
While encouraging signs show business returning to pre-COVID-19 normalcy, manufacturers in capital-intensive global aerospace and defense (A&D) industries still face potential long-term impacts on supply chains due to major disruptions from the pandemic.
COVID-19 brought a core supply chain challenge to light: inventory surplus. No one could have predicted a global pandemic would stop production on such an enormous scale, suddenly creating excessive amounts of inventory to manage.
Thankfully, leading manufacturers have been able to recoup losses endured during the pandemic and protect cash flow and liquidity by putting an actionable, data-driven inventory optimization strategy in place – starting by gleaning critical insight from inventory in their factories. There are several ways aerospace manufacturers can drastically reduce inventory and establish operational command to thrive in a post-COVID-19 economy.
Avoid excess inventory, shortages
Supply chains can evolve to accommodate changes such as shifts in demand, order mix, product process variations, or outsourcing. While evolution is a natural part of the supply chain cycle, increasingly complex and unexpected changes can significantly impact manufacturers’ ability to create and deliver products if they don’t have the tools to see problems coming and pivot. Failure to react quickly and efficiently can increase inventory or generate shortages that harm the bottom line and customer relationships. These battles become even more problematic when teams rely on antiquated systems.
Spreadsheets and home-grown business intelligence solutions have served manufacturers well in the past, but these resources aren’t sufficient given the growing complexity of globalized supply networks. Despite evolving technology, teams still often turn to spreadsheets because existing systems lack trusted data and workflows. Leading companies are tapping into analytics, automated workflows and dashboards, advanced collaborative tools, and artificial intelligence (AI) to boost visibility and actionability across the factory.
Powerful insights and purpose-built analytics allow teams to quickly prioritize and respond to urgent actions that can’t be predicted with traditional tools; get a global view of supply and demand data; fix inventory and delivery issues when demand changes; share inventory information and collaborate with colleagues on inventory issues; and standardize inventory processes with built-in workflows.

Crisis management
During the pandemic, supply chain leaders learned they need a viable crisis-resilient inventory optimization plan to adjust cash and execute plans quickly for on-time delivery. Although they can’t predict what crisis will upend operations, supply chain leaders know the best defense against disruptions is to be prepared.
Effective ways teams can adapt after a crisis to better manage inventory operations include:
Prioritize, simplify daily work for the buying team – Institute an inventory triage process and establish a simple standard workflow for buyers and procurement leaders so they can focus on the most critical actions first and stay organized in a crisis. Supply chain leaders can also organize specialty teams to tackle the highest priority initiatives, such as shortage or surplus inventory. Collaborating and moving in the same direction frees up time for teams to focus on revenue-building initiatives.
Monitor progress, results to identify buyers who need more support – A spike in current shortages, late placement of purchase orders, or other metrics could highlight instances where buyer workloads must be rebalanced. Managers’ support can relieve some of the burden on team members and keep executive and front-line teams completely in sync and in control of the work ahead.
Manage accountability with task ownership, clear timelines – Leaders must establish operational processes to keep activities moving forward, assign owners and due dates to critical items related to shortages or excess, and report on item status in regular meetings.
Share up-to-date resources to help everyone act quickly, keep production moving – Equip teams with the analytical tools and workflows needed to act quickly on shortages and other procurement issues to avoid production stoppages. Align all team members on which parts and customer orders are most critical and which suppliers are most vulnerable. Equipped with the most accurate information, teams can prioritize the supply needed and determine how to allocate constrained supplier and production resources.
Conclusion
Although COVID-19 upended the aerospace supply chain in 2020, manufacturers can take control of inventory management to achieve resiliency and agility as they continue to ramp up operations. As 2021 brings the promise of a return to normalcy, aerospace supply chain leaders can get back in charge by using advancements in factory technology to address long-term industry impacts and any future crisis that might cause disruption.
About the author: Richard Lebovitz is the founder and CEO of LeanDNA, an analytics platform for factory inventory management. He can be reached at richard.lebovitz@leandna.com.
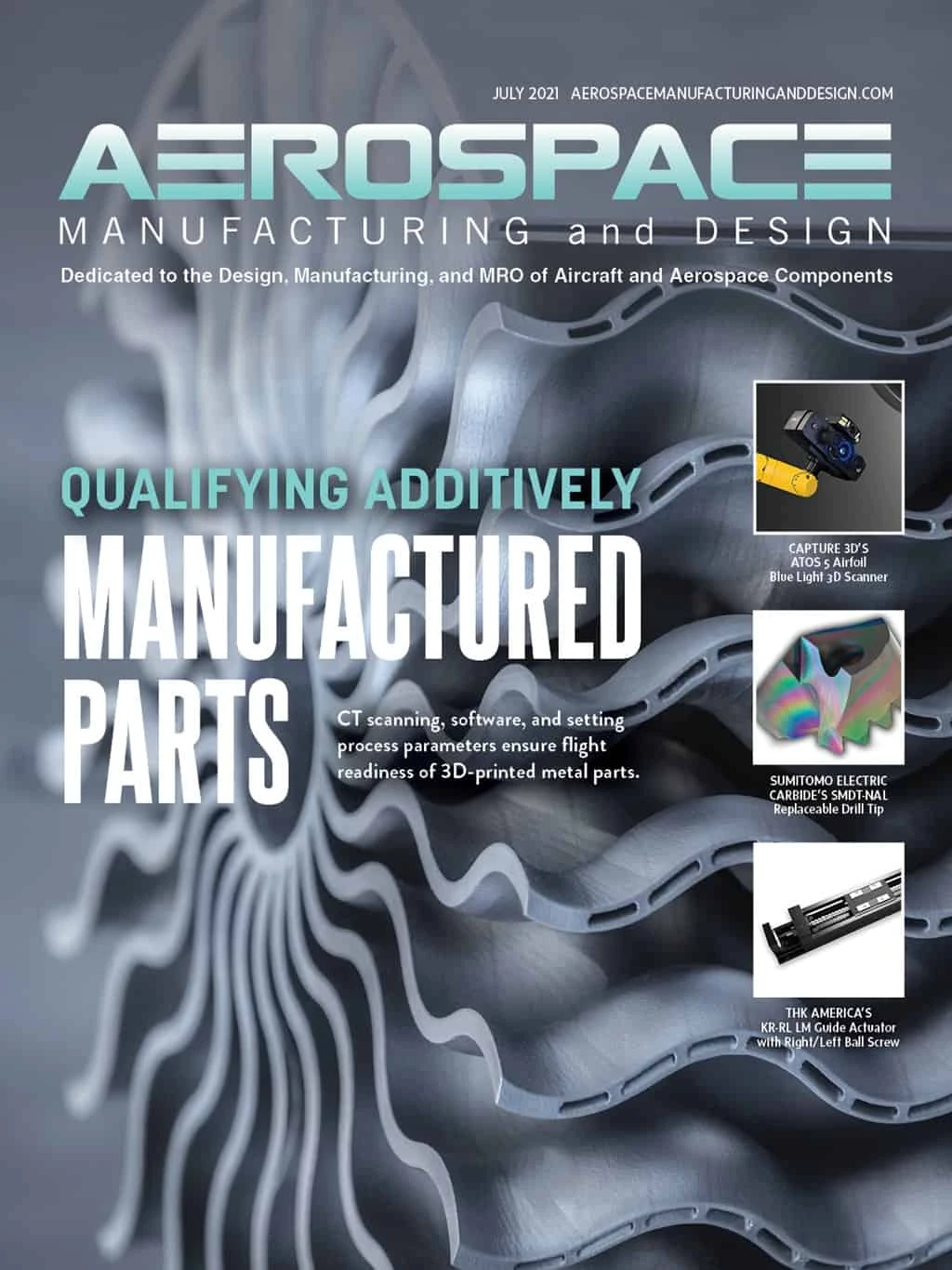
Explore the July 2021 Issue
Check out more from this issue and find your next story to read.
Latest from Aerospace Manufacturing and Design
- Revitalizing the Defense Maritime Industrial Base with Blue Forge Alliance
- Safran Defense & Space opens US defense HQ
- Two miniature absolute encoders join US Digital’s lineup
- Lockheed Martin completes Orion for Artemis II
- Cylinder CMMs for complex symmetrical workpieces
- University of Oklahoma research fuels UAS development
- Motorized vision measuring system
- Everyone's talking tariffs