
The U.S. needs a national aerospace strategy created by the government, private industry, and labor unions to maintain its standing as a world leader in the high-tech and high-skilled aerospace industry. That’s the call to action found in the latest report from the International Association of Machinists and Aerospace Workers (IAMAW), North America’s largest aerospace labor union. The 28-page report, “Rising Potential: An IAMAW Proposal for a U.S. Aerospace Strategy” offers a benchmark of the current successes and challenges facing the aerospace and defense (A&D) industry.
IAM Int’l President Robert Martinez Jr. and IAM Aerospace General Vice President Mark Blondin advocate for strong unions, buying American, and stricter regulation of offsets that transfer technology to global competitors. While the IAMAW and A&D corporate management will likely disagree on several points, the report’s executive summary highlights a concern on which both parties should agree: the imminent skills gap that threatens to create a shortage of trained A&D workers. IAMAW leadership calls for investment in quality registered apprentice and training programs to save these essential jobs.
As the industry’s technology is constantly evolving, it’s essential for the workforce “to adapt and meet the new challenges of a global economy through reskilling.” Yet, while reskilling is a top concern, only 34% of employees in the industry said they participated in learning and development programs. That’s not enough.
IAMAW aims to establish a uniform registered apprenticeship and training system in which future apprentices are carefully selected and properly trained in all the industry’s mechanical and theoretical aspects.
The IAMAW-Boeing Joint Apprenticeship Program in Washington’s Puget Sound area is one example cited as an effective training program to develop a highly skilled workforce. Boeing offers 10 apprenticeship programs of four or five years in duration, requiring 160 unpaid classroom hours per year. Qualified journeyman workers teach students through a combination of real-world and on-the-job training that meets the Standards of Apprenticeship approved by IAMAW, Boeing, and the Washington State Apprenticeship and Training Council.
But there’s more to do. A 2019 survey of large IAMAW-represented aerospace locations indicates only 10 of the 75 respondents have strong apprenticeship programs. Of the remainder, six have apprenticeship programs but lack participation. Twenty-seven of the remaining 59 employers agree with the need for apprenticeship programs but lack resources to implement them.
To help fund such programs, IAMAW calls for a coordinated effort between government, private business, universities, and labor unions to move the industry forward. “Without a comprehensive aerospace sector plan going forward, the industry will lose jobs and its foothold as world leaders, even as other countries prioritize their own aerospace industries,” the report warns.
Such programs shouldn’t focus solely on original equipment manufacturers (OEMs) and Tier 1 suppliers. They must also include smaller and mid-size companies in the A&D supply chain. – Eric
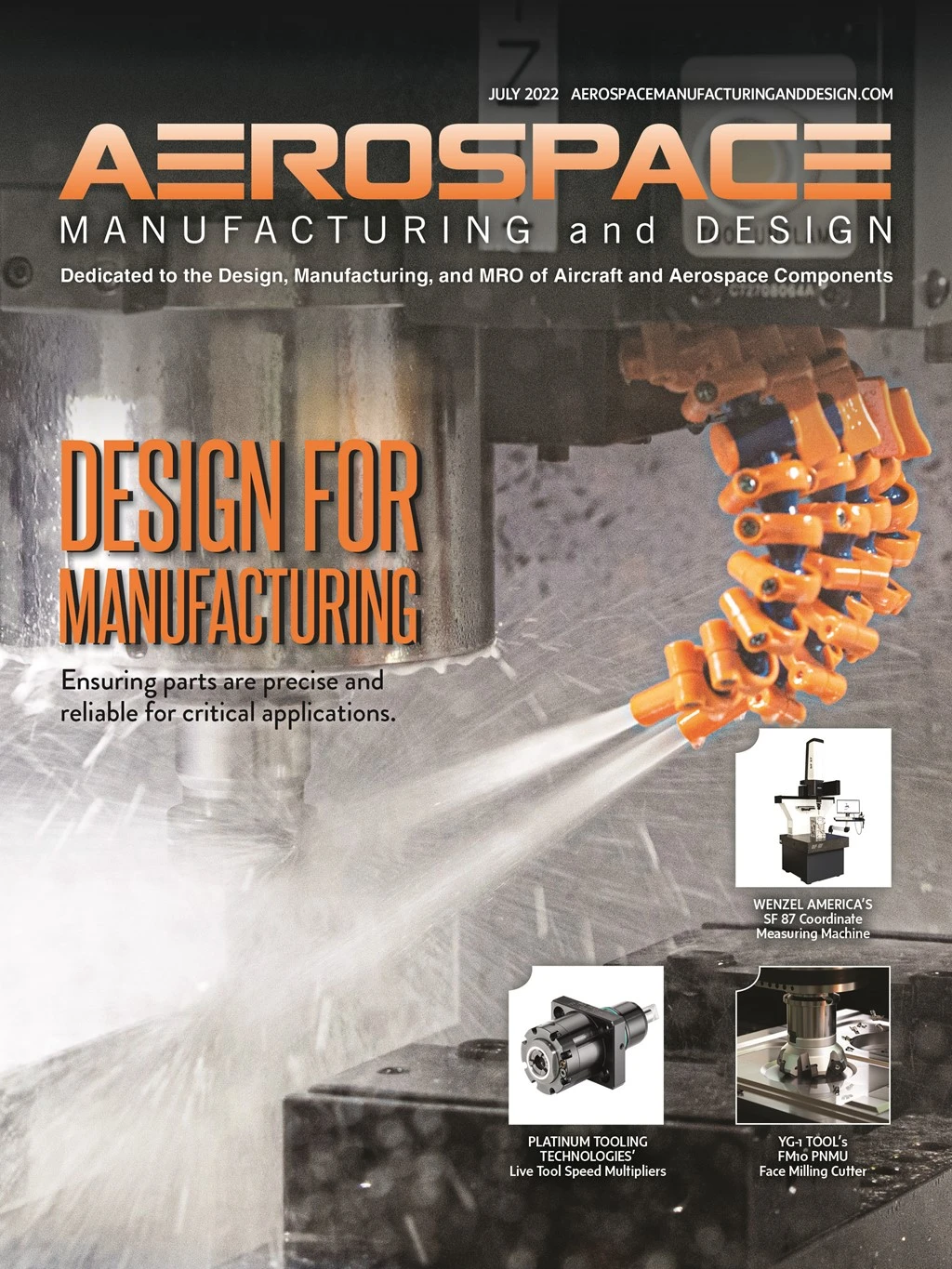
Explore the July 2022 Issue
Check out more from this issue and find your next story to read.
Latest from Aerospace Manufacturing and Design
- Boeing to build US Air Force’s sixth-generation fighter jet
- Sandvik Coromant introduces CoroMill Plura barrel
- #54 - Manufacturing Matters - HMI Solutions for EV Industry from EAO
- Aerospace Industry Outlook returns for spring 2025
- Drop in for an interactive webinar on automation in manufacturing
- SW’s wing rib technology for the aerospace industry
- Mach Industries launches Mach Propulsion
- Murata Machinery USA's MT1065EX twin-spindle CNC turning center