
Prolonged economic challenges – pandemic, inflation, labor shortage, the supply chain – are fundamentally reshaping the way businesses operate. Which changes are likely to stay as businesses struggle to reach efficiencies? Aerospace Manufacturing & Design recently had the opportunity to ask Ben Johnston, COO of Kapitus, a direct lender and a network of lending partners that’s provided more than $3.6 billion in growth capital to more than 64,000 U.S.-based small businesses.
Despite recent job growth numbers, small businesses in the U.S. report that finding and keeping qualified employees remains one of their biggest challenges. How will inflation, supply chain, and other manufacturing challenges complicate hiring and retaining skilled workers?
“The manufacturing industry is feeling this shortage acutely and is experiencing significant wage inflation as employers are forced to increase compensation to attract qualified workers and compete with more flexible employment options,” Johnston says. “At the same time, supply chain issues can wreak havoc on both the manufacturer and its labor pool. If a lack of available parts forces a plant to temporarily close, the manufacturer has the unenviable choice of either paying idle employees or furloughing critical workers, thereby encouraging them to seek other employment.”
How long will this period of prolonged economic challenge last?
“Manufacturers continue to feel the impact of higher energy prices, supply chain disruptions, and wage inflation caused by nearly full U.S. employment. The war in Ukraine is likely to keep pressure on food and energy prices for the foreseeable future. Meanwhile, expanding COVID-19 lockdowns in China have the potential to further disrupt the global supply chain, driving up the cost of critical raw materials and finished goods for U.S. manufacturers.” Johnston explains, “Small businesses can expect continued inflationary pressure in the coming months.”
The news isn’t all negative, though. Johnston says, “Manufacturers can limit the impact of inflation by vertically integrating critical components of the manufacturing process they might otherwise have contracted out. Vertical integration can help control lead times and limit markups charged by third parties.”
Another suggestion: Manufacturers should consider partnering with other local manufacturers to purchase common materials in larger quantities. “Larger orders should command a better price and may be prioritized for fulfillment over smaller orders,” Johnston adds. “If a manufacturer is sourcing a critical component from China that could be made in-house, or by an onshore or nearshore partner with a more dependable supply chain, it may be worth the incremental expense to ensure timely delivery.”
How can small enterprises reduce, automate, streamline without negatively impacting their business?
“Investing in new equipment and software that eliminates material waste and non-essential human effort will be key,” Johnston replies. “Be sure to update your assumptions on equipment, labor, and financing as costs are changing rapidly. These costs will be offset by the benefit of more dependable production and lower shipping costs,” he asserts. Good advice, I say. – Eric
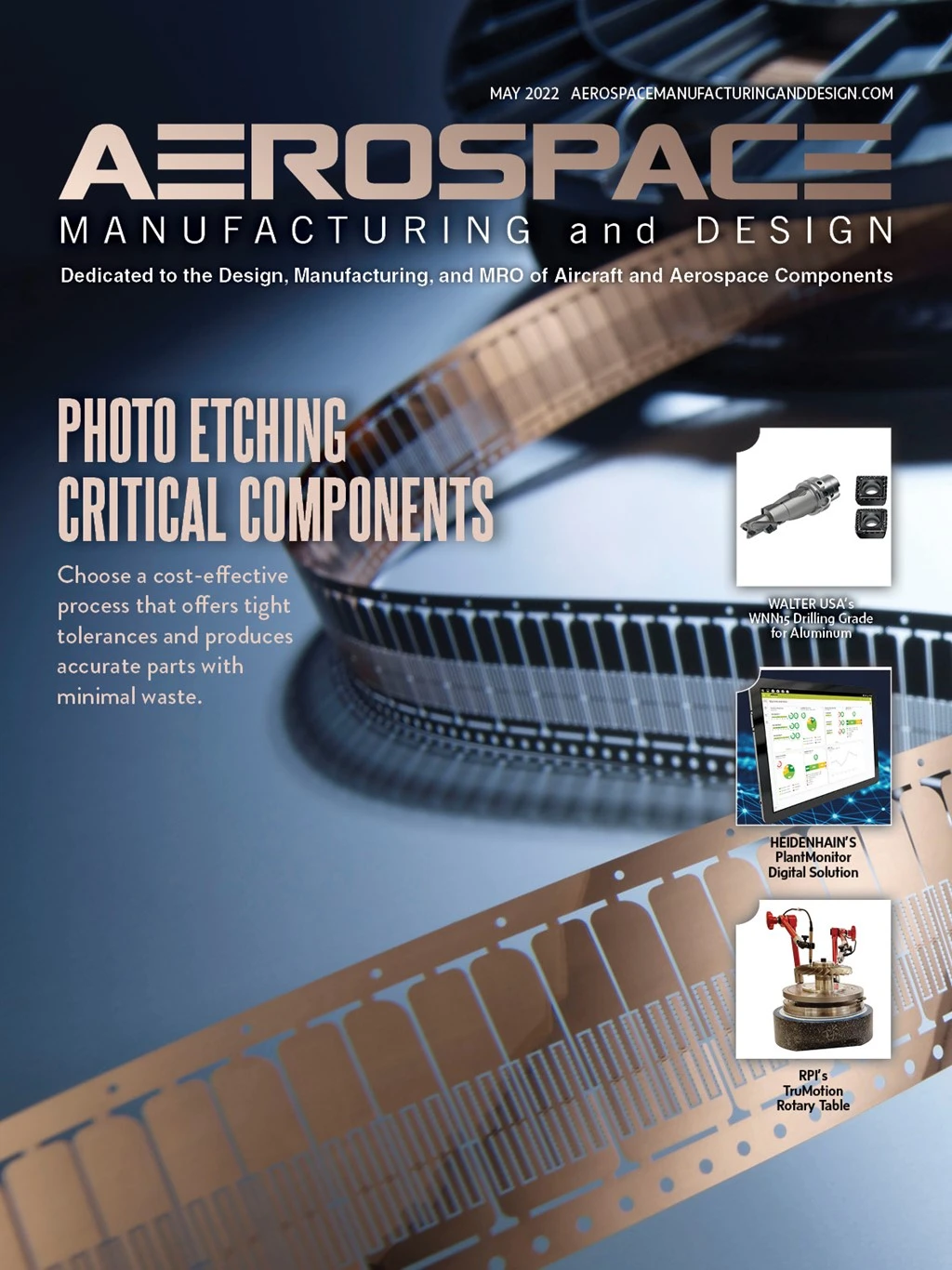
Explore the May 2022 Issue
Check out more from this issue and find your next story to read.
Latest from Aerospace Manufacturing and Design
- Piasecki acquires Kaman's KARGO UAV program
- PI Americas’ long-travel XY piezo nanopositioners-scanners
- AAMI project call submission deadline extended to May 12
- Jergens launches cast iron tooling column additions
- Airbus to acquire assets relating to its aircraft production from Spirit AeroSystems
- FANUC America's Cobot and Go web tool
- Chicago Innovation Days 2025: Shaping the future of manufacturing
- High-density DC/DC converters for mission-critical applications