
PET carbon fiber (CF), an easy-to-use and versatile composite material, was added to UltiMaker’s portfolio of high-performance materials for S series 3D printers. UltiMaker PET CF offers superior strength, high heat resistance, and high chemical resistance for strong, high-performance thermoplastic applications.
With its exceptional mechanical properties, UltiMaker PET CF enables engineers to produce stronger, more accurate parts for applications such as manufacturing tools, jigs, and fixtures, and end-use parts. Engineers can also leverage the benefits of PET CF for engineering prototypes, enabling easy and extensive testing of technical concepts and functions. PET CF offers a reliable solution for replacing broken or hard-to-source production parts. By using its strong mechanical and thermal properties, manufacturers can swiftly print replacement components, eliminating the need for costly production line shutdowns.
One feature of PET CF is its ability to achieve even higher strength, stiffness, and temperature resistance through annealing. By annealing printed parts, engineers can achieve a temperature resistance up to 181°C and increase strength up to 30% and stiffness up to 10%, producing parts for challenging environments.

Exhibiting low moisture sensitivity compared to other carbon fiber materials, PET CF requires limited drying. When stored in the UltiMaker Material Station, it remains well-conditioned, enabling a reliable printing experience and consistently high-quality prints. PET CF is compatible with dedicated support materials, such as UltiMaker PVA and Breakaway, offering full design freedom and enabling the creation of complex composite parts without limitations.
UltiMaker offers PET CF in multiple colors, including black, gray, and blue, allowing users to color code carbon fiber prints, for specific use cases or aesthetic requirements. The material is fully integrated into the UltiMaker platform through NFC-equipped spools, offering a seamless experience that makes use of NFC material recognition, a dedicated Print Core CC, support material compatibility, and intent profiles.
UltimakerAdditively manufactured propulsion platform for ultra-quiet eVTOLS

MagLev Aero selected GE Additive’s AddWorks consultancy team to support development of additive technologies and materials for its proprietary MagLev HyperDrive aero propulsion platform.
The MagLev HyperDrive applies the same fundamental principles that drive ultrafast, ultraquiet, high-efficiency maglev trains, but in a circular rotor. This approach has the potential to deliver less noise, more payload, elevated safety, and compelling industrial design for high-efficiency electric aircraft.
MagLev Aero’s propulsion-first business model allows its platform to be integrated into different OEMs’ aircraft concepts and eVTOLs, enabling industrial design elements and use cases previously thought impossible with traditional rotor technology. The first generation of eVTOLs has achieved tremendous milestones, improving the viability of Urban Air Mobility. But the industry, to this point, has yet to solve the critical, real-world challenge of take-off and landing noise. MagLev Aero represents the next generation of electric, ultraquiet, high-performance and safe vertical lift propulsion that’s necessary to bring clean energy flights to everyday people.
Get curated news on YOUR industry.
Enter your email to receive our newsletters.
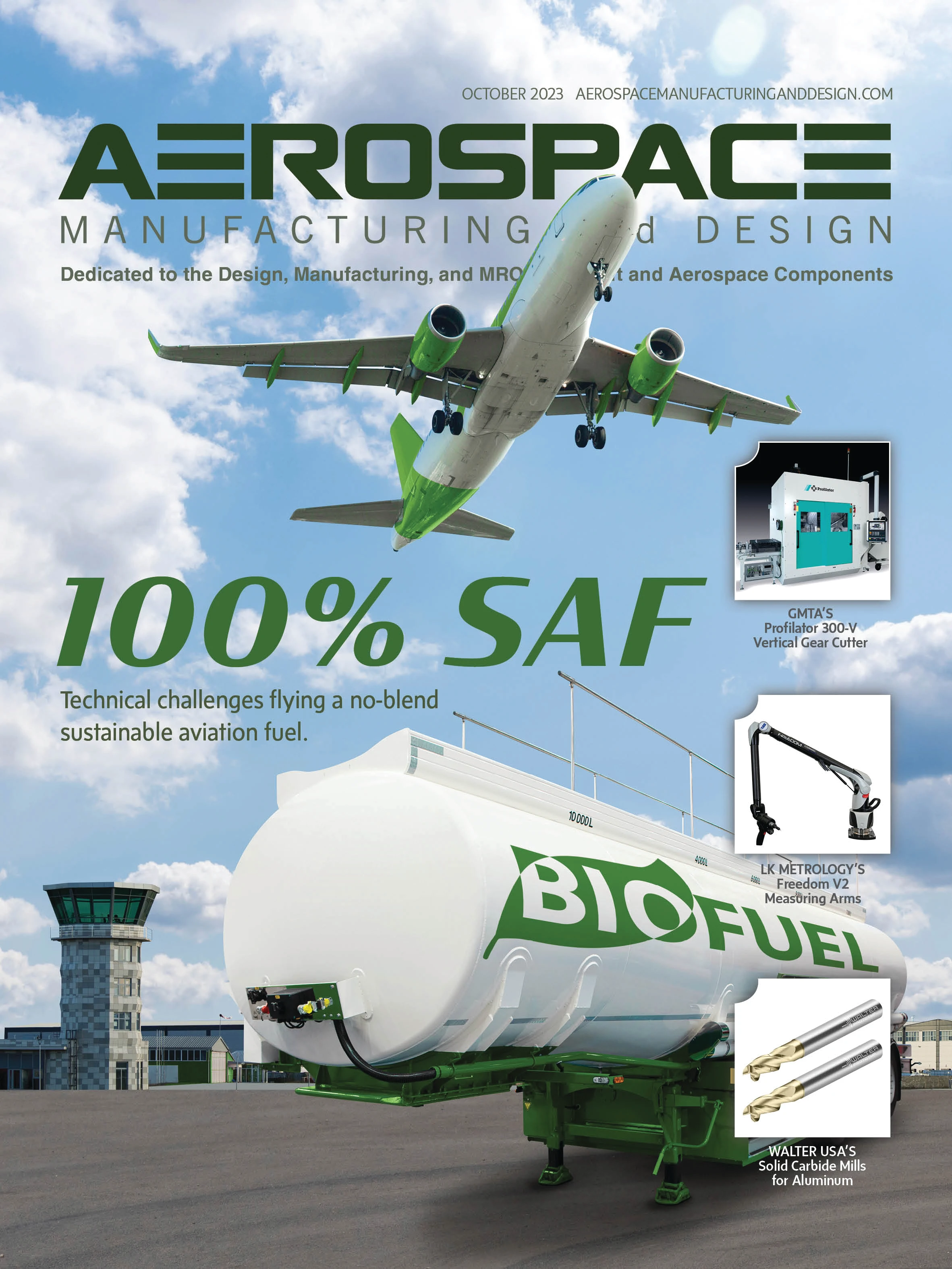
Explore the October 2023 Issue
Check out more from this issue and find your next story to read.
Latest from Aerospace Manufacturing and Design
- Registration is open for April’s Manufacturing Lunch + Learn!
- Natilus begins search for new home to build world's most efficient commercial aircraft
- Aerospace Industry Outlook webinar is back by popular demand
- Automation Webinar with Visual Components
- PrecisionX Group expands manufacturing operations
- Creaform Metrology Suite expands capacities
- United Performance Metals acquires Fabrisonic
- OES’ 30mm vertical lift stage