
A contract secured by KUKA Systems Aerospace Group to develop the manufaturing facility for a high-profile helicopter included requirements for a series of work platforms designed to interface precisely with the helicopter and tooling at various stages of production.
“Before this project, we didn’t have a need for a modular, portable work stand,” says Rick Zaitonia, project manager for KUKA Systems.“We were using large steel work platforms, fixed in place, at a fixed height, which we designed and built in-house.”
It wasn’t until the helicopter program that KUKA needed to use the same work stands at different heights. Cataloged work platforms were available, but KUKA needed something custom-designed. Most standard work platforms were steel and fixed in place, while KUKA needed lightweight, mobile platforms. KUKA had the design capability to build the work platforms they needed, but the project involved coordinating and implementing more than 600 tools, and they needed to use their resources wisely.
“Instead of having to come up with custom designs for work platforms, we could go to the experts that already had the designs,” Zaitonia says. “We had a complex, large program, and it freed up our resources to let the experts handle that portion and let us specialize in what we’re good at.”

They researched potential suppliers and performed site visits to ensure the companies could meet the requirements of the project, ultimately, selecting Spika Design and Manufacturing for all the platforms required in the manufacturing line.
“Spika has the production capabilities to take care of volumes, quality control systems in place to put out a good product, and a management team to help us with the designs for different manufacturing facilities,” Zaitonia says.
Partnering with Spika
For the next three years, Spika worked with KUKA and its customer to design and manufacture work platforms for the various stages of assembly. Spika provided more than 30 work platform systems for the project, based on 15 different designs. The project was comprised of more than 90 modules. The platforms used several complex designs, including:
- Electrically controlled, dual-stage actuation for significant height adjustability
- Decks with trap doors which allowed the aircraft to pass through the platform when it was raised or lowered
- Decks with sensors and limits so the platform could not be lowered past a specific point with the trap decks down
- Work platform sections could be removed/reattached to larger sections for different assembly configurations
- Removable railings for multiple platform configurations
- Electric, electric-over-hydraulic floor locks remove working load from casters
- Extensive air and electric supply plumbed throughout
Spika worked with KUKA for the updates and changes to the system. KUKA and its customer were happy with the outcome.
“The relationship with the outsourcing company is more of a partnership and team effort than a vendor relationship,” Zaitonia says. “There has to be cohesiveness and transparency for it to work. The Spika design team has been great – they’re flexible and accommodated to all the change requests we made throughout the process. Spika platforms are quality, clean, and well put together.”
KUKA Systems Aerospace Group
Spika Design & Manufacturing
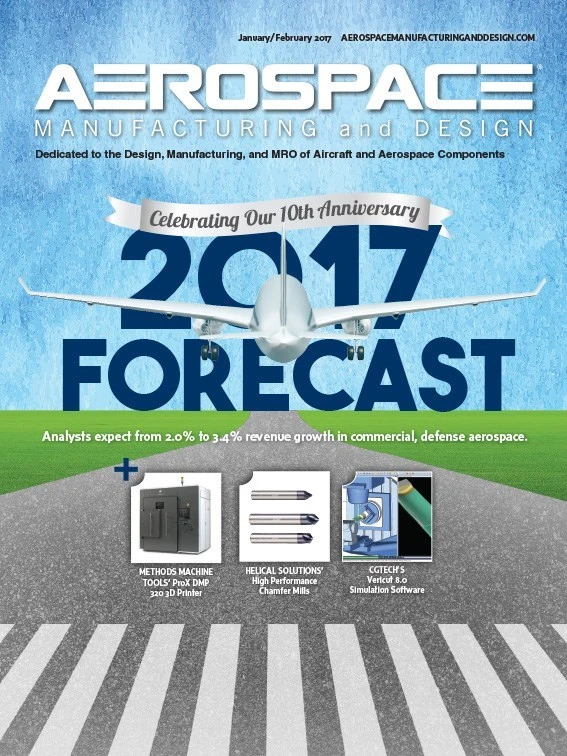
Explore the January February 2017 Issue
Check out more from this issue and find your next story to read.
Latest from Aerospace Manufacturing and Design
- 2024 Favorites: #10 Article – How 3D-printed aviation parts can accelerate return to air
- 2024 Favorites: #10 News – Boom Supersonic completes Overture Superfactory
- OMIC R&D hosts Supporting Women in Manufacturing Day 2024
- 4D Technology's AccuFiz SWIR interferometer
- Seventh Lockheed Martin-built GPS III satellite launches
- KYOCERA AVX's CR Series high-power chip resistor
- UT researchers receive Air Force grant for wind tunnel
- Monticont's linear voice coil servo motor