
Several trends affect the aerospace industry’s ability to reduce costs while improving quality and productivity. It’s a tremendously complex and globalized industry, and international trade agreements can disrupt the supply chain.
Original equipment manufacturers (OEMs) are consolidating and partnering, producing bigger companies with greater ability to pressure suppliers. Notable examples: Airbus invested 50.1% in Bombardier’s CSeries program, rebranding it the Airbus 220, and Boeing purchased an 80% stake in Embraer.
To meet growing orders, OEMs are becoming assemblers, increasingly turning to the supply chain to develop complete modules and systems. This heavily impacts the supply chain as OEMs’ specifications become more complex, adding stricter quality requirements and intellectual property transfer clauses.

Facing increased risk, suppliers are also consolidating. Rockwell Collins acquired B/E Aerospace in 2016, and before this deal even closed, United Technologies purchased Rockwell. With higher outsourcing producing increasingly complex parts and assemblies, expectations grow for every level of the supply chain. The pressure becomes more intense as non-traditional suppliers enter the marketplace with agile business structures, the ability to innovate rapidly, and a willingness to accept more risk.
Collaboration, visibility
Effectively managing a global industry with thousands of suppliers and numerous programs requires all stakeholders to undserstand what is being communicated. The greater the exploitation of common information throughout the supply chain, the higher the likelihood of efficiency and innovation.

Digitalization is the first step to improving visibility; but more important is the extent to which digital information is integrated. Using tools that aren’t connected inhibits meeting demands. Digital technologies should be shared on a common information technology (IT) platform uniting suppliers for collaboration, visibility into problems, interdependencies, and consequences of any actions.
Suppliers may balk at the idea of having to update IT systems while facing already tight margins, but it will be difficult to survive the pace of today’s requirements with outdated systems. However, evolving to a fully secured, flexible, and scalable cloud platform doesn’t require high IT investment. Boeing, Airbus, and others use Dassault Systèmes’ 3DExperience platform, uniting computer aided design (CAD), manufacturing, project lifecycle management (PLM), and business system software, granting their supply chain access to the network. Suppliers looking to increase their ability to innovate, meet requirements, deliver on time, and reduce costs, will want to play in this integrated sandbox.
This approach gives one definition of engineering parts and bills of material (BOM) throughout the supply chain and one common change process, providing visibility for all stakeholders and standardizing change management. For suppliers, immediate access and sharing information accelerates product development and increases simulation ability for evaluating materials’ performance, reliability, and safety before committing to physical prototypes.
Digitalization enhances modeling production and distribution processes, providing visibility, control, and synchronization across manufacturing operations and global supply chain processes. Small issues deep in the supply chain can disrupt the flow of parts and materials. With an integrated platform, it’s possible to see how various supply chain players relate to each other, and how changes in one impact another. For example, if a Tier 2 supplier is experiencing a labor disruption or a delay in material procurement, the Tier 1 can see it and learn how it affects its own production schedule and how to find a solution.
Solution
For aerospace suppliers to survive, they can no longer exist on their own. Each company is a partner in the network, collaborating and sharing to meet customer requirements, reduce costs, and have the flexibility to respond to changing conditions. Suppliers must provide better visibility into their operations and work seamlessly as an extension of the OEM. Digitalization of information and participation in a common platform can help suppliers accomplish this and benefit themselves through streamlined processes, better alignment with OEMs, and improved performance and responsiveness.
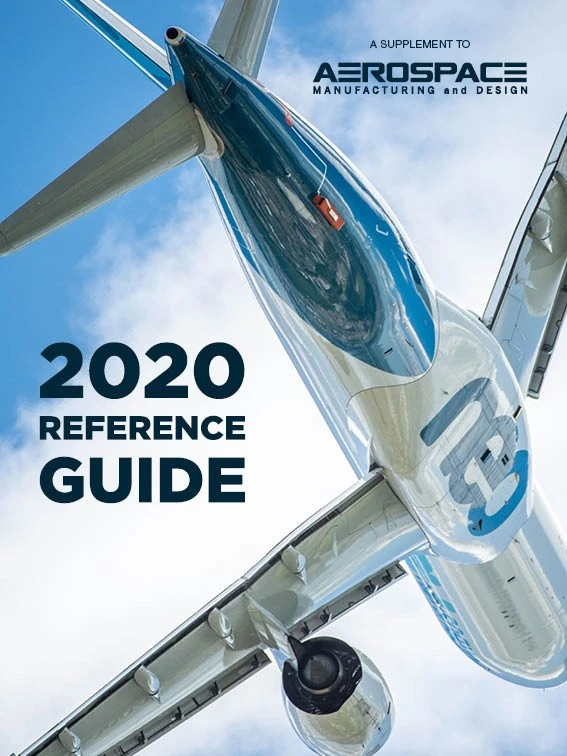
Explore the AMD Reference Guide 2020 Issue
Check out more from this issue and find your next story to read.
Latest from Aerospace Manufacturing and Design
- Revitalizing the Defense Maritime Industrial Base with Blue Forge Alliance
- Safran Defense & Space opens US defense HQ
- Two miniature absolute encoders join US Digital’s lineup
- Lockheed Martin completes Orion for Artemis II
- Cylinder CMMs for complex symmetrical workpieces
- University of Oklahoma research fuels UAS development
- Motorized vision measuring system
- Everyone's talking tariffs