For part surfaces requiring features with specific and varying depths, removing microns of delicate surface material, and working with small precision parts and intricate compositions,
A single pass of a micro-abrasive stream can uniformly remove 0.127µm or less of material depending on the substrate, abrasive, and blast parameters.

Controlling erosion
Cutting, etching, and milling surface materials fall under the controlled erosion process category – precise removal of material from a part surface. Micro-abrasive blasting or microblasting, precision sandblasting on a micro scale, is suited to controlled erosion on small and precision parts because it employs very fine abrasives (17.5µm to 350µm), small nozzles (0.018" to 0.125"), and a consistently modulated abrasive feed to remove and alter microns of surface material in a repeatable pattern. Microblasting is often used to refine and alter aerospace parts that must meet strict industry
Four variables can determine how much material can be removed in
Abrasive type (particle shape, size, composition) – Size, shape, and hardness of abrasive impacts how much energy transfers to the substrate resulting in erosion
Abrasive velocity (controlled by pressure, blaster configuration, nozzle distance)–
Abrasive quantity (controlled by blaster configuration, blast duration) – Amount of abrasive each unit area of the substrate receives measured in grams per cm² per second
Substrate properties (hardness, crystal structure or grain size, ductility, homogeneity) – Sum of all the chemical, physical, and mechanical properties of targeted part affecting how easily material is removed during the erosion process
These four variables are usually identified during sample parts testing.
Abrasives
Abrasive type is the single most important variable in microblasting. Controlled erosion applications almost always use cutting abrasives with cutting
Particle size affects removal rates; large particles erode more material in less time using less powder, however, the larger the particle, the harder it is to control. A large particle increases surface roughness, creating messier transitions between eroded and untouched areas. If specifications are not too critical (example: 1,000µm depth, ±150µm), an abrasive with a large particle size may suit the application.
Control velocity, control depth
Controlled erosion applications usually require particle velocities of 150m/s to 225m/s (492ft/s to 739ft/s). Velocity is controlled by nozzle size, blast pressure, and the distance from nozzle end to target. Velocity is an extremely important variable in applications with tight tolerances.

Middle: Velocity and erosion have a corresponding relationship. Bottom: Optical (L) and actual (R, 150x and 200x) of an eroded spot on a silicon wafer (brittle).
Increasing blast pressure increases velocity, speeding erosion at the cost of precise depth control, leading to uneven surfaces. Worse, if the application requires photo-resist or plastic masking, too much blast pressure may destroy the mask before erosion is complete.
Keep nozzle perpendicular with long nozzle distance
Applications benefit most from a nozzle tip that sits perpendicular to the part surface. If the part curves, the nozzle should follow the curve so it remains perpendicular to the target. If the nozzle sits at an angle - however slight - to the target, the erosion rates drop, walls on either side of the channel form with different slopes, and masking may get undercut.
Applications that require a mask are typically done at a 1.5" to 2.0" nozzle distance from the part. Long working distances provide better erosion control and less depth variation across the part than close distances’ abrasive distribution becomes more uniform across the targeted surface area, yielding a larger spot size than the features.
Once
Pass fast, lean
Microblasting usually moves at a rate of 20-to-60 seconds per square inch of material per pass. Passing the nozzle as fast as possible preserves or limits damage to the masking material and provides better depth control per pass.
Controlled erosion applications tend to run a lean abrasive flow, less than 10g/min. At a certain hold or channel depth, abrasive particles run into one another rather than impacting the substrate material. A lean abrasive stream best cuts deep holes into a part while a heavier abrasive stream best cuts channels or shallow features.
Change one variable, change your finish
These four variables do not operate independently, tweaking one alters another, but relationships to remember are:
- Increasing blast pressure increases particle velocity, giving abrasives more energy for surface material removal and increases
abrasive quantity, compounding material removal rate - Fixing the nozzle close to the part surface concentrates abrasive to a smaller area but reduces abrasive velocity; a nozzle too close to the target results in exiting particles crowding one another, unable to accelerate to maximum speed
- Switching nozzles to alter spot size changes mass flow rate and alters stream velocity
Brittle vs. ductile substrates
The
- Silicon
- Quartz
- Sapphire
- Glass
- Ceramics
- Graphite
- Composites
- Hardened steel
Microblasting is most effective on homogeneous materials. The finer the grain structure and fracture mechanics of a substrate, the lower its Ra after blasting. Pitting is more likely to occur on sintered parts.

Carbon fiber composites
Microblasting works particularly well on carbon fiber because it does not compromise its integrity. Since microblasting does not impart stress or heat, it’s a dry process, it does not distort like a wet process might, and it does not create burrs or spurs. Most carbon fiber applications require masking and benefit from aluminum oxide blasting at a pressure of 50psi to 70psi.
Summary
Microblasting is a proven solution for consistently and efficiently removing microns of surface material and provides precision and control to etch and mill features of varying depths. It works on complex and curved part designs, benefiting brittle and
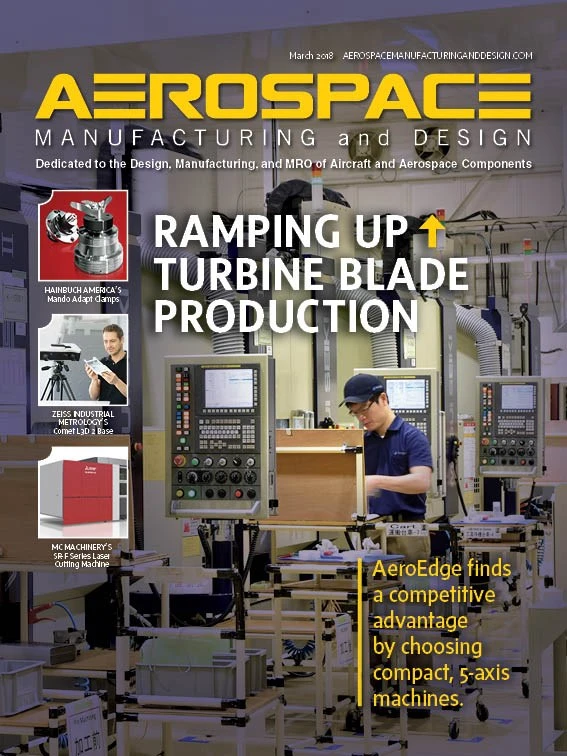
Explore the March 2018 Issue
Check out more from this issue and find your next story to read.
Latest from Aerospace Manufacturing and Design
- Qualified materials for 3D-printing mission-critical applications
- #69 Manufacturing Matters - Shopfloor Connectivity Roundtable with Renishaw and SMW Autoblok
- Demystifying Controlled Unclassified Information (CUI)
- Simplify your shop floor operations while ensuring quality parts
- Happy Independence Day - July 4th
- Bombardier receives firm order for 50 Challenger, Global jets
- Automatic miter bandsaw
- SAS orders 45 Embraer E2 jets with options for 10 more