
Hansen Engineering Co. (HEC) is a Harbor City, California, aerospace engineering shop, with most of its modern, high-speed enclosed CNC machines operating from 10,000rpm to 15,000rpm – cutting large blocks of titanium, stainless steel, and aluminum. Toolholders were getting stuck in the spindle due to deformation, fretting on contact surfaces, and increasing cycles. Persistent problems lead to shutdowns to allow the machines time to cool off. Additionally, poor finish and chatter problems were recurring when roughing aluminum, titanium, and stainless steel.
Eliminating toolholder expansion – a condition that occurs when a standard retention knob is installed into a toolholder – can boost performance in CNC milling. Pressure exerted by thread engagement, coupled with elastic properties of toolholder steel, creates a bulge at the small end of the holder. Once expansion occurs, the holder will not pull all the way into the spindle, will fail to contact more than 70% of the spindle surface. The bulge stops the toolholder from making full contact with the spindle taper, causing vibration, chatter, poor tolerances, non-repeatability, poor finish, shortened tool life, excessive spindle wear, run-out, and shallow depths of cuts. Eliminating the bulge reduces downtime, extends tool life, and increases speed and feed rates.
JM Performance Products Inc. (JMPP) of Fairport Harbor, Ohio, a manufacturer of CNC mill spindle optimization products since 2009, recognized a bulge-related design flaw in V-flange tooling was responsible for CNC boring and milling problems. A high-torque retention knob for use in existing toolholders eliminated the bulge.

HEC engineering personnel met with JMPP’s technical team for a demonstration on how the high-torque retention knobs would benefit their 50 taper V-flange toolholders. JMPP’s high-torque retention knobs are longer and reach deeper into the holder’s threaded bore. Thread engagement occurs in a thicker cross-section of the toolholder where material is better able to resist deformation. Eliminating V-flange tooling flaws allowed HEC to increase machine speeds, offering savings of 10% to 15%.
HEC installed 25 high-torque knobs, abiding by calculated torque specs and using a retention knob socket and torque wrench. Immediately, HEC machinists noticed a 5% spindle load decrease using a 3.0" hi-feed insert mill running titanium. HEC also installed them on an aluminum forging job they were running that had consistently produced chatter problems. Among the tools tested for this job were a 1-1/4" diameter knuckle rougher and 2.0" diameter finisher.
HEC Shop Lead Man Curtis Sampson says, “The chatter was eliminated, and it produced the best finish we have ever seen on these parts. After that, we bought 50 more pieces and immediately noticed improvements all around the table – we’ve been increasing their use over time ever since.”
By converting 14 CNC machines with approximately 120 JMPP high-torque retention knobs per machine, HEC increased productivity 15% and decreased downtime.
HEC Buyer - Tool Crib Jose Campos says, “Productivity has continued to increase by approximately 15%. The same rate applies for downtime as there is less change-out of tool cutters across the board.” Campos notes that in 2015 a HEC machine with spindle running at 10,000rpm and 350ipm feed on aluminum parts used 170 high-torque retention knobs. In 2016 the company used 300 high-torque knobs. The progressive conversion to JMPP’s high-torque retention knobs allowed HEC to overcome long-standing productivity issues for its entire fleet of high-speed CNC mills.
Campos says improvements on HEC’s Mazak 5-axis CNC machining center, featuring 160" length with dual shuttle tables and a tool-changer designed to run one table full of parts while the other is being loaded. “Our Mazak machines used to make a loud noise when changing tools, and JMPP’s high-torque retention knobs solved that problem,” Campos says. “The machines are much quieter now when roughing titanium and stainless steel. They also eliminated fretting of the toolholder shank.”
The retention knobs have shown lower spindle loads, which is better for the machine, and when roughing titanium and stainless steel with the knobs, HEC used less power while improving tool life.
Hansen Engineering Co.
JM Performance Products Inc.
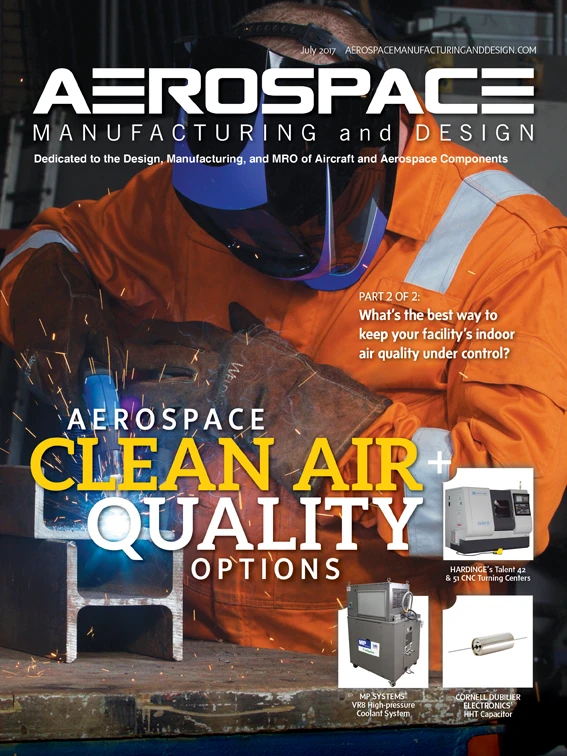
Explore the July 2017 Issue
Check out more from this issue and find your next story to read.
Latest from Aerospace Manufacturing and Design
- America Makes announces IMPACT 3.0 Project Call worth $4.5M
- Updated parting and grooving geometries from Sandvik Coromant
- AIX showcases the future of air travel
- Sunnen Products' PGE-6000 gage
- #41 Lunch + Learn Podcast - SMW Autoblok
- Revolutionizing aircraft design without sacrificing sustainability
- GE Aerospace awarded subcontract for FLRAA next phase
- KYOCERA Precision Tools publishes 2025-2026 Indexable Cutting Tools Catalog