
Shape memory alloys (SMAs), metals that can alter their original shape in response to stimuli such as temperature, have been around since the early 1930s and used in the biomedical industry since the early 1990s.
In aerospace, SMAs could offer actuation – such as a wing aileron or deploying a Mars rover solar panel – where their light weight, silent operation, and compact form are desirable.
Dr. Othmane Benafan, a materials research engineer at NASA’s Glenn Research Center in Cleveland, Ohio, and shape memory alloys team leader, says, “By changing temperature to these metals, you can have them push and pull things to do work. The heat that drives them can come from electrical resistance, can be harvested from engine exhaust heat, or just from passive temperature changes in the environment, which can come from an airplane’s take-off to cruise altitude or from a spacecraft’s hot launch to cold orbital conditions in space.”
SMAs start with equal parts nickel and titanium, with 10% to 25% replaced with elements such as palladium, platinum, gold, hafnium, or zirconium to produce a range of shape memory activation temperatures from -150°C to 500°C. Hafnium and zirconium are readily available and inexpensive, which creates the potential to commercialize aerospace-fit SMAs.
SMAs
“The difference in SMAs is they go from one solid phase to another. The material’s crystal structure is moving and changing shape, and the atomic-level rearrangements are reversible and can be formulated to remember a shape,” Benafan explains.
Superelasticity – mechanical loads – can also induce the alloy’s shape memory. An example is bendable metal eyeglass frames.
“Imagine you have a body that can deform heavily and return to shape when the load is removed – sort of a rubber band, but in metal,” Benafan says. “This structural property is useful for designing structures that undergo large deformation. SMAs provide an order of magnitude more deformation recovery than conventional metals like aluminum or steel.”

Repeatable, predictable
Shape memory actuators have been used in space since the 1980s, and NASA’s Mars Pathfinder Sojourner Rover has them. In most cases, they are used for a one-time antenna or cargo deployment, pin-pullers, or other
Most
Another challenge with SMAs is that their functionality can degrade with increasing time and number of completed cycles. Plus, materials for SMAs often can’t be procured from a vendor without some costly customization. These challenges help explain why SMAs have not made their way onto commercial aircraft.
Progress
The shape memory alloy team at NASA Glenn is tackling some of these challenges. For more than a decade, the team has been creating new alloys, testing infrastructure, and modeling tools. The alloys developed at NASA have expanded SMAs temperature range to nearly 500°C.
Benafan emphasizes, “The materials we develop are scalable to hundreds of pounds with a direct path to even bigger batches. NASA has produced many patents in this area and worked with industry partners to transfer the knowledge related to the alloys’ chemistry and processing. We all want to see better and more efficient aircraft, and that can only happen if the material is available in abundance commercially.”
The NASA Glenn team has created process-finished SMA rods 1" in diameter up to 10ft long, starting with 8", 150-lb ingots. One application is a torque tube that can be used for rotary motion. When heated, it twists to drive a wing flap.

The angle output (twist) is a function of length and diameter. A 0.5" tube, 1ft long can give 100° of twist. Torque is a function of diameter, not length. Where SMAs have been limited to below 300 in-lb, NASA Glenn engineers can now make tubes that produce 15,000 in-lb of torque.
Large actuators with the right temperatures and strength are now feasible, in addition to smaller forms, such as wires, cables, tubes, or springs that can be derived from the 1" round stock. For wires and tubes, the SMA serves as sensor and actuator.
SMAs offer at least three advantages for use on aircraft, one being weight savings.
“They’re smaller than hydraulic or pneumatic systems. They can deliver large force in a tiny package – a huge benefit,” Benafan says. “They have a smaller footprint, so they can be put into smaller spaces, nearer wing edges.”
SMAs also reduce part count – fewer pumps, gears, fluids, and seals. As the part count goes down, there are fewer parts to fail.
“They also offer silent actuation where that is desirable,” Benafan adds.
SMAs are tunable to different temperatures, depending on
These modern SMAs do not yet exist outside of NASA labs.
“No one has proved to the Federal Aviation Administration (FAA) that they’re ready to go on aircraft. Also, people would like to see fatigue and durability to millions of cycles. We’re still working on it,” Benafan admits.
Next step: certification
NASA Glenn’s SMA team intends to see its technology blossom in aerospace, which means certification and standards are necessary. NASA has joined an international team led by aerospace companies, government agencies, and universities under the Aerospace Vehicle Systems Institute (AVSI) to develop the first-ever FAA-accepted material specification and test standards related to SMA actuation for commercial aviation. The team has drafted two standards that are under review by standards development organizations.
“Fatigue of these materials is mostly unknown, system integration is a whole new beast, and new applications still favor conventional, trusted methods. It certainly requires a new way of thinking and new paradigm shift,” Benafan says. “The community outside of shape memory doesn’t know that metals can move. We hope to make engineers and designers aware of

Toward this end, the team is also working on material selection tables – a look-up database of
“It is exciting to see all the pieces come together, but that doesn’t mean we are done,” says Glen Bigelow, a materials engineer. “The path ahead is toward real applications.”
SMAs offer a solution for future morphing- or adaptable-wing concepts, or just better and more efficient aircraft.
NASA engineers have made measurable progress in developing SMAs – in advancing the art, generating publications and patents, engaging industry partners, and spreading the knowledge via mentoring students and Ph.D. dissertations.
“We want to see SMAs in many aeronautics and space applications,” Benafan says. “It is just a matter of time, a matter of persistence, and a matter of continuing some really cool science.”
NASA Glenn Research Centerwww.nasa.gov/centers/glenn
SMA fundamental research is funded by NASA’s Transformational Tools and Technologies (TTT) project under the Aeronautics Research Mission Directorate.
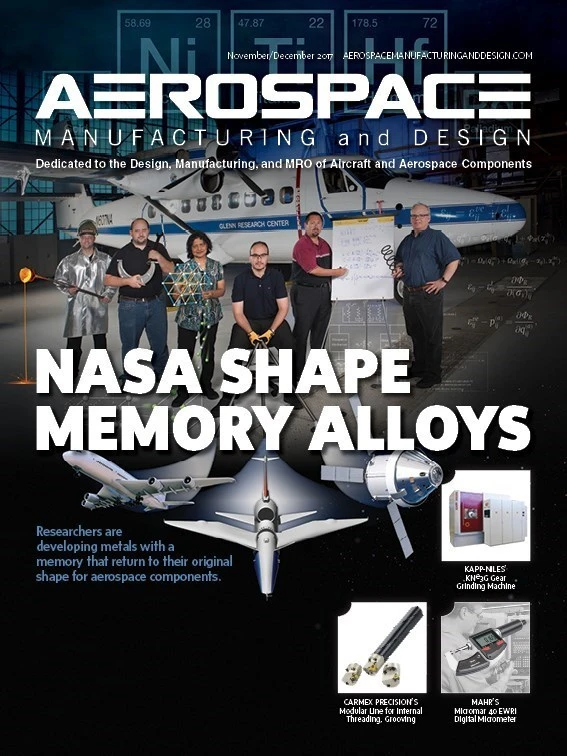
Explore the November December 2017 Issue
Check out more from this issue and find your next story to read.
Latest from Aerospace Manufacturing and Design
- Revitalizing the Defense Maritime Industrial Base with Blue Forge Alliance
- Safran Defense & Space opens US defense HQ
- Two miniature absolute encoders join US Digital’s lineup
- Lockheed Martin completes Orion for Artemis II
- Cylinder CMMs for complex symmetrical workpieces
- University of Oklahoma research fuels UAS development
- Motorized vision measuring system
- Everyone's talking tariffs