
The solid-carbide TC685 Supremeorbital drill/thread milling cutter reduces hard machining time by producing the core hole, chamfer, and thread in one operation. The cutter’s face milling geometry is designed for core hole creation and chamfering. After chamfering to start a hole in the workpiece, the tool creates the core hole and thread using helical interpolation.
Applications include blind-hole and through-hole threads in steel and hardened steel from 44HRC to 65HRC (ISO P and H materials). The tool produces thread depths of 2xDN and 2.5xDN and is suitable for machining a range of metric thread sizes from M2 to M20.
The left-hand cutting tool features a 15° helix angle for excellent chip removal. Cooling with compressed air makes it possible to achieve maximum tool life in materials harder than 50HRC. Internal coolant delivery is available for tools creating the M6 size through the larger thread sizes. The tool shank is in accordance with the DIN 6535 HA standard.
New geometry and post-treatment process reduces torque requirements and extends tool life.
Horizontal lathe with high-torque spindle

The LB3000 EX III horizontal lathe is built on the manufacturer’s Thermo-Friendly Concept to ensure minimal thermal growth, and slanted box bed construction offers high quality and rigidity. Equipped with a high-power, high-torque PREX motor, the machine delivers heavy- to high-speed cutting.
The operator-friendly, open-architecture OSP-P500 CNC control makes the machine easy to operate and integrate with other peripheral equipment. A variety of bed lengths, bore sizes, and options includes live tooling, sub-spindle, and Y-axis.
Okuma America Corp.
IMTS 2024 booth #338500
Quick-change receiving plate

The QCR Quick-Change Receiver manually actuated cam-lock receiving plate attaches to CNC lathe spindles and significantly reduces the time needed to change workholding clamping devices. With the QCR, the time needed to switch I.D./O.D. collets, jaw chucks, or face driver workholding devices on a machine is cut from one hour to five minutes. The QCR also features automatic release of the draw connections.
It’s available for all standard nose configurations, for spindle sizes from A2 - A5 through A11, and flatback spindles. The QCR also comes in a through-hole design for through-spindle bar feeding operations.
Engineering the receiver so only two adapter plates are necessary allows the QCR to be modular and standardized.
Speedgrip Chuck Co.IMTS 2024 booth #432268
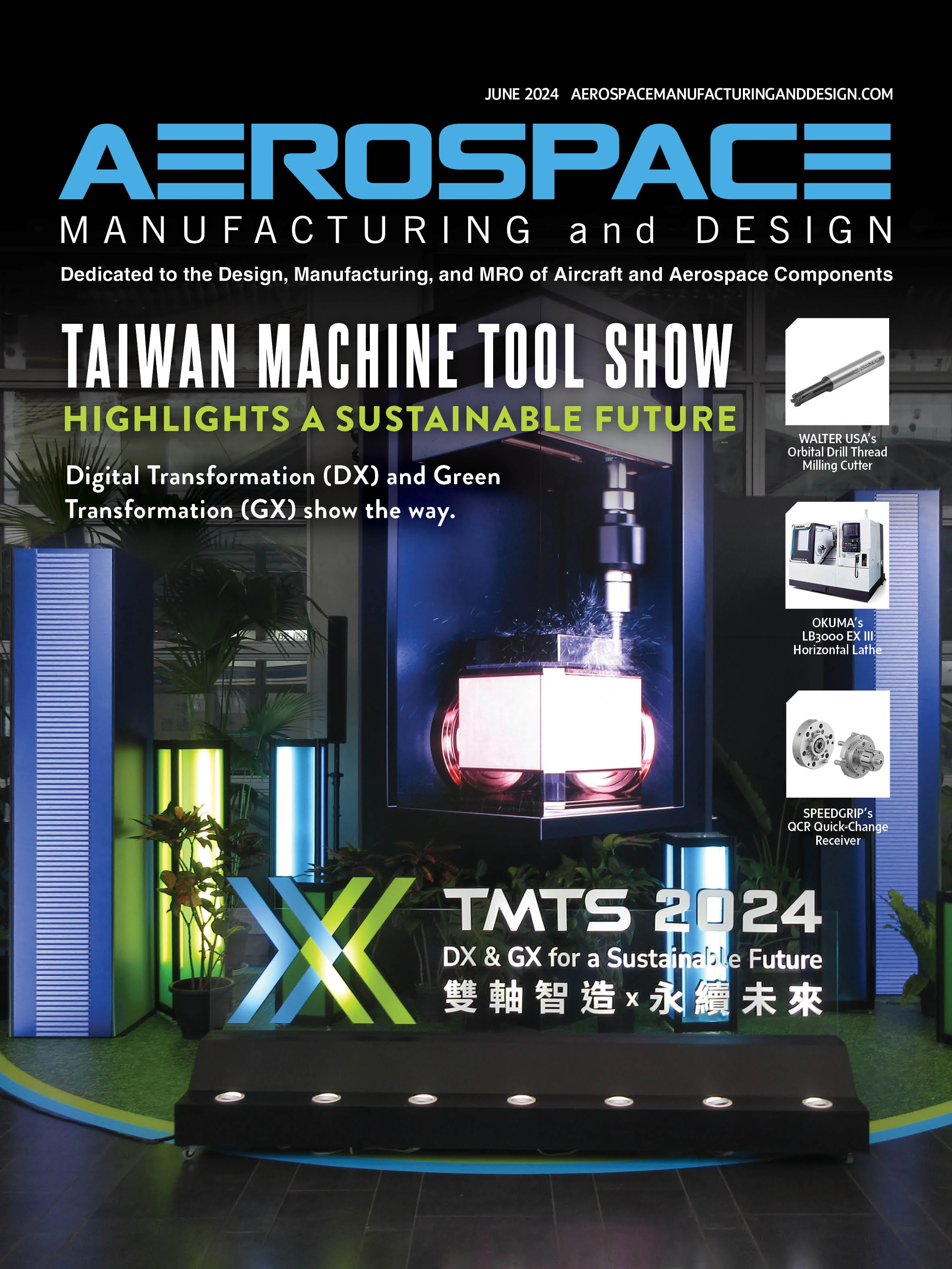
Explore the June 2024 Issue
Check out more from this issue and find your next story to read.
Latest from Aerospace Manufacturing and Design
- Piasecki acquires Kaman's KARGO UAV program
- PI Americas’ long-travel XY piezo nanopositioners-scanners
- AAMI project call submission deadline extended to May 12
- Jergens launches cast iron tooling column additions
- Airbus to acquire assets relating to its aircraft production from Spirit AeroSystems
- FANUC America's Cobot and Go web tool
- Chicago Innovation Days 2025: Shaping the future of manufacturing
- High-density DC/DC converters for mission-critical applications