The efficiency of a power-conversion subsystem is important to overall system performance. For every watt of power dissipated, aircraft range is reduced or energy storage is increased. The topology chosen and its efficiency performance affects the power converter’s size, weight, reliability, and cost. All of these factors have important and serious implications:
- Ease of installation
- Thermal loading of the surrounding area
- Life cycle cost where reliability, weight, and initial cost are factors
In addition to the benefits of high efficiency, other electrical performance factors matter. When converting from AC platform power, the approach must provide active power factor correction (PFC) to minimize current harmonic distortion and regulated DC output characteristics. When combined with a smaller, lower weight package at a competitive initial cost, a compelling proposition is at hand. With a new single switch approach to implementing power factor corrected, AC-to-DC regulated power conversion, these goals are achieved without compromise in a qualified package for aerospace and military applications.

Legacy topologies degrade overall efficiency
The traditional path from three-phase 115VAC to regulated DC power requires multistep topologies. There are two main legacy methods:
- Transformer rectifier unit with output boost converter (Regulated TRU or RTRU)
- Rectifier with Active PFC followed by a switching regulator (APFC-SMPS)

The first type – RTRU – is in wide use on airframes where a somewhat regulated output is required. It uses the topology of an unregulated TRU, followed by a boost converter. The latter maintains the output voltage under high load demands in which the TRU’s output will sag.
It’s important to note that the TRU and RTRU don’t employ power factor correction circuitry and will exhibit high levels of current harmonic distortion at loads below 50%. While not complex, this converter relies on a large, heavy transformer and many diodes to provide the intended function.
TRUs commonly convert the 120VAC power from the engine or auxiliary power unit (APU) generator on board, or a ground power unit (GPU) into 28VDC to power electrical components. In a TRU, the transformer component isolates the AC input from the output and via rectifier diodes creates the DC output, followed by L-C filtering to remove most of the AC ripple from the DC. The second step is the boost converter which lessens voltage sag under load as there’s no regulation in the transformer/diode section.
The three-phase TRU issues go beyond efficiency and ripple. Since two of the three phases are conducting current through the bridge at any one time, the current discontinuity causes undesirable harmonic distortion and reduces power factor. The input power source sees a reactive load due to post-rectifier filter capacitance used to smooth rectified voltage ripple, inducing a phase shift of the current with respect to voltage, pushing the power factor down from the desired value of unity. The use of two 6-diode rectifier circuits brings down harmonic distortion to a usable level of 12%.
The second type – the APFC-SMPS – uses switch mode power supply (SMPS) techniques to achieve power conversion resulting in more highly effective active PFC in one stage and output isolation (if required), step up or down, and regulation (Figure 1) in its second stage. There are traditional designs where the PFC function and output regulation function are accomplished in two separate switching or step circuits.
The first step rectifies the AC voltage and applies active power factor correction (APFC) resulting in total harmonic distortion (THD) holding to a low level, typically under 5%, with individual harmonics <3%. The side effect of APFC circuits is they also behave as boost converters. This boosted voltage is fed to an isolated or non-isolated switching regulator, providing a line and load regulated output at the lower desired DC voltage. The result is a higher performing power conversion process, albeit with the size, weight, and complexity penalty of two separate switching circuits.
Consider a regulated AC-to-DC path with two stages, with each stage at a respectable 95% efficiency at near load or full load. Overall efficiency is therefore slightly more than 90%. It’s very difficult to achieve desired efficiencies in the 92%+ range, including losses in the electromagnetic interference (EMI) filters when you have multiple switching converters in series. The difference in power dissipation going from 90% to 92% for a 1kW converter at full load is 24W, a decrease of 22%.

New approach, multiple improvements
When converting AC input power to an isolated, fully regulated DC output while also adding passive or active PFC, each step adds to complexity, component count, volume, and weight while decreasing efficiency. With the demands on power subsystems, there’s a need to improve power conversion.
Marotta Controls developed a single-step AC-to-DC conversion, based on a circuit solution that simultaneously provides output-voltage regulation, electrical isolation, and APFC (Figure 2).
The 1-STEP topology employs a switch mode power converter where each of the three-phase pairs feeds a full-wave rectifier and flyback converter that operate in parallel in closed-loop voltage mode (Figure 3).
The three converters use a single, shared control loop to regulate the output voltage that sends a single pulse-width modulated (PWM) signal which controls the current flow through all three converters. The converter outputs are connected in parallel which share the load evenly due to the common control. Power flow is distributed evenly among the input phases with each always providing current.
The 1-STEP design switches the rectifier current at a frequency of 50kHz, compared to 2x the line frequency for TRUs, essentially eliminating the low frequency current distortion. The proportionality of current to voltage causes the converter to appear resistive to the input power source while the higher switching speed also eliminates the need for a ripple smoothing filter capacitor that follows traditional rectifiers. These two factors result in power factor correction of between 0.95 and unity depending on the specific 1-STEP model and load, with current harmonic distortion performance <2%.

1-STEP AC-to-DC performance
Many AC-to-DC power-conversion models are available from Marotta Controls using the 1-STEP architecture, each with overall efficiency better than 91%, ranging from as low as 30% evenly to 100% of rated load (Figure 4), and with power factor between 0.95 and unity, depending on model and load.

Of course, a good AC-to-DC converter is defined by more than its high efficiency and near-unity power factor. All 1-STEP units include overload capability; over-current, over-voltage, and over-temperature protection; low inrush current, and stiff response to dynamic loads. Overload capability in the 28VDC units is designed for traditionally configured applications. They all meet the relevant standards for advanced military and commercial platforms covering environmental tests (temperature, vibration and shock, humidity, salt fog), EMI/EMC characteristics, and power quality and utilization.
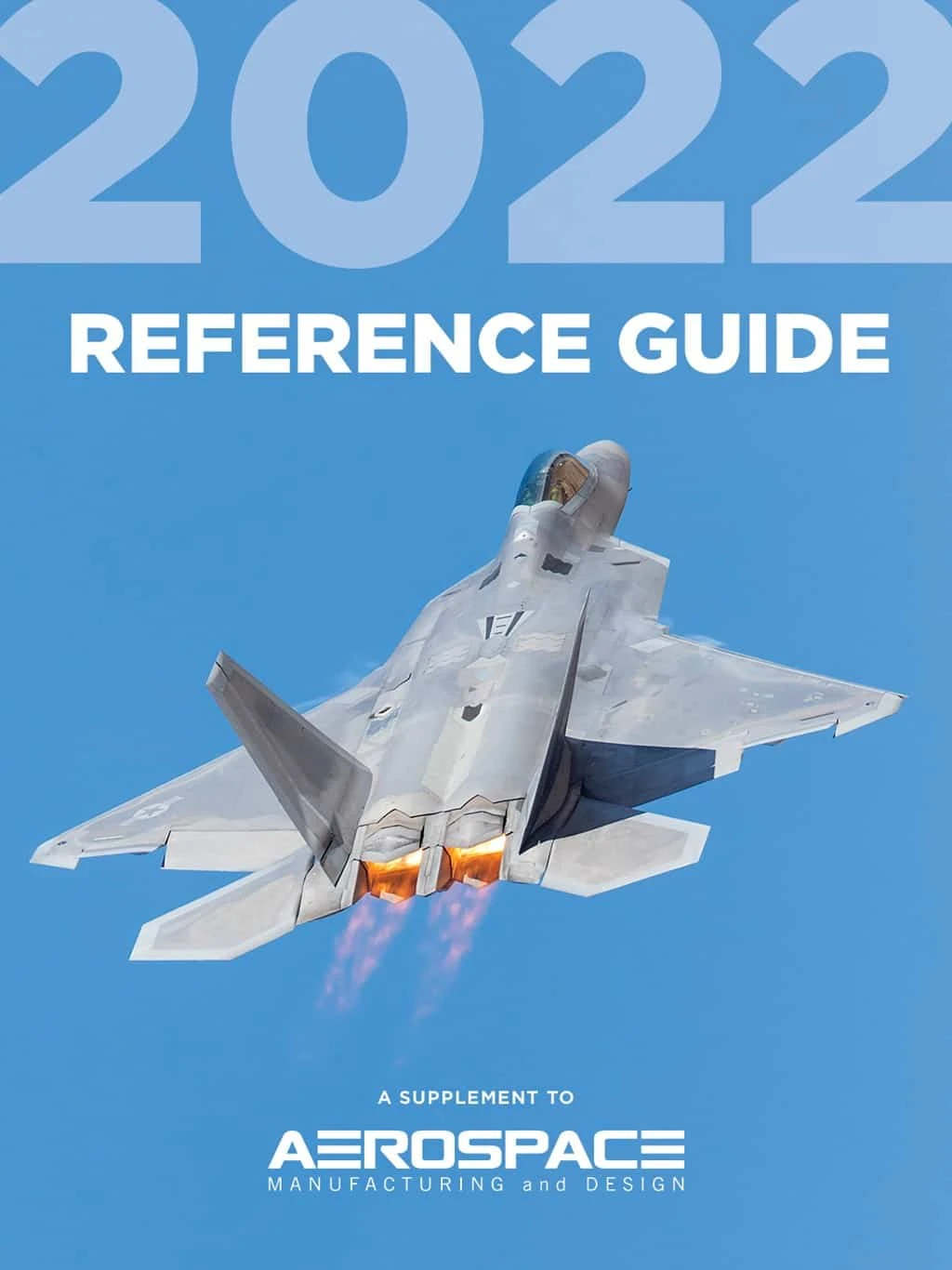
Explore the AMD Reference Guide 2022 Issue
Check out more from this issue and find your next story to read.
Latest from Aerospace Manufacturing and Design
- AAMI project call submission deadline extended to May 12
- Jergens launches cast iron tooling column additions
- Airbus to acquire assets relating to its aircraft production from Spirit AeroSystems
- FANUC America's Cobot and Go web tool
- Chicago Innovation Days 2025: Shaping the future of manufacturing
- High-density DC/DC converters for mission-critical applications
- #59 - Manufacturing Matters: Additive manufacturing trends, innovations
- ACE at 150: A legacy of innovation and industry leadership