Mott Corp.’s porous 3D printing technology can quickly manufacture custom sintered metal filtration and flow control products that provide more uniform pore size distribution and flow permeability in virtually any configuration. Presented at the International Conference on Sintering in San Diego, California, by Dr. Vince Palumbo, Ph.D., the technology allows rapid creation of customizable dense, porous, and porous-dense hybrid solutions. In conjunction with proprietary 3D printing techniques, innovative computational fluid dynamics (CFD) algorithms ensure specific part density and geometries are optimized for mission-critical applications.
Mott
www.mottcorp.com

Fatigue testing for component reliability
Testing company Toolcraft is using metrology to assess the fatigue strength of various metals used in additive manufacturing.
By alternating tensile and fatigue tests, the Smith diagram and other fatigue diagrams can evaluate stresses relevant to a system, resulting in material reliability.
During fatigue testing, researchers examine materials using the Wöhler method, evaluated with the DIN 50100 standard. The test begins by clarifying tensile and compressive stress, bending stress, and torsional stress. Then, test pieces are produced in accordance with the applicable standards. This process is generally performed in conformity with the DIN 50125 standard. Recent trends require high-cycle fatigue tests, in which materials are exposed to more than 10 million load cycles. Plotting the load level against the number of cycles allows a Wöhler curve to be calculated. A condition-monitoring system analyzes how the material behaves during the alternating stress, identifying limits for durability of the component in use.
Toolcraft
www.toolcraft.de

CPW, Magnitude partner on AM
Metal powder supplier LPW Technology Ltd and process development company Magnitude Innovations Ltd. are combining their additive manufacturing (AM) experiences to support industrialization of metal AM.
LPW Chief Operating Officer Ben Ferrar says, “In partnership, LPW and Magnitude will support their clients with metal powders, design, process, and application support, helping manufacturers overcome production challenges throughout the complete AM value chain. The projects undertaken together will offer a tailored, turnkey solution to the adoption of AM technologies.”
LPW Technology Magnitude Innovations3D printing software with cloud-based computation
Silicon Valley-based Carbon’s new 3D printing software update expands its tools to design, engineer, and make polymeric parts using digital light synthesis (DLS) technology and resins. A variety of tools enable customers to print parts the first time, optimize supports for material use, and minimize post-processing. The software uses cloud-based finite element analysis (FEA) to simulate the forces of DLS.
This cloud-connected approach allows Carbon to integrate its unit operations and offerings, and the six-week release updates continually optimize customers’ hardware to ensure peak performance and streamline introductions of new resins.
Carbon
www.carbon3d.com
Supersonic metal 3D printing
Designed for scalable, just-in-time production, SPEE3D prints brackets, manifolds, and engine components in single or high-volume production quantities, economically, on-demand, and at speeds 100x to 1,000x faster than traditional metal 3D print technologies.
Rather than using heat to melt metal powders, SPEE3D’s technology uses supersonic deposition in which a rocket nozzle accelerates air up to 3x the speed of sound to deliver manufacturing-grade metal and high-density parts.
SPEE3D is currently installed at Charles Darwin University where the institution is researching new applications for the technology. Aluminum and copper are SPEE3D’s initial focus.
Spee3D
3D printed satellite launched from International Space Station
Tubesat-POD (TuPOD) is the first completely 3D-printed satellite to be launched from the International Space Station (ISS). Manufactured by CRP USA of Mooresville, North Carolina, it uses the company’s Windform XT 2.0 carbon fiber-reinforced composite material.
TuPOD, which includes a 3U CubeSat with a deployment platform for two smaller Tubesats satellites, was developed because the cylindrically shaped Tubesats are not compatable with the normal P-POD Cubesats platform on the ISS.
The platform is an international collaboration between CRP USA, Teton Aerospace (Tetonsys), Morehead State University, JAXA, and TubeSat teams from Brazil’s Escola Municipal Presidente Tancredo de Almeida Neves and National Institute for Space Research (INPE). www.crp-group.com; www.windform.com.
Get curated news on YOUR industry.
Enter your email to receive our newsletters.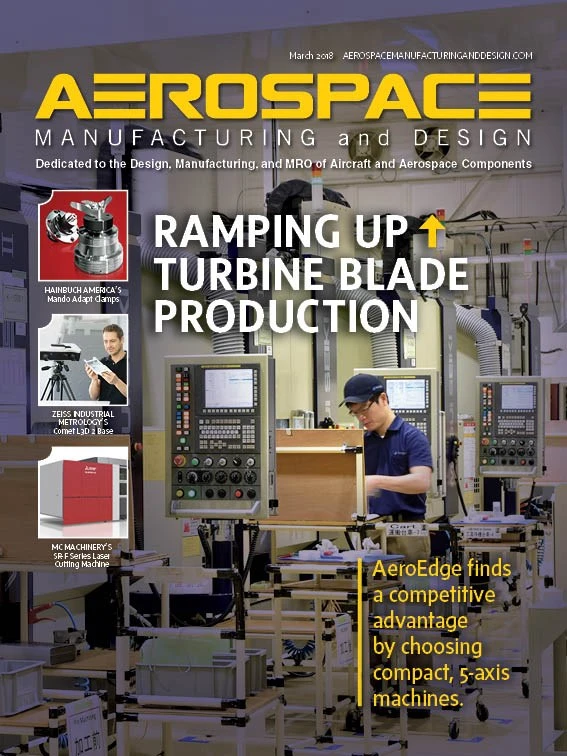
Explore the March 2018 Issue
Check out more from this issue and find your next story to read.
Latest from Aerospace Manufacturing and Design
- GE Aerospace secures Air Force engine contract
- Thomson Industries' online sizing and selection tool
- #53 - Manufacturing Matters - 2024 Leaders in Manufacturing Roundtable
- Join us for insights on one of the hottest topics in manufacturing!
- You can still register for March’s Manufacturing Lunch + Learn!
- Ohio creates Youngstown Innovation Hub for Aerospace and Defense
- Tormach’s Chip Conveyor Kit for the 1500MX CNC Mill
- How to Reduce First Article Inspection Creation Time by 70% to 90% with DISCUS Software