
Broken tools can waste time and increase scrap amount – so breakages must be detected immediately.
Previous solutions to rapidly detect tool breakage involved laser-based detectors or touch probes contacting the tool. Laser-based detectors can be contaminated by coolant liquids or dust obstructing the laser beam. Unless the detector is cleaned regularly using compressed air, its accuracy can be reduced – registering false positives when a tool isn’t broken, or not registering a broken tool. The need for compressed air requires routing piping and replacing air filters.
Laser-based detectors require initial calibration for measuring tool geometry and need special control system programs to decrease tool rotation speed, slowing the machining process.
Contact-based, or tactile, breakage detectors risk breaking or damaging small tools.
Not using a tool breakage detector is a false economy, as it’s expensive to rework a job if a hole has been missed due to a broken or damaged tool, or worse, the workpiece may be damaged.

Heidenhain’s contact-free TD 110 tool breakage detector uses electromagnetic induction to sense tools made of HSS steel and carbide moving within a magnetic field generated by the electric current flowing within the detector.
The TD 110 can determine whether a tool still has a cutting edge of more than 2mm as it passes within a machine tool without slowing the machining process. The TD 110 can detect tools as they pass, spinning at regular speed. Tools down to 400µm can be detected without breaking the tool. There’s no need for extra programs in the system, so operation is faster.
Measuring approximately 71mm x 40mm x 24mm, the TD 110 retrofits existing machines and is flexible where it can be positioned, such as placed within the machine’s work envelope where it’s easily reached during a tool change. The unit is up to 6 seconds faster per tool change than laser-based systems (for 5-axis CNC; a 3+2-axis CNC would save 3 seconds) and can reduce idle time further when combined with Heidenhain TNC7 process monitoring.
Installation doesn’t require calibration or piping to run compressed air for cleaning – a single cable connects the detector. The TD 110 is universally retrofittable, due to its standard interfaces for tool touch probes.
The detector is maintenance-free and doesn’t require regular cleaning. Rated IP68, it’s usable in dirty or dusty environments and in the presence of cooling lubricant.
The breakage sensor can generate a floating or an HTL switching signal to connect to a Heidenhain TNC control, a PLC, or I/Os of other CNC controls. The machine control can evaluate signals via standard instruction sets to stop a cycle or alert an operator. An LED signals a broken tool.
Heidenhain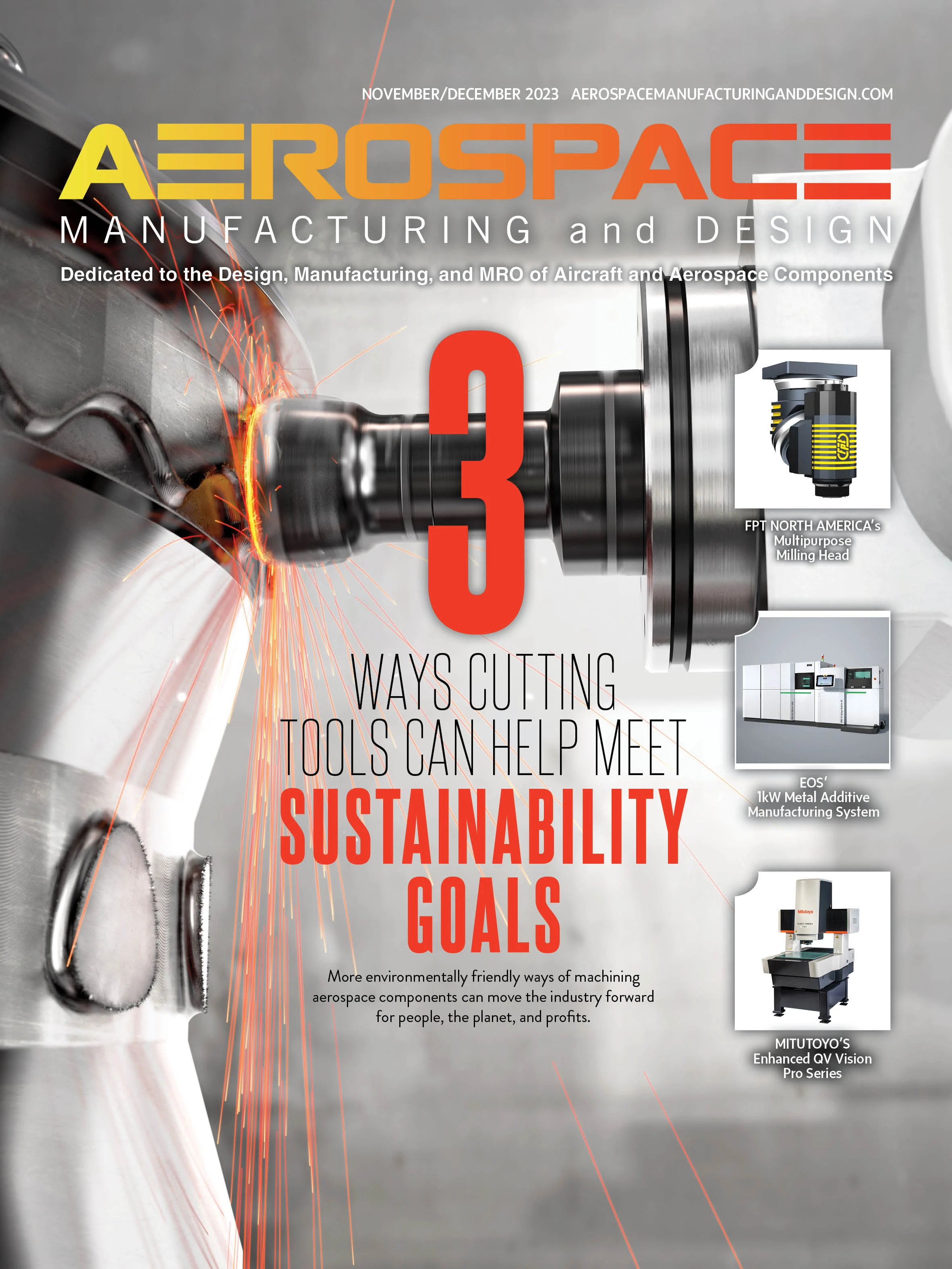
Explore the November December 2023 Issue
Check out more from this issue and find your next story to read.
Latest from Aerospace Manufacturing and Design
- Piper Aircraft receives its largest ever domestic trainer order
- Miniature, high force-to-size linear voice coil servo motor
- MagniX, Robinson to develop battery electric R66 helicopter
- Zero-point clamping modules
- Hartzell electric engine propeller earns FAA approval for AAM
- Thin profile flame and thermal barrier
- Guill Labs offer materials and extrusion testing
- High production vertical honing systems