
If it can ignite, it can burn. In mission-critical aerospace applications, even the smallest source of contamination can lead to dangerous combustion. This threat increases in oxygen-rich environments, where the steady supply of oxygen can easily support the ignition and sustained burning of certain materials. Minimize these risks by selecting pressure control components that are verifiably cleaned and designed with oxygen-compatible materials. This combination will ensure the safety of high-pressure oxygen equipment in applications such as astronaut breathing support and rocket engine fuel pressing.

Meet enhanced cleanliness standards
Oxygen is highly reactive in nature so any components or systems operating in the presence of liquid or gaseous oxygen must be verifiably cleaned. Meticulous cleaning is fundamental to ensuring the safe operation of an oxygen system by ridding the equipment of foreign object debris (FOD) and combustible residue that could serve as an ignition source.
ASTM G93, ASTM International’s current cleanliness standard for equipment in oxygen-enriched environments, and Compressed Gas Association (CGA) G-4.1, which outlines the methods for cleaning equipment for oxygen service, are accepted industry standards that must be met for basic-level oxygen cleaning. However, many mission-critical aerospace applications involving high-pressure oxygen and other oxidizers require enhanced and verifiable levels of cleanliness.
For these critical applications, TESCOM offers enhanced cleaning options including IEST-STD-CC1246E, the industry standard for enhanced cleaning for critically clean applications. This standard, issued by the Institute of Environmental Sciences and Technology (IEST), specifies and determines product cleanliness levels for contamination-critical products by focusing on contaminants that impact product performance. It also covers stainless steel, high-strength alloys, specialty metals, brass, aluminum, plastics, and elastomers.
The current IEST-STD-CC1246E standard is a revision of MIL-STD-1246 in an effort to expand its usefulness beyond military applications. Unlike the MIL standard, the IEST specification defines the cleanliness levels for products that include various components and fluids.


Choose the right materials
Just because a material is oxygen-cleaned and free of combustible residue and FOD doesn’t mean it can’t ignite. Selecting suitable materials is as important as thorough cleaning processes. When it comes to pressure control components, it’s important to consider a material’s oxygen index, autoignition temperature, and heat of combustion.
Oxygen index is the minimum concentration of oxygen needed for a material to continue to burn on its own once it ignites at atmospheric pressure. Materials with a high oxygen index are preferred for oxygen service; the higher the oxygen index, the lower the propensity of a material to ignite and burn. Conversely, the lower the oxygen index, the higher the propensity of a material to ignite and burn. Soft goods such as Teflon, polychlorotrifluoroethylene (PCTFE) and fluoroelastomers (FKM) are generally accepted due to their high oxygen index.
Autoignition temperature is the temperature at which a material autoignites in the presence of pressurized oxygen. Materials with a high autoignition temperature are preferred for oxygen service. Materials such as Teflon and PCTFE are preferred, as they have high autoignition temperatures.
Heat of combustion is the amount of energy released by a material when it burns in oxygen. Materials with a low heat of combustion, such as Teflon, PCTFE, and Vespel SP21, are preferred.
For metals, the minimum burn pressure is critical since it’s the minimum oxygen pressure where a metal will continue to burn on its own after ignition. Burn-resistant metals like Monel and brass are highly preferred for oxygen service. Stainless steels and aluminum have very low minimum burn pressures and generally are not recommended in oxygen-rich environments, even at relatively low pressures. Materials used in the flow stream of oxygen systems – lubricants, thread seals, and even unintended materials like compressor oils – shouldn’t be overlooked in minimizing the risk of an oxygen fire.

Partner with the right supplier
In addition to using only oxygen-cleaned and oxygen-compatible pressure components for applications, an additional benefit is partnering with the right supplier who can provide oxygen-compatible parts and deliver components according to cleanliness specifications.

Suppliers with in-house basic or enhanced cleaning capabilities offer significant time and cost savings compared to in-house cleaning processes or third-party services, which can drive up lead times by weeks or months. Many third-party cleaning services may not have the technical expertise to reassemble components correctly once cleaned, increasing the risk of product failure.
Choose a supplier that can help you select the right pressure control solutions constructed of oxygen-compatible materials and offers in-house cleaning services to keep your lead times and costs as low as possible.
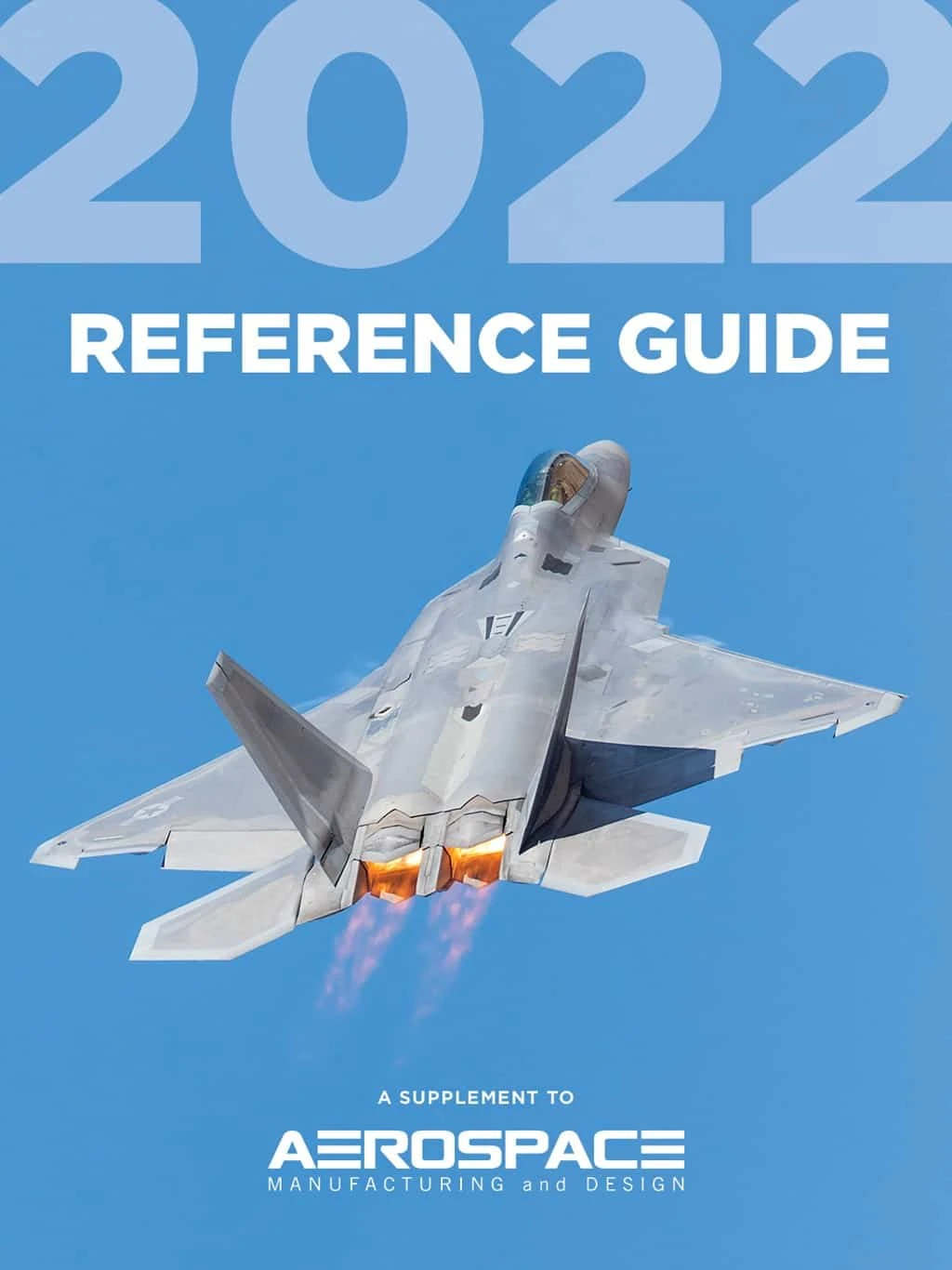
Explore the AMD Reference Guide 2022 Issue
Check out more from this issue and find your next story to read.
Latest from Aerospace Manufacturing and Design
- AAMI project call submission deadline extended to May 12
- Jergens launches cast iron tooling column additions
- Airbus to acquire assets relating to its aircraft production from Spirit AeroSystems
- FANUC America's Cobot and Go web tool
- Chicago Innovation Days 2025: Shaping the future of manufacturing
- High-density DC/DC converters for mission-critical applications
- #59 - Manufacturing Matters: Additive manufacturing trends, innovations
- ACE at 150: A legacy of innovation and industry leadership