
Neutron imaging, a powerful nondestructive testing (NDT) method, can see through complex materials and catch flaws and defects that would otherwise go unnoticed, such as cracks and voids in energetic materials, ceramic remnants in turbine blades, and structural weaknesses in composites and 3D-printed components.
How it works
Neutron radiography (N-ray) uses a stream of neutron radiation to visualize an object’s internal structure. Similar to X-ray imaging, neutron radiation behaves differently from X-rays, producing images with new, valuable details.
X-rays can pass through light materials more easily than dense ones. The more electrons an element has, the more energy an X-ray needs to pass through it, and heavier atoms have much larger and more populated electron clouds, making them more opaque. Neutron radiation only interacts with the atomic nucleus, ignoring those sometimes dense electron clouds. Generally, it’s difficult for neutron radiation to penetrate through lighter materials because there is less space between the atomic nuclei for the radiation to pass through. Therefore, neutron radiation penetrates dense materials more easily than light materials.
There are many items used in aerospace, such as turbine blades, energetic devices, and composite materials, for which neutron imaging can provide more insight than other nondestructive testing methods.
Turbine blades
Cast from lightweight metal around ceramic cores, turbine blades have hollow air-cooling channels running through them to prevent them from breaking or melting in a jet engine’s high-temperature operating environment. In manufacturing, small amounts of ceramic can get trapped in the cooling channels, impeding airflow. Since failure of a single blade can prove disastrous for a jet engine, manufacturers trust a rigorous quality assurance (QA) process to identify any blades with this dangerous flaw.
Neutron radiation interacts in interesting ways with certain elements, such as gadolinium and boron. These elements are neutron absorbers, as their physical properties render them effectively opaque to neutron radiation. Soaking a turbine blade in a liquid gadolinium solution to tag it allows the gadolinium to settle into porous ceramic fragments but not the blade’s metal structure. So, when taking a neutron image of the tagged blade, even the smallest bits of ceramic will appear in stark contrast to their surroundings.
Neutron radiography is such a critical nondestructive testing method for turbine blade manufacturers that manufacturing output depends on the availability of neutron imaging facilities. Many neutron imaging facilities are fission reactors maintained by public universities and often have planned maintenance shutdowns coinciding with university schedules, straining supply. If neutron sources are unavailable, it impacts the entire turbine blade supply chain.

Energetic devices
Energetic devices (explosives) power the ejection mechanism in fighter planes, for example, using a series of tiny explosive charges that fire in order to blow off the plane’s canopy and eject the pilot. In rockets that send satellites into orbit, similar explosive charges in the payload fairing separation system allow release of the payload.
Energetic devices also enable explosive signal transfer systems, which are useful for high-radiation environments where traditional circuitry can damage easily. A single energetic device misfire can spell the difference between success and a messy failure. However, they are difficult to inspect for flaws with most forms of NDT, since these devices consist of a dense outer shell encasing a payload of lighter energetic material.
The energetic material within these devices tends to be a solid, hydrogen-rich chemical compound. Physical flaws, such as voids, cracks, gaps, and bubbles, can denote breakdowns in the chemical composition that can lead to misfires. Hydrogen’s high neutron cross-section makes energetic compounds more opaque to neutron radiation; unlike X-rays, then, neutron radiation can pass through the device’s dense outer shell without passing through the energetic material.
3D-printed composites
As 3D printing technology advances, additive manufacturing is quickly becoming essential for aerospace manufacturers due to its ability to construct complex designs more efficiently and with less waste than traditional subtractive methods. 3D printing technology allows aerospace manufacturers to quickly design and test prototypes of new components and composite materials.
Composites combine two or more substances in order to imbue the resulting material with the advantages of both (for example, strength from one substance and flexibility from another). However, they can be frustrating to inspect nondestructively. One component substance of the composite material may X-ray well, while another may not, making it difficult to get the full picture with just one testing method.
This is where neutron radiography complements X-rays. Applied together, both can give two halves of the whole picture. N-rays are especially useful for boron composite materials due to boron’s high neutron cross-section.
Composite materials are an especially exciting matter for aerospace manufacturers, as they can be used to create lighter, stronger, and more environmentally friendly components for aircraft and spacecraft. As composites use increases, new opportunities for NDT methods such as neutron imaging will present themselves in product testing and design, QA, and failure analysis.

Improving N-ray access
Although neutron imaging provides great NDT insight in aerospace, outside of turbine blade manufacturers, it’s not often used due to long-standing accessibility issues. Until recently, only a handful of nuclear fission research reactors could provide enough neutron output to create clear and detailed neutron images for industrial NDT. Neutron imaging has been underused for inspecting devices such as ejection and payload fairing separation mechanisms since most facilities are not equipped to handle energetic material.
However, new neutron imaging facilities are emerging with significant advantages compared to aging and dwindling reactor facilities that can provide equivalent image quality with a smaller footprint, fewer regulatory burdens, and fewer safety risks. Since its emergence as a viable industrial NDT method in the 1950s, neutron imaging has had a long history of critical use within the aerospace industry, and as newer, more accessible facilities emerge, its usefulness as a tool for research and development, quality assurance, and failure analysis will increase.
Phoenix LLC
https://phoenixwi.com
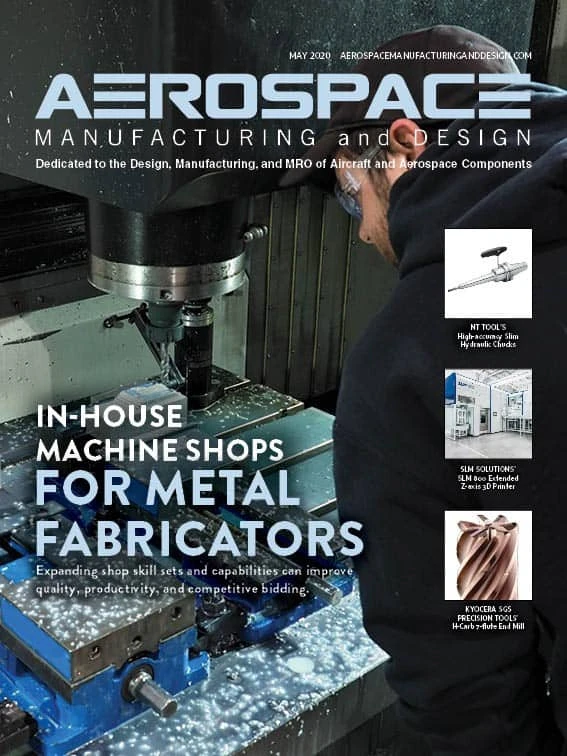
Explore the May 2020 Issue
Check out more from this issue and find your next story to read.
Latest from Aerospace Manufacturing and Design
- Titanium drop bottom furnace installation underway
- Solid carbide taps for demanding materials
- The Partner Companies acquires Precision Eforming
- Hall Effect angle sensors
- July is for learning – so drop in for this month’s second Manufacturing Lunch + Learn
- Essential strategies to protect your data
- NASA selects instruments for Artemis lunar terrain vehicle
- Twin-cutter boring head