
At the beginning of 2018, MTU Aero Engines set up a department in Munich, Germany, headed by Dr. Jürgen Kraus to advance additive manufacturing (AM) technology.
A team of design engineers, structural mechanics engineers, process specialists, and operations scheduling experts investigate conceptual designs of applications and constructions from a bionics viewpoint, develop production technology, and industrialize the entire process chain.
Since 2013, MTU has used selective laser melting (SLM) for production of borescope bosses for the PurePower PW1100G-JM geared turbofan engine powering the Airbus A320neo.
As part of Clean Sky, the largest technology initiative launched in Europe, MTU is working on a seal carrier manufactured using additive processes. The inner ring with an integral honeycomb structure will be installed in the high-pressure compressor and contribute to improving clearance control, increasing efficiency. Bearing housings, brackets, and struts will follow. Other aims are to further enhance the process monitoring system and improve the surface finish. www.mtu.de

CO2 snow cleaning
The ADDvance Cryoclean system uses CO2 snow particles and a blasting abrasive to remove surface oxides, unfused powders, and residues from 3D-printed parts.
It produces CO2 snow on-demand by feeding liquid CO2 into a cleaning chamber, making it environmentally-friendly and cost-effective.
Since the Cryoclean system does not require the use of water or other solvents, there is no moisture to corrode metals, no need for drying, and no wastewater. It can be used as a manual system or as an automated cleaning solution. www.linde.com
Oerlikon, IABG accelerate AM component qualification
Oerlikon AM and European technology and science service provider IABG mbH are accelerating equipment and process certification and equipment testing for additive manufacturing (AM) components.
The partnership allows European manufacturers to provide AM-qualified components to customers, produced through certified processes that have been developed through the partnership. Cutting-edge qualification, inspection, and testing methods for AM could essentially become new standards in additive manufacturing. The joint research and development of procedures and methods will push forward AM industrialization. www.iabg.de; www.oerlikon.com
Boeing, Assembrix collaborate on secure 3D printing methods
Boeing will use Israeli-based Assembrix Ltd.’s software to manage and protect intellectual property shared with vendors during design and manufacturing.
Assembrix's software will enable Boeing to transmit additive manufacturing (AM) design information using secure distribution methods to protect data from being intercepted, corrupted, or decrypted throughout distribution and manufacturing. www.assembrix.com; www.boeing.com

Additive manufacturing guide
Renishaw has launched its additive manufacturing (AM) page to educate and inform customers and the wider engineering community
Content includes videos, feature articles, industry news, opinion pieces, and case studies of successful AM applications. It also contains a collection of technical articles written by Renishaw’s industry experts, including AM LinkedIn bloggers Marc Saunders and Lucy Grainger, experts in metal powders for AM.
The beginner’s guide to AM explains how to optimize metal AM use to take advantage of the design freedom, performance, and efficiency of this manufacturing technique. It also explains how understanding the AM process characteristics are essential to reduce waste and cost. www.renishaw.com

3D metal printer
Bulk to Shape Transformation (BTS) technology advances 3D laser metal printing, making existing basic processes more robust and predictable.
Optimizing the system configuration improves cost performance up to 3x by using application-specific approaches for quick prototyping, engineering, validation, and instant market checks.
In most cases, it represents the fastest path to manufacturing readiness level (MRL) 10. www.laserphotonics.com

3D printing simulation
High-performance KetaSpire PEEK AM filament will be the first polyetheretherketone polymer included in e-Xstream engineering’s Digimat simulation software.
Part of Digimat 2018.1, Digimat for additive manufacturing (AM) will enable designers and engineers to accurately predict warpage and residual stresses of 3D-printed KetaSpire PEEK parts as a function of AM processes, such as fused filament fabrication (FFF). With Digimat for AM, users can further optimize processes and minimize part deformation before printing parts.
KetaSpire PEEK AM filament offers superior mechanical strength and chemical resistance for 3D-printed parts, as well as applications that demand a higher level of end-part performance. www.solvayam.com
Rize launches One Black material

Get curated news on YOUR industry.
Enter your email to receive our newsletters.
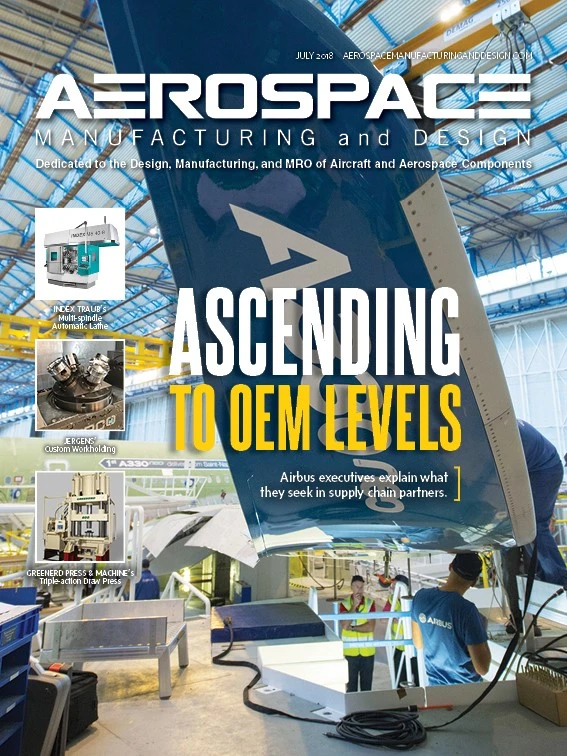
Explore the July 2018 Issue
Check out more from this issue and find your next story to read.
Latest from Aerospace Manufacturing and Design
- March Manufacturing Lunch + Learn with Quell Corp.
- March Manufacturing Lunch + Learn with SMW Autoblok
- SwRI addresses critical aging aircraft issue
- Walter adds tools to its PCD milling cutter range
- Archer Aviation, Palantir partner on next-gen aviation
- Fairlane Products’ TG GripSerts and accessories for low-profile clamping
- Boeing to build US Air Force’s sixth-generation fighter jet
- Sandvik Coromant introduces CoroMill Plura barrel