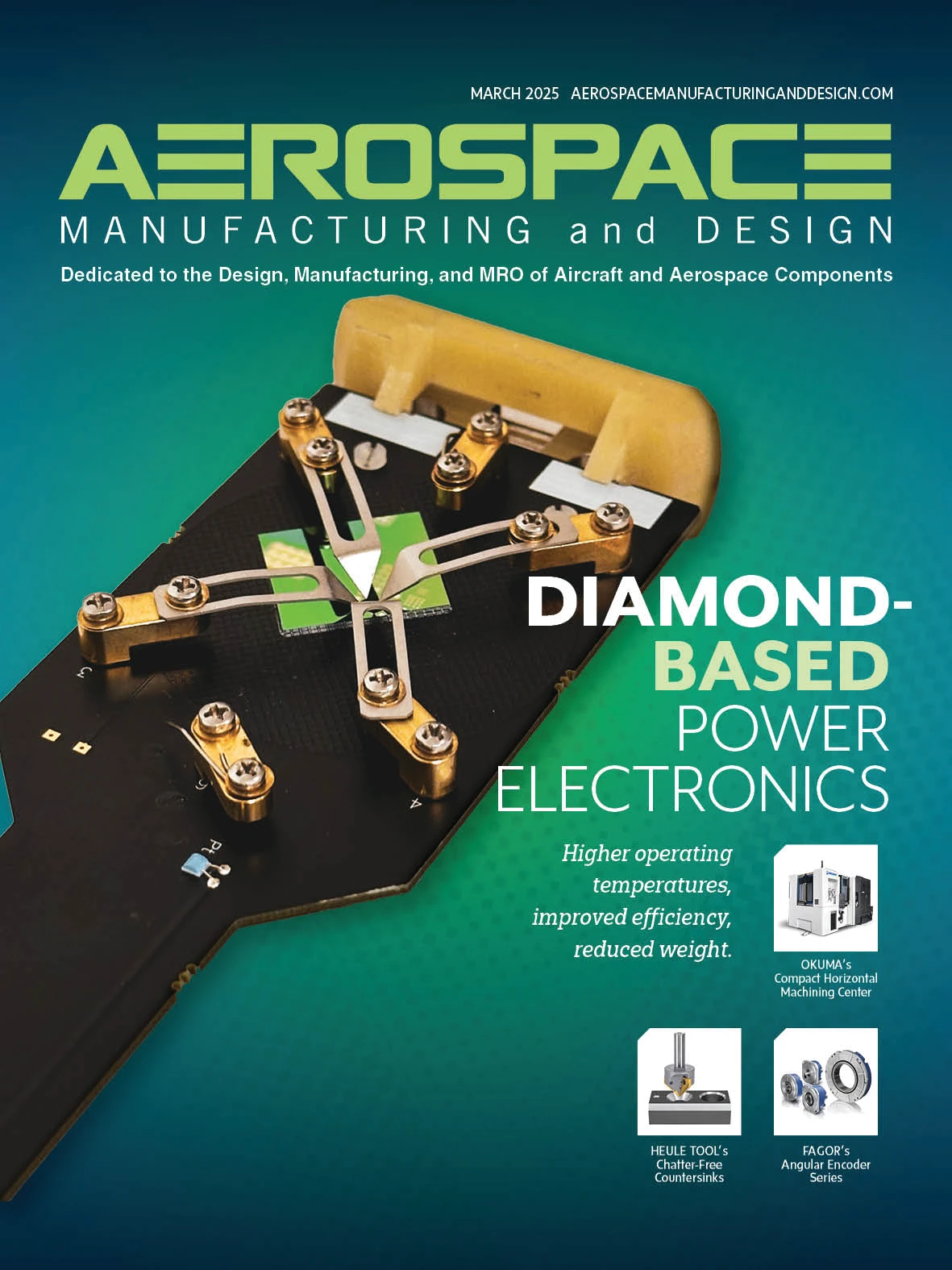
Explore the March 2025 Issue
Check out more from this issue and find your next story to read.
Latest from Aerospace Manufacturing and Design
- NASA offers free high school engineering program this summer
- Pemamak's PEMA Vision 3D software
- Aerospace Industry Outlook - Spring 2025, presented by Richard Aboulafia
- Panama’s National Air and Naval Service selects Embraer Super Tucano
- Model 5770 Linear Abraser
- #42 Lunch + Learn Podcast - Quell Corp
- RECARO Aircraft Seating showcases advanced comfort solutions at AIX 2025
- Mitutoyo America’s MiSTAR 575 Shop Floor CNC CMM