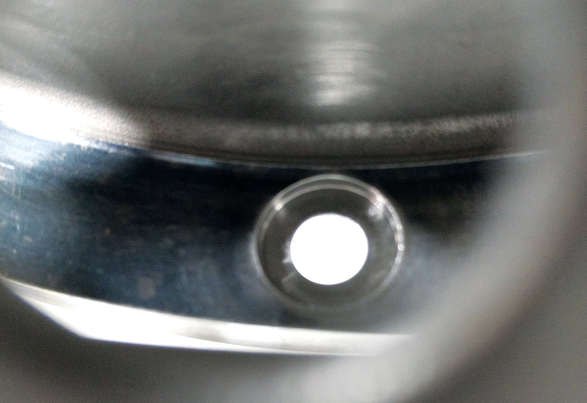
Aerospace industry specs often call for a part to be machined to the thousandth of an inch. In an ideal world, that level of precision wouldn’t sacrifice production time or tool longevity. Whitcraft Group, a manufacturer of aerospace components, is living in that ideal world, machining parts accurately, quickly, and without tool failure.
Mike Anderson, lead/supervisor of the Bearing Housing Flow Line at Whitcraft, gives the credit to the Back spot facing (BSF) tool from Heule Tool he recently brought into the shop’s line. The BSF has sped up production time, decreased insert costs, and increased tool longevity, without sacrificing precision.
Broken parts ground production
Whitcraft commonly works with components machined from forgings or sheet metal welded to forgings. For the bearing housing for a new engine – cast of Inconel 718 then heat-treated to roughly 50Rc – the main bore required spot facing a 0.278" diameter hole with a back-bore diameter of 0.535", ±0.008". They run a Cat 40 vertical machining center with an Okuma 1,000psi, through-spindle at 55sfm at 345rpm.
Anderson initially looked at Heule Tool, but they didn’t offer a stock insert for that diameter. He purchased tooling from another supplier to achieve this back spot facing. However, after two holes, the blade would break, and the operator would stop production to remove the broken blade and insert a new one. The tool was an insert rotated on a through-pin, so changing the blade required the operator to align it perfectly, a time-consuming task. The part needed 10 holes, requiring an operator to change out five tools, with no small bit of frustration per part.
A Heule representative later informed Anderson that they had added a BSF small enough for Whitcraft’s use on the bearing housing, the BSF-A-0700/040-7.5, which Anderson quickly purchased.
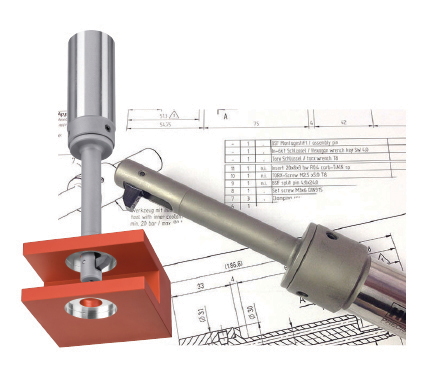
Cleared for takeoff
Heule Tool’s BSF is an automatic back spotfacer that retracts the boring blade by coolant pressure. Designed for CNC machining, the BSF functions without an anti-rotation device, change of spindle direction, or contact mechanism. The blade expands using centrifugal force when the spindle is activated. Coolant pressure moves a piston, pushing a pin that forces the blade back into the blade housing when deactivated.
The tool and blade have coolant pipes that continuously flush the blade window and the blade with coolant, keeping the section clean and optimizing chip removal. For Anderson, this meant the blade would reliably retract and no material would jam the blade or get stuck in the cavity.
The Heule BSF machined 10 holes in one blade, allowing one blade per part, reducing tool consumption and production downtime by 80%. With replaceable blades, the time between parts decreased.
Savings without the sacrifice
Anderson estimates that the entire process for one part takes 7 minutes, 45 seconds with the Heule BSF, down from 62 minutes with the competitor’s tool (a nearly 90% descrease). The blade parts for the competitor cost $410 per part, while the Heule tool costs $120 per part. With more than 300 parts per year, the Heule BSF saves Whitcraft $130,000.
Even more powerful was the time saved – more than 250 hours of production time per year. That time savings doesn’t include training – the easily-changeable blade on the Heule tool allows less-skilled operators to be just as successful as experienced ones and closes the training gap with new employees more quickly.
“The time savings is significant,” Anderson says, “Getting rid of the user input allows our operators to do other tasks and lets the machine run.”
Now that his operators are changing blades one-fifth of the time they used to, manufacturing the bearing housing is faster and more cost effective than before, allowing Anderson to pass those savings along to his customers, ensuring they’ll return for more machining needs in the future.
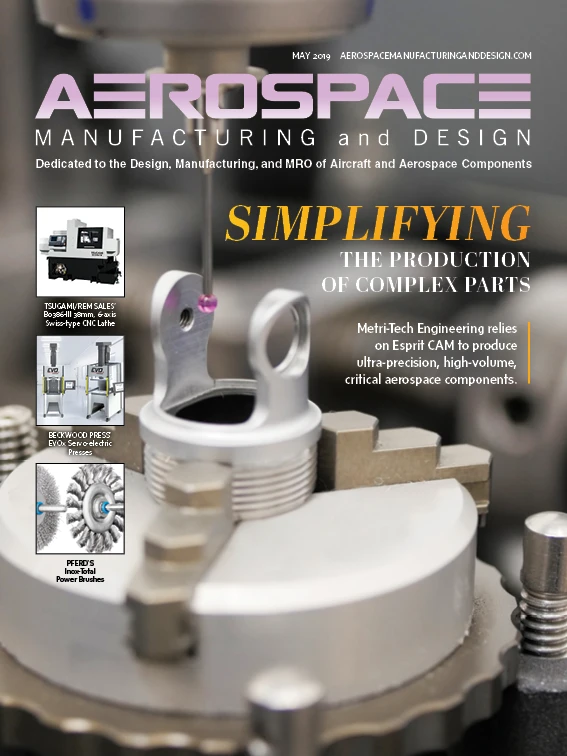
Explore the May 2019 Issue
Check out more from this issue and find your next story to read.
Latest from Aerospace Manufacturing and Design
- Piasecki acquires Kaman's KARGO UAV program
- PI Americas’ long-travel XY piezo nanopositioners-scanners
- AAMI project call submission deadline extended to May 12
- Jergens launches cast iron tooling column additions
- Airbus to acquire assets relating to its aircraft production from Spirit AeroSystems
- FANUC America's Cobot and Go web tool
- Chicago Innovation Days 2025: Shaping the future of manufacturing
- High-density DC/DC converters for mission-critical applications