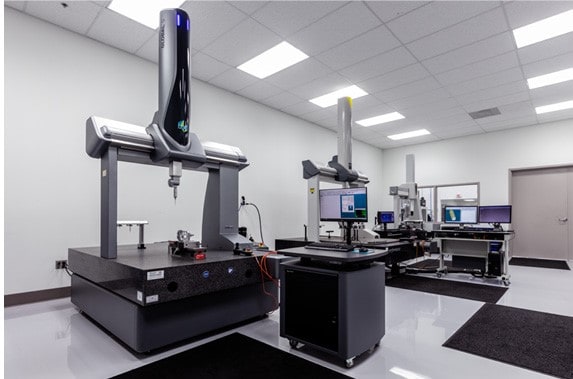
Roush Yates Manufacturing Solutions (RYMS), a division of Roush Yates Engines (RYE), a North Carolina company with a legendary auto racing history, is using a digital manufacturing ecosystem to apply racing’s core values of unwavering quality and instant responsiveness to serve new markets in CNC machining for aerospace and defense (A&D) industries.
RYMS is an AS9100 Rev D-certified, ITAR-registered 88,000ft2 manufacturing facility that machines high performance engine components to support engine design, development, and production at RYE. Their expertise is in CNC machining complex-geometry parts that require precision and robust process control using 4- and 5-axis mills, automation centers, waterjet, multi-axis mill-turn, and Swiss-turn machines. In addition, they offer post-machine surface and secondary treatment processes through validated suppliers.
A digital footprint
In parallel with growing its business, RYMS saw a need to update its manufacturing management processes. Todd English, vice president for strategic partnerships and marketing, explains that manufacturing at RYMS involved several manual activities.
The company’s quality manager was spending a good amount of time collecting hand-written metrology data, so to maximize efficiency, economy, and response to customer needs, it became necessary to streamline the company’s manufacturing management systems.
“We were trying to advance toward a total digital footprint,” English says, so RYMS researched various manufacturing systems software and chose ProShop, a shop management system for small- to medium-sized companies.
In addition to typical enterprise resource planning (ERP) features for estimating, quoting, and purchasing, ProShop includes manufacturing execution system (MES) and quality management system (QMS) control, monitoring, and collection capabilities. The MES tracks machine usage, cutting tool management, work instructions, part inspection data, and other factors. QMS modules manage a company’s ISO 9000, AS9100, API, and ISO 13485 certifications, covering the tasks required to comply with different quality systems, including data for standards, procedures, equipment, users, training, audit reports, non-conformance reports, and corrective actions.
Paul Van Metre, ProShop’s founder, says, “ProShop software represents a digital manufacturing ecosystem or ERP 4.0. It enables shops to manage their business using big data manufacturing analytics, including shop floor monitoring of part quality inspection, work instructions, and tool management. Often, when smaller companies hear about ERP software, they don’t want to take on an unwieldy system that needs an army of people to manage, maintain, and run. ProShop is designed to fulfill the needs and work with the resources of smaller to medium-size operations.”
While many conventional ERP systems are accounting-based, with minimal functionality for managing and controlling the shop floor, systems focused on manufacturing monitoring don’t provide all the information to optimize business strategies. ProShop offers benefits for machine shops, fabricators, job shops, contract manufacturers, and others in regulated industries requiring tight process controls and exacting, timely information. ProShop often can replace five or six separate software packages that may not communicate well with each other, improving profitability and throughput.
English says the software saved a considerable amount of time as RYMS expanded and reorganized its business. “ProShop has allowed us to not only capture quality data but also gave us complete visibility on our manufacturing floor for our various processes. Our machinists are able to view all drawings and input information directly into the system.”
RYMS Quality Manager Kathy Arcoleo says the company uses ProShop to manage all its quality information including non-conformance, supplier evaluation and tracking, customer returns, and corrective action process. “Essentially all the requirements of aerospace standards and our customers’ demands are done electronically within ProShop,” she says.
Totally paperless
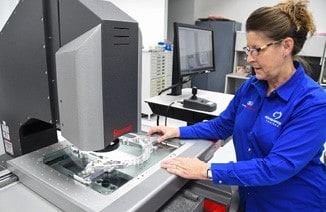
“There are no work orders on the shop floor or procedures in a binder. You won’t find paper following parts around the workshop. It’s very neat and tidy and everything is up to date.”
An auditor before she joined RYMS, Arcoleo says an auditor working in a traditional manufacturing management system might spend half their time looking through paper. “If an auditor asks a question, we don’t have to run and get a document. We can just show them right on a laptop in real time,” she says.
The paperless ProShop enables an auditor to quickly review a large amount of information which “allows them to dig really deep in your business,” Arcoleo says, “The good side of that is if you’re not doing something correctly, they’ll find it.”
Paperless data also permits company-wide access to real-time information. “There might be an order that’s been received but the purchasing person doesn’t know that because the paperwork hasn’t gotten to them or to accounting,” Arcoleo says. “We don’t have those issues because everything’s done in real time.”
Having real-time data available company-wide also makes it possible to get information to customers faster. When data is collected at different locations it’s not always clear if what’s available is current.
“Every operator, every work area, every office person has their own work center and system ID,” Arcoleo says. “Any time you have an electronic transaction that happens quickly is a benefit.”
Naturally occurring scrap
Some scrap occurs naturally in machine shop operations and is anticipated. Arcoleo says, “With ProShop we can evaluate production efficiency and evaluate whether we’re achieving our planned scrap rate…are we losing money or meeting our forecasts? Quality personnel can measure the quality of the product that’s coming out of production and measure the quality of the work that we send to our customers.”
RYMS uses ProShop return merchandise authorizations (RMAs) to track quality the customers receive, and non-conformance reports (NCRs) track production scrap rates and internal non-conformances. “We want to make sure that when we’re charging our customers for setup, we’re charging them for the real cost of what it takes us to manufacture and not just the part that we provide,” Arcoleo explains.
Sales & service value
“On our virtual tours and in person, we talk about our paperless floor,” English says. “We show that there aren’t any work orders or prints, that everything is computerized, and we can make measurements and update the system in real time. It’s definitely a sales tool for current as well as potential customers.”
Paperless operation also facilitates customer support. Arcoleo says the shop floor isn’t a good environment for paper because it gets dirty, greasy, lost, and torn and by the time it gets to inspection, it’s not always readable.
“We tend to have big drawings and the fact that the operators can zoom in and look at things electronically on their computer screens is a huge benefit. We do some pretty complicated machining with a lot of geometric dimensioning and tolerancing (GD&T), and if the operator has a question and we have a customer on the line, we share that information and get questions answered in real time,” Arcoleo explains.
Expert resources support progress

English says about the evolution of RYMS, “There’ve been a lot of steps in our growth, but if you look at the Roush Yates leadership, if you look at the vision, if you look at the employees, we’ve combined that with industry leaders like ProShop that continue to elevate our business. I think it’s important that, as we continue to grow, there are subject matter experts that we’ll align with to support our growth.”
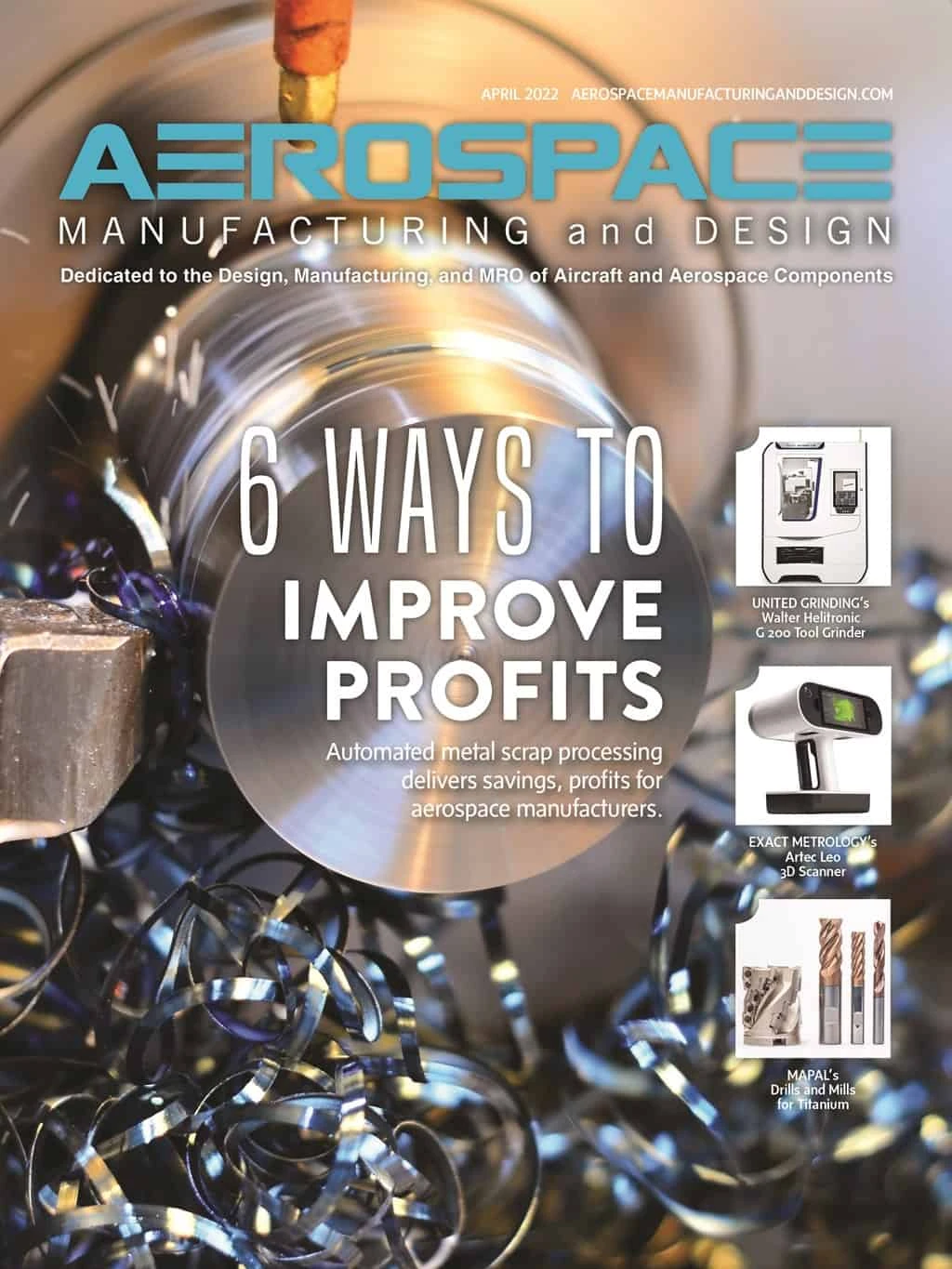
Explore the April 2022 Issue
Check out more from this issue and find your next story to read.
Latest from Aerospace Manufacturing and Design
- Revitalizing the Defense Maritime Industrial Base with Blue Forge Alliance
- Safran Defense & Space opens US defense HQ
- Two miniature absolute encoders join US Digital’s lineup
- Lockheed Martin completes Orion for Artemis II
- Cylinder CMMs for complex symmetrical workpieces
- University of Oklahoma research fuels UAS development
- Motorized vision measuring system
- Everyone's talking tariffs