Resolving challenging bonding or adhesion issues with the ideal plasma treatment is an exact science, often the domain of chemists and physicists. With multiple options and chemistries, coming up with the right recipe often requires a precise understanding of the surface free energy.
Many devices that measure surface energy offer limited information, and they fail to measure the polar and dispersive components of surfaces that otherwise have the same surface energy.
This is critically important, says Dr. Michael Barden, head of research & development at PVA TePla America, because some adhesives will bond with polar surfaces while others perform better with dispersive surfaces. For example, organic adhesives often bond better to dispersive surfaces, whereas two-component epoxies, carbonates, or ureas bond better with a polar surface.
“When these factors can be more precisely measured, plasma experts are able to dial-in the best treatment solutions, with more consistent results,” Barden says.

Dyne tests
Plasma treatments often create high surface energy for increased wettability of surfaces to assist chemical adhesive spreading. Dyne tests can measure surface energy to derive a value in
Although
“In about 70% of the projects we work on, dyne testing roughly correlates to adhesion,” Barden says. “However, it can only determine if bonding is working within a specific range.”
Barden notes customers regularly ask for dyne tests to determine if the surface energy is, for example, 55dyn/cm or better. However, deriving a quantitative number can be important if a plasma treatment works best at precisely 60dyn/cm.
“By more completely measuring the surface free energy, we can measure the quantitative change that occurs before and after plasma treatment,” Barden explains. “This allows the customer to correlate those measurements with their bonding experiments.”
To do this, designers and manufacturers of plasma systems often turn to advanced drop-shape analyzers such as those available from Krüss.
Drop-shape analyzers
Because surface energy of a solid cannot be measured directly, surface energy values must be calculated from a set of liquid/solid contact angles developed by bringing various liquids in contact with the solid.
Drop-shape analyzers visually measure these contact angles; a droplet is deposited by a syringe positioned above the sample surface and a high-resolution camera captures the image from the profile (side) view, which is measured using image analysis software.
Most of these systems are software-controlled to enable direct determination of the precise contact angle and surface free energy, measured in millinewton per meter (mN/m), a value identical to dyne per centimeter (
Krüss equipment can simulate surface treatment process conditions using precision, temperature-control methods
Most importantly, according to Barden, advanced drop-shape analyzers can evaluate the polar and dispersive components of surface free energy.
Water is often used for contact angle measurement but is not sufficient for determining whether the surface is polar or dispersive. Instead, a variety of known liquids must be used, followed by data fed into complex mathematical equations, analyzed, and then graphed.
This type of approach can also determine if a surface is oleophobic (repels oils). In applications such as fluorinated coatings that need to repel water and other organic materials, drop-shape analyzers play a key role.
“Engineers often want to know if the polymers they want to bond are oleophobic as well as hydrophobic, which the Krüss system can tell them,” Barden explains.
Using this quantitative and qualitative information, plasma experts can then alter surfaces by altering the plasma treatment applied.
Physical plasma such as helium, for example, would create a dispersive surface that allows liquid to spread broadly. Oxygen plasma – along with a hydroxyl or carboxyl coating – could be used to create a polar surface that would alter the spreading mechanism.

Leveraging surface analysis
PVA TePla offers this technology as a service, supported by an in-house team of materials scientists and engineers, allowing users to dial-in precise equations that provide options for successful surface treatments.
In addition to designing and manufacturing plasma systems, the company is also a contract manufacturer with the equipment to process materials and conduct a full range of experiments. Customers can brainstorm with their technical team and run collaborative experiments. According to Barden, these technical customer/supplier meetings often produce the best experimental matrices and ideas.
Krüss USA PVA TePla America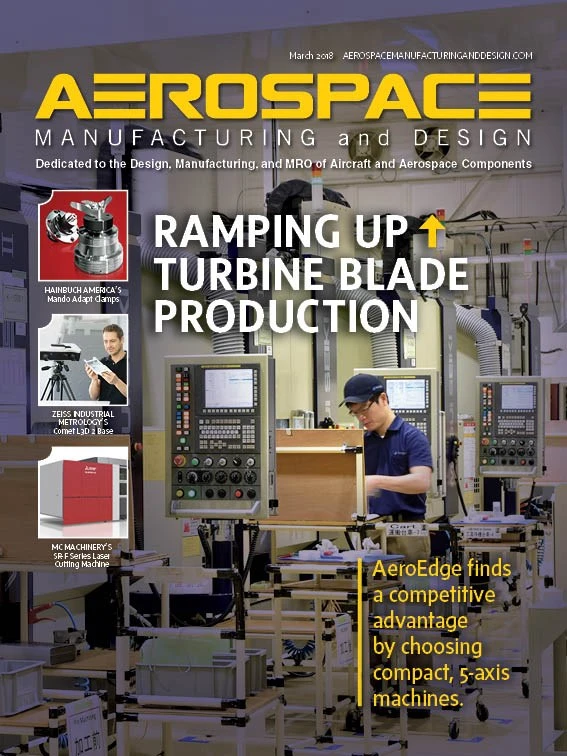
Explore the March 2018 Issue
Check out more from this issue and find your next story to read.
Latest from Aerospace Manufacturing and Design
- Revitalizing the Defense Maritime Industrial Base with Blue Forge Alliance
- Safran Defense & Space opens US defense HQ
- Two miniature absolute encoders join US Digital’s lineup
- Lockheed Martin completes Orion for Artemis II
- Cylinder CMMs for complex symmetrical workpieces
- University of Oklahoma research fuels UAS development
- Motorized vision measuring system
- Everyone's talking tariffs