
A non-contact measurement technique, polarized structured light (PSL), enables handheld, 3D-inspection to identify the severity of corrosion pits, scratches, wear scars, and other defects on precision machined surfaces in less than 10 seconds, with micrometer resolution and repeatability. Instruments based on the PSL technology offer the functionality and durability of handheld gages and the resolution of high-end inspection systems, giving quality professionals a new option for quantifying wear and damage on machined components.
Inspectors in maintenance, repair, and operation (MRO) facilities must accurately determine the severity of surface defects to judge whether a component is acceptable as-is, whether it can be refurbished, or whether it should be scrapped. A corrosion pit or scratch tens of microns deep may be sufficient to cause early part failure, particularly in high-speed or high-stress applications. Quantification of fine surface features ensures efficient component function and avoids the development of more severe damage.
Most often, inspectors rely on visual comparisons or scribe checks which, while rapid and easy to implement, are highly subjective and lack precision and repeatability.
More quantitative, high-resolution metrology systems are widely used for measuring surface roughness and dimensions, but they are typically too expensive, slow, and susceptible to vibration for defect measurement on the shop floor. Such instruments are typically sequestered in carefully-controlled metrology labs, making it virtually impossible to measure large components or difficult-to-reach areas of smaller components. Inspectors often make rubber/elastomeric replicas of surfaces which can be measured – a process that may take up to an hour for a measurement that is still subject to variability in the replication processes.
The lack of repeatable measurement options forces inspectors to take an abundance of caution when characterizing defect severity, judging defects conservatively to avoid accepting potentially unsafe components. Millions of dollars are lost to

PSL-based gage
The PSL technique combines fringe projection and dynamic interferometry. Fringe projection (also known as structured light), uses a known pattern that is optically projected onto the test surface and imaged at a different angle onto a detector. The surface’s shape can be reconstructed based on the distortion of the projected pattern. However, multiple patterns, wavelengths, or angles are necessary to create an accurate 3D representation of the test piece. Acquisition time is relatively long, so vibration and instrument motion will degrade measurement results.
Dynamic interferometry enables high-resolution measurement despite vibration by using polarization to further encode the measurement light beam, and a specialized detector with polarizing elements in front of each camera pixel to decode the signal. Information for 3D reconstruction can be acquired simultaneously, in microseconds, enabling a handheld instrument to make accurate measurements in noisy environments. Dynamic interferometry has traditionally been used to measure smooth surfaces with sub-nanometer resolution. On its own, it has not been able to measure larger steps or deep features.
PSL combines the two methods in a high-speed technique with a larger range for measuring vertical features from 0.0002" to 0.1000" (0.005mm to 2.5mm). Its immunity to vibration allows use in handheld systems for improved flexibility. Sub-micrometer resolution is sufficient for imaging defects from machining, wear, and corrosion. Instantaneous measurements reduce the measurement cycle from many minutes to several seconds. Results are quantifiable and can be tied to traceable standards.
Applications
A handheld, PSL-based gage can inspect simple and complex part geometries (see Figure 1, pg. 24.) The PSL technique also can measure defects and features materials with varying reflectivity and roughness (see Figure 2, pg. 24.) In addition to defects, the SPL gage can also measure intentional surface features,

Conclusion
Rapid, portable, high-resolution metrology is essential to maintaining component performance and safety, and for reducing unnecessary scrapping and reworking of expensive components. By enabling in-place measurement, a PSL gage offers manufacturing and repair facilities a cost-effective option for accurate, traceable inspection of surface defects and features.
4D Technology Corp.Get curated news on YOUR industry.
Enter your email to receive our newsletters.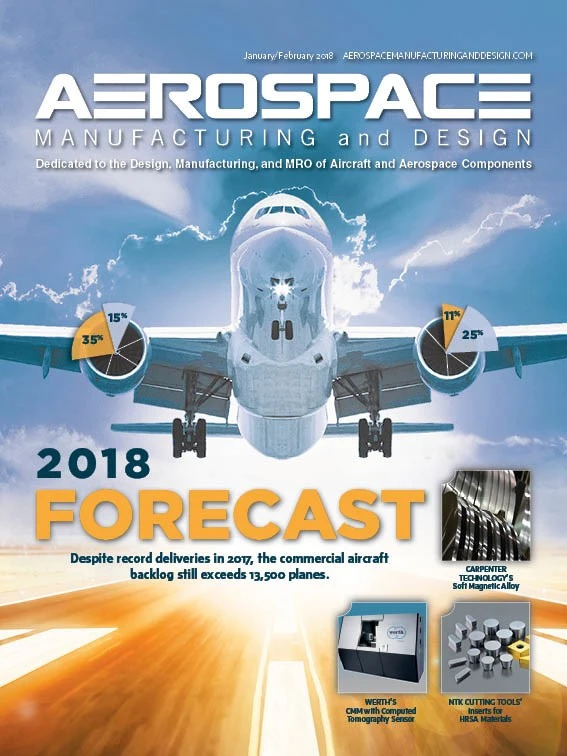
Explore the January February 2018 Issue
Check out more from this issue and find your next story to read.
Latest from Aerospace Manufacturing and Design
- Address the challenges of machining high-temperature aerospace components
- Elevate your manufacturing operations with April’s Manufacturing Lunch + Learn
- America Makes announces IMPACT 3.0 Project Call worth $4.5M
- Updated parting and grooving geometries from Sandvik Coromant
- AIX showcases the future of air travel
- Sunnen Products' PGE-6000 gage
- #41 Lunch + Learn Podcast - SMW Autoblok
- Revolutionizing aircraft design without sacrificing sustainability