

It’s now possible to increase productivity and tool life in HRSA and titanium machining. At a critical time in aerospace machining, PrimeTurning™ is a new methodology delivering outstanding results in ISO S applications.
1. What exactly is the PrimeTurning methodology and what does this innovation mean for conventional turning?Our PrimeTurning method gives you the ability to turn in four separate directions with one insert, one tool holder. This all-directional turning is unlike any other turning concept available today. Beyond the ability to go multidirectional with just one tool, PrimeTurning differentiates itself compared to conventional turning because its performance enables you to engage high feed turning or chip thinning. The result is increased levels of productivity, as well as often achieving longer tool life.
2. Why are aerospace manufacturers seeing increases in productivity with PrimeTurning?
When dealing with heat-resistant super alloys (HRSA) materials, one of the largest enemies of tool life is notch wear. PrimeTurning methodology is unique in that it allows using one tool to create sharp 90° angles when programmed properly and to spread wear along more of the carbide. Ultimately, it increases feed rate which helps increase productivity. A critical part of PrimeTurning's success in aerospace is the new S205 HRSA turning grade. Second generation CoroTurn® Prime B-type inserts in combination with grade S205 are an extraordinary combination for aerospace operations.
3. What are you hearing from customers using PrimeTurning?With a properly implemented PrimeTurning application, I’m hearing customers experience between 18% to 35% productivity increases and significant tool life gains, depending on the grade they’re using and how they’re roughing the material. When properly used, it reduces cycle times up to 30%. This enables shops to increase the productivity of 1 machine into perhaps 1.3 machines.
4. What is the best way to implement PrimeTurning and secure maximum output?
The key is to plan accordingly and work with your Sandvik Coromant local sales rep, application specialist, and aerospace specialist. In addition, we offer support through our CAM partners or customers can use our CoroPlus® ToolPath for PrimeTurning software which generates optimized CNC code for smooth implementation of the PrimeTurning method and CoroTurn Prime tools in turning applications. It’s a team effort: assisting customers in taking full advantage of the system and the application and then supporting them as necessary.
5. When should shops consider upgrading conventional turning operations to PrimeTurning?Customers wanting to reduce cycle times from 18% to 35% should consider the efficient PrimeTurning solution to maximize profits and income. PrimeTurning shines in intermediate- to final-stage machining but can be considered at all stages of turning. PrimeTurning excels in turning operations with 1/2" IC inserts on a lathe. With the release of second generation CoroTurn Prime B-type inserts, consider PrimeTurning first.
Learn more about PrimeTurning
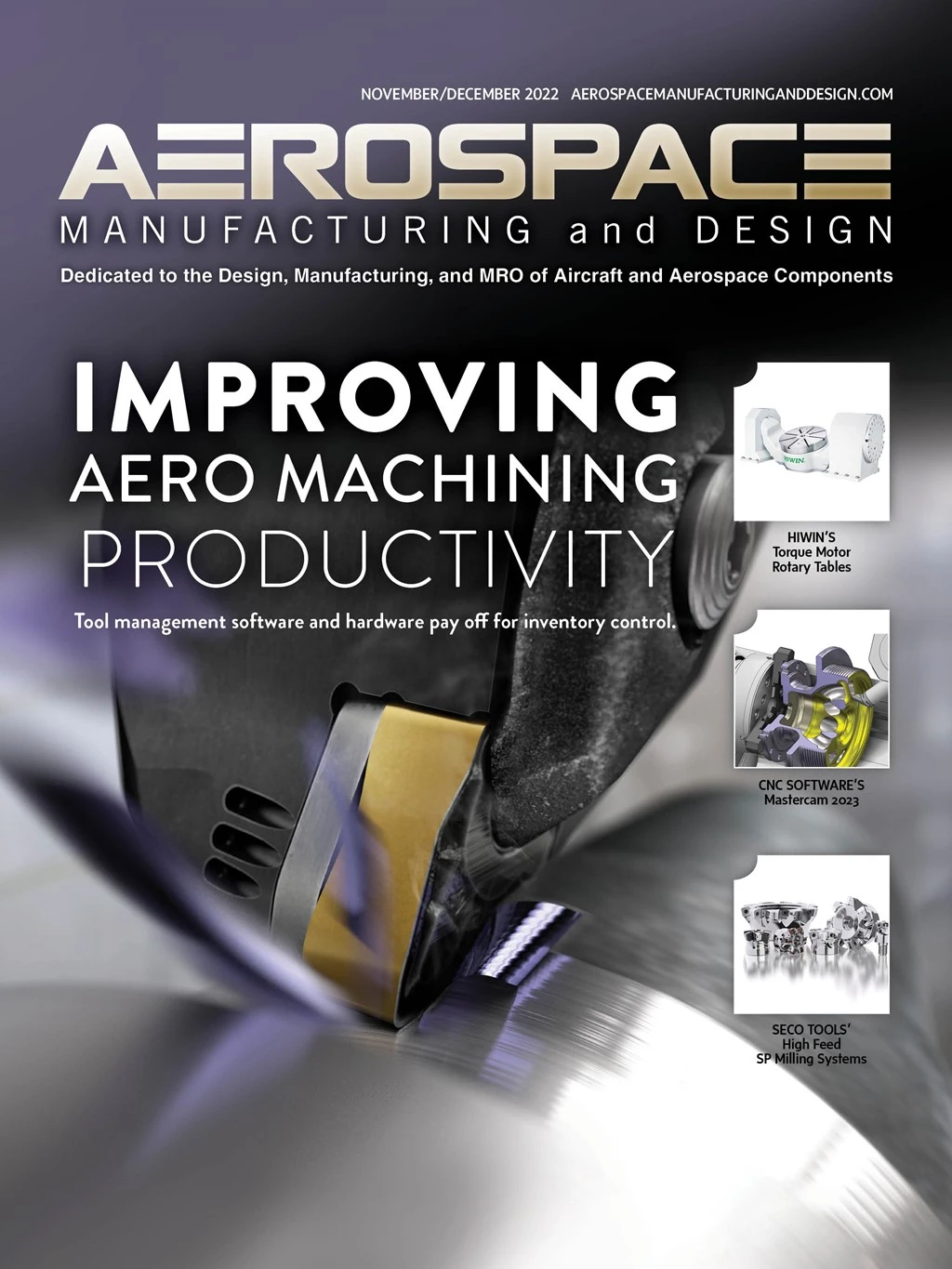
Explore the November December 2022 Issue
Check out more from this issue and find your next story to read.
Latest from Aerospace Manufacturing and Design
- Revitalizing the Defense Maritime Industrial Base with Blue Forge Alliance
- Safran Defense & Space opens US defense HQ
- Two miniature absolute encoders join US Digital’s lineup
- Lockheed Martin completes Orion for Artemis II
- Cylinder CMMs for complex symmetrical workpieces
- University of Oklahoma research fuels UAS development
- Motorized vision measuring system
- Everyone's talking tariffs