

Selecting the appropriate grinding wheel for CNC tool grinding involves considering multiple factors to ensure optimal performance.
Basically, there are three types of bonds for super-abrasive wheels: resin bond, metal bond, and polyamide bond (plastic bond). The most successful high-performance wheels for carbide grinding are made with a hybrid bond including resin and metal.
Throughout the years, grinding wheel manufacturers have refined the ingredients and manufacturing processes. The most successful manufacturers collaborate with large grinding companies to develop and enhance wheel performance, learning from users’ experiences.
In production grinding of solid carbide endmills, two critical operations where wheel selection is vital for maintaining consistent tool geometries and extending lights-out operation are flute grinding and gash grinding. This also applies to high-performance drills in many ways.
Flute grinding involves the most substantial stock removal in producing carbide endmills, followed by gash grinding. Flute grinding requires wear resistance, whereas gash grinding demands effective stock removal and excellent edge and form retention to maintain the correct and consistent endmill end-geometry.
A high-performance diamond fluting wheel possesses more free-cutting characteristics and is more self-dressing, providing higher material removal with less need for truing. Truing involves removing the wheel from the machine and placing it into a wheel dressing machine, a manual and labor-intensive procedure similar to a new setup. The truing process removes the bond between the abrasive grits, so worn crystals can fall out. It also brings the wheel back to its original shape. The less frequently truing is necessary, the lower the overall production cost will be.
I use a simple cost calculator to demonstrate the annual savings from reduced setup times. Calculations show the impact of increased wheel costs compared to longer production times (less frequent truing). By purchasing higher-value diamond wheels which increases wheel pack costs by 20%, and assuming a 25% decrease in wheel dress frequency, production increases by 3.21% per year and the cost per tool decreases by 3.14%.
Assuming a total cycle time reduction of 30 seconds per tool (from 7 min to 6.5 min cycle time) due to the higher performance (increased feed rates) of the fluting and gashing wheels, production increases by 10.06%. Based on a cost-per-piece of $11.50 (including wheel costs), the total annual savings are $43,055.00. These calculations are based on an hourly shop rate of $80.00 and include assumptions about setup time and uptime, among other factors.
This analysis is based on producing the same endmill continuously 24/7 for an entire year. Every tool manufacturer produces various endmills on the same machine; however, this still highlights the benefit of investigating and testing new-generation diamond wheels with an open mind. Testing new wheels should be integrated into the continuous improvement process for every tool manufacturer.
MyGrinding Inc.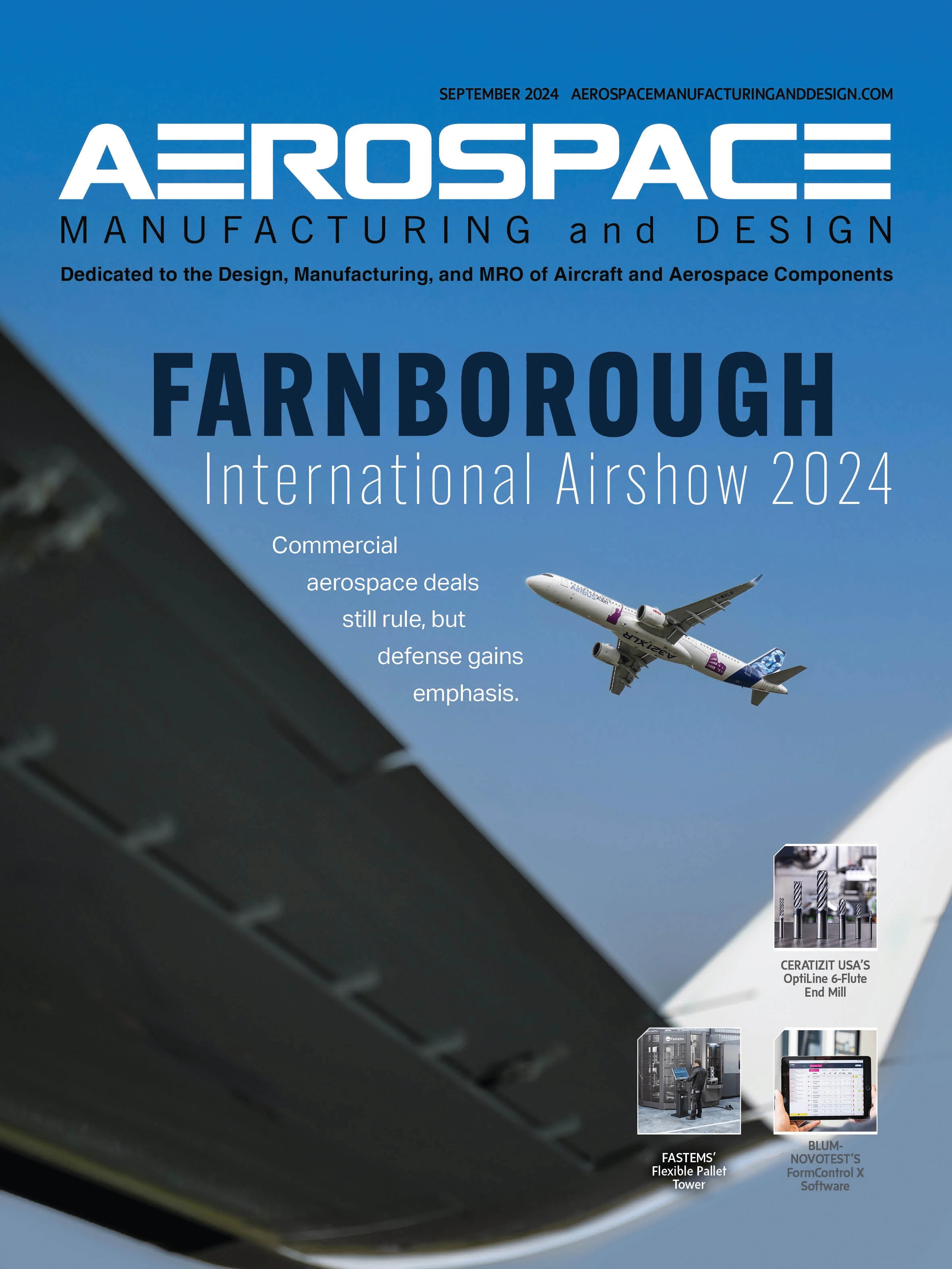
Explore the September 2024 Issue
Check out more from this issue and find your next story to read.
Latest from Aerospace Manufacturing and Design
- Revitalizing the Defense Maritime Industrial Base with Blue Forge Alliance
- Safran Defense & Space opens US defense HQ
- Two miniature absolute encoders join US Digital’s lineup
- Lockheed Martin completes Orion for Artemis II
- Cylinder CMMs for complex symmetrical workpieces
- University of Oklahoma research fuels UAS development
- Motorized vision measuring system
- Everyone's talking tariffs