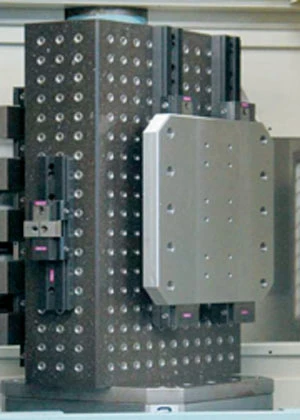
Through the use of flexible, multi-part clamping for complex parts, one job shop has successfully produced a 21-hour machining cycle, using only one manned shift. More significant, perhaps, the shop priced out the manufacture of three, 300 and 3,000 typical parts to China being machined in this new way and only the three-part order could be produced at a lower cost, without the shipping cost and time considered.
According to Triag, a workholding and fixturing manufacturer, solving complex part manufacturing requires three key elements.
Fixtures need to be flexible, modular and variable. By "flexible," it means the fixture must be suitable for various cutting conditions. It must also be adaptable to a wide assortment of materials, weights, sizes and configurations, whether for 3-, 4- or 5-axis machining center.
"Modular" means the design principle of the fixture must be such that it allows the clamping devices to move and be repositioned on the fixture faces in different setups, often within the same job run. This presupposes, of course, that the machining center has onboard controls sufficient to handle the staging of different jobs.
"Variable" means the fixture must adapt to the particular machining center characteristics of mounting, access to the cutting theater, and shuttling, with little or no modification.
The shop, Profiform AG, is located in the town of Adligenswil, near Lucerne in Switzerland. Opened in 1987, the shop began with vertical machining centers and simple clamping vises. In 1992, the investment was made in two- and six-pallet horizontal centers, equipped with multiple clamping systems. In 2002, the first FMS (flexible manufacturing system) was installed, allowing the first unmanned production to be accomplished. This resulted in immediate improvement in the overall shop productivity, as well as cost containment for the owners of this 13-man shop.
Currently, the heart of the shop's FMS is a Mazak PFH 5800 4-axis HMC, with XYZ movement of 730mm x 730mm x 740mm. A 16-pallet rack, equipped with Tripoxy tombstones up to 960mm high, and 378-position toolchanger are onboard this formidable workhorse.
In what the shop calls its "chaotic" clamp setup, complete subassemblies are partially removed, ready for final assembly. Single large part fixturing and/or the clamping of several small parts are done simultaneously. This chaotic clamping setup means constant change to the clamping location, which is performed by the Triag Powerclamp system. On more "organized" setup, the same part is clamped in all stations on the tombstone.
Typically, Profiform machines forged and cast parts, structurals, saw cuts, profiles and parts up to 400mm x 400mm x 50mm in materials ranging from aluminum, stainless and tool steels to various plastics and composites.
Profiform's requirements for their clamping system included process safety through rough milling, as well as the clamping of pressure-sensitive parts; maximum flexibility in terms of the clamping techniques employed; maximum clamp density for optimum space utilization; short setup times and ease of use. Triag responded with the modular Powerclamp design, consisting of a base rail, used as a support unit for the clamping modules, as well as the Microclamp fixture system for smaller parts, which runs on the same base rail design.
In a typical 21-hour running production day, only one shift of operators is required, during which all the worker know-how is brought to the task of efficiently scheduling and fixing the workpieces into place on the various stations, then programming the FMS to execute the runs. As a result of this system, 13 to 14 hours of unattended running time are translating into a decided competitive advantage.
The shop has indeed priced out the production of various finished products, in small, medium and large batch runs, to China and found only the small quantity was made at a lower cost, with no shipping cost or time factored. This atypical scenario has boosted the confidence of both the job shop and its customers in the value of this workholding system.

Explore the May June 2008 Issue
Check out more from this issue and find your next story to read.
Latest from Aerospace Manufacturing and Design
- Simplify your shop floor operations while ensuring quality parts
- Happy Independence Day - July 4th
- Bombardier receives firm order for 50 Challenger, Global jets
- Automatic miter bandsaw
- SAS orders 45 Embraer E2 jets with options for 10 more
- Height measuring instrument
- Shopfloor Connectivity Roundtable with Renishaw & SMW Autoblok
- Moog expands space actuation, avionics manufacturing