
In a manufacturing shop in Grafton, Wisconsin, a 50-ton army tank named Amelia is parked on an aluminum-framed platform. Amelia drives on and off its platform several times each year, but the aluminum frame never budges.
Similar aluminum framing systems are all around the factory, holding everything from granite surface plates on the floor to a 100+ lb Smog Hog mist collector hanging from the ceiling. A single aluminum overhead shelf supports a heavy air compressor that “vibrates like crazy,” according to Frank Oetlinger, the energetic owner and president of Controlled Dynamics. He adds proudly, “That air compressor runs all the time. It’s been up there for three years and that shelf never moves.”
Oetlinger designed and patented the aluminum framing systems that he uses throughout Controlled Dynamics and in his other company, Blanking Systems Inc., located next door.
“The hardest thing to design is something simple that works,” Oetlinger says with a smile. He’s spent more than 45 years in the manufacturing industry and holds 150 patents, so he knows a thing or two about designing things that work. And Oetlinger enthusiastically predicts that his Crosslink aluminum framing system, “will ultimately change every aluminum structure on Earth.”

Common fixtures
Aluminum framing systems in manufacturing enclose machining cells and support conveyors and other automated material handling systems. They’re used to build workstations, carts, storage racks, and walls. It would be difficult to find an aerospace or automotive manufacturing facility anywhere that doesn’t use some type of aluminum framing system. But most of those are unstable, Oetlinger says, especially when used in environments subject to movement.
“If there’s any vibration they just fall apart,” he says.
That universal problem inspired the Crosslink system that maximizes extruded profile strength by creating mechanically locked, precision-aligned joints and components that can withstand heavy industrial vibrations. Oetlinger’s system becomes stronger and more rigid under dynamic conditions.
“The problem you have with other systems is that they’re all pivot-based. You’re dealing with 100% friction,” Oetlinger says. “Our system is a mechanical lock. We’re not pivot-based.”
Crosslink does not need gussets or cross brace supports, and can withstand direct, cantilevered, and torsional forces while maintaining alignment and stability.
Pointing to its supporting legs, Oetlinger says, “If you put a plate on top of these four columns and put a load on it, it would hold 1.4 million lb. And it’s all aluminum.”
More importantly, results are consistent and predictable. Engineers can run finite element analyses (FEA) on the structures and get predictable results.
Early adopters include Boeing, Northrop Grumman, 3M Corp., and Disney. Other customers include Caterpillar, Snap-On Tools, Eaton, and Rockwell Automation. Oetlinger is confident that the list will continue to grow, if he can get people to understand how the system works. The key is in understanding how his connectors mate the aluminum extruded parts.

Removable, reusable buck rivet
“When you’re sitting on an airplane in the window seat and you look out at the wing and you see all those little round things, hundreds, thousands of them, those are buck rivets,” Oetlinger explains. “Those dimples you see all over the side of a semi-trailer truck that you pass on the expressway, those are buck rivets, too.”
Buck rivets never loosen because, unlike pop rivets, they completely fill the holes into which they’re inserted. There are no gaps between the rivet and the surrounding material, so they don’t shift under dynamic conditions. They’re the preferred fastener for moving assemblies in trucks, aircraft, and trailers.
Oetlinger designed a reusable buck rivet for Crosslink that also leaves no room for movement in insertion holes.
“When you tighten it, it just becomes one piece,” Oetlinger says. “It’s stronger than a weld.”
The key difference is installation – traditional buck rivets are typically installed with an air gun and can only be used once while the reusable buck rivet installs with an Allen wrench and can be removed and reused.


Modular designs
Oetlinger’s employees at Blanking Systems Inc. use Crosslink for storage. Assembler Therese Dallgas says she loves the shelving system she uses to store her tools above her workbench.
“I can use it to assemble anything. If I want to change the layout of my shelf, I can loosen those connectors and change it,” Dallgas says. “I don’t have to get a guy to do it for me. I can put it together and it would hold a tank.”
Oetlinger adds, “Everything we do is simple and uncomplicated. When you take our parts and you put a bracket on and tighten it, it’s perfectly aligned. It locks and the bolt never comes out. It’s foolproof. Anybody can build anything.”

Amelia and the kids
The Leopard A5 main battle tank, Amelia, is named after Oetlinger’s eldest granddaughter and is frequently used to raise money for St. Jude Children’s Research Hospital. The idea came to Oetlinger when his youngest daughter, Liz, was diagnosed with cancer. Oetlinger holds an annual fundraiser, when he lets children with cancer climb on the tank and get behind the wheel. He intends to start his own foundation someday and plans to put the children’s names on the tank in the near future. Children in remission will get a star next to their names, he explains. Children who don’t win their battles with cancer “will have an angel next to theirs,” he says sadly. “3M is going to donate some tape that will stick on there forever.”
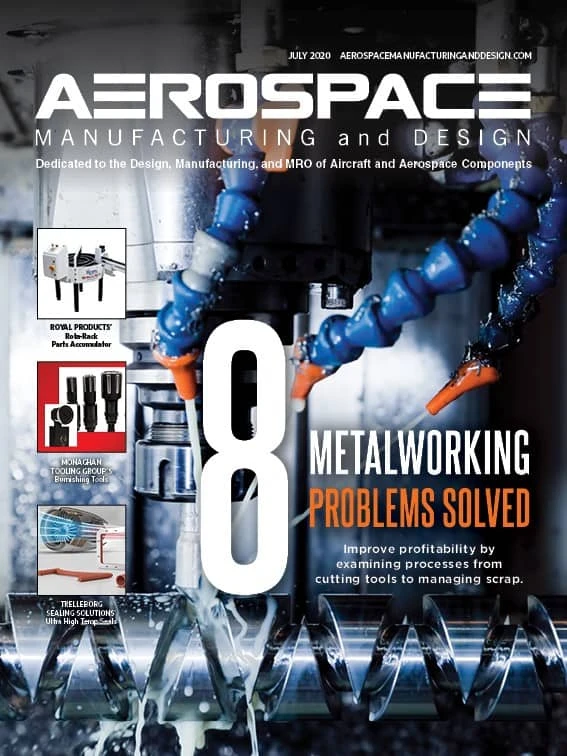
Explore the July 2020 Issue
Check out more from this issue and find your next story to read.
Latest from Aerospace Manufacturing and Design
- Revitalizing the Defense Maritime Industrial Base with Blue Forge Alliance
- Safran Defense & Space opens US defense HQ
- Two miniature absolute encoders join US Digital’s lineup
- Lockheed Martin completes Orion for Artemis II
- Cylinder CMMs for complex symmetrical workpieces
- University of Oklahoma research fuels UAS development
- Motorized vision measuring system
- Everyone's talking tariffs