Metrology solutions typically support industrial quality control (QC), verifying build processes and assuring customers that manufactured products meet specifications. However, scanning and imaging technologies used to inspect parts can play a major role in design and engineering.
Exact Metrology, an inspection services company, discusses how various scanning technologies – white-light systems, laser scanners, structured-light scanners – allow users to gather critical information needed for complex design challenges.
Airfoil scan procedures
Cross-section portions of airplane wings or turbine blades are critical aerospace structures with stringent quality requirements. Generating usable data from high-accuracy scans is critical in part design and manufacturing.
Scans can occur at the manufacturer’s facility with a mobile unit or at an Exact Metrology office. Airfoils typically require full documentation with photos, measurements, and all surface markings or serial numbers recorded prior to high-definition scanning.

Setup – A thin SKD-S2 Magnaflux coating is applied to the blade’s reflective surface for the second phase of a crack-checking process (Phase 1 dye penetration is not typically used).
A fixture and targets (placed using magnets on either side of the airfoil) constrain data during scanning. The fixture holds the airfoil in place for hands-free part-data capture. A manual or automatic turntable can also enhance part scanning and registration access.
Scanning – The part is positioned on the rotating table or stationary marble top and repeatedly scanned from multiple perspectives. Known geometric objects are often placed nearby for quality assurance and validation. The Breuckmann Stereo 3D scanning system uses a halogen, structured white-light projection system with dual 6.6-megapixel (MP) cameras.
Registration – Targeting uses an automated fitting of point clouds, based upon three common positions on the part or scene. Software simplifies registration and analyzes every point with overlaps and runs a best-fit algorithm to find the best alignment.
Validation – Verify automated methods with targeting and adding known geometric shapes. All scans are documented with notes, computer logging, and digital photos accompanying the recorded scan setup within the software.
Modeling – With data gathered, point cloud or data sets can be worked. The first step is to triangulate or mesh points together. Algorithms intelligently remove points from the network, decimating overlapping or redundant data points. This mesh is further manipulated by reducing triangles and points along flatter areas and retaining more triangles in curved and complex areas. This poly mesh can now be exported as a complete STL file or similar format.
Surfacing – Fitting non-uniform rational basis spline (NURBS) imaging models to the point cloud can be time-consuming. A surface is draped over the mesh and smoothed to reflect the actual part. The model is then ready for various formats, depending on client needs and limitations of existing conversion tools. A final 3D solid model can be provided as a dumb solid without parametry or history tree as an imported object.
Parametric modeling – A parametric model has all dimensional relationships within the CAD, allowing manipulation and fine-tuning without altering part geometry. The adjustable Pro/Engineer CAD model with known geometry possesses a design history.
Automotive resto-mod
Johan Kars, inventor of a catalytic abatement system for organic solvent emissions, is also an accomplished pilot and overall helpful guy: having reengineered and improved the waffle irons for his friend’s restaurant.
And it’s only natural, with a name like Kars, that he’d become a collector of classic automobiles.
After acquiring a 1951 Bentley MK VI H.J. Mulliner Lightweight Saloon Coupe, Kars sought to restore the bumper of the vehicle, which had been damaged in 1969 during a bad parking attempt. Only seven of these vehicles were made, so bumpers for the car are scarce.
Exact Metrology non-contact scanners were able to capture precise data about the existing bumper and vehicle rear-end, allowing the Bentley’s bumper to be re-manufactured to exact 1951 specifications.
The car was originally exhibited on the H.J. Mulliner stand at the Earl’s Court Motor Show in October 1951. Being a MD series, it is one of the first of the 4.5L versions of the car, which were introduced that year. The coachwork is a rare 2-door aluminum body with a hood that stretched an extra 3", an enhancement to the classic, flowing lines.
These Bentleys were in high demand and went all over the world. Original owners of the seven cars included: Princess Faiza Rauf of Egypt, French diplomat Baron Jules de Koenigswarter (while stationed in Mexico), and automotive scion Henry Ford II.
Kars’ vehicle was commissioned by Magnus S. Swenson, who resided on Wall Street in New York, and was delivered in November 1951. In 1953, the car was sold to Martin Block, a radio host, living in New Jersey, who passed away in 1967. The car was then driven on occasion by Block’s mistress, until her son locked the car in a garage in 1969, following the parking attempt that created a repair opportunity for Exact Metrology. A rudimentary repair was done to the rear fenders, but some damage remained.
Seeking to restore his precious purchase, Kars contacted Exact Metrology. Technicians arrived on-site with the portable NDI Scan System, a handheld laser scanner ideal for fast, non-contact digitization of physical components. The scanning technician quickly and accurately collected 3D data about the Bentley’s rear end and existing fenders.
NDI Scan System technicians oriented the ScanTRAK in 6 degrees of freedom (6DOF) without concerns of beam breakage and no mechanical restrictions. The system’s large measurement volume eliminates the need for time-consuming data capture.
With data collected, Exact professionals began modeling the parts at their offices. Geomagic Studio 3D Reverse Engineering Software converts 3D scan data into CAD models, allowing Exact to create a 3D model of the Bentley’s fender. Kars can use the model to recreate the damaged fender, a part out of production since 1951, restoring the rare Bentley to its as-built form.

Customized kneepads
Metrology's exact most rewarding project was to help a 9-year-old Tieshawn, a boy born with spina bifida, a spinal cord birth defect. Tieshawn loves to move, typically by walking on his kneecaps, which can cause painful callouses. Traditional kneepads weren’t designed for Tieshawn’s needs and slipped off quickly.
Cincinnati, Ohio-area based May We Help, betters the lives of people with special needs by partnering with skilled partners. It began working with Tieshawn’s family and therapists to find a better solution. It partnered with rapid-prototyping company Bastech, which had created similar kneepads for spelunkers (cave explorers). First, Bastech needed a very accurate understanding of how Tieshawn’s knees moved and were shaped.
Exact Metrology joined the effort, using Artec 3D Scanners to measure Tieshawn’s knees in his own bedroom in less than 30 minutes. The Artec scanner captures up to 2 million points of data a second with 3D point accuracy up to 0.1mm, using a handheld device that weighs less than 2 lb.

Popular for plastic surgery, orthopedics, post-trauma care, and dietology, the light scanners can generate 3D images of a single appendage or the entire human body.
With a better understanding of Tieshawn’s biomechanics, Bastech designers customized kneepads to provide more comfortable, safer movement.
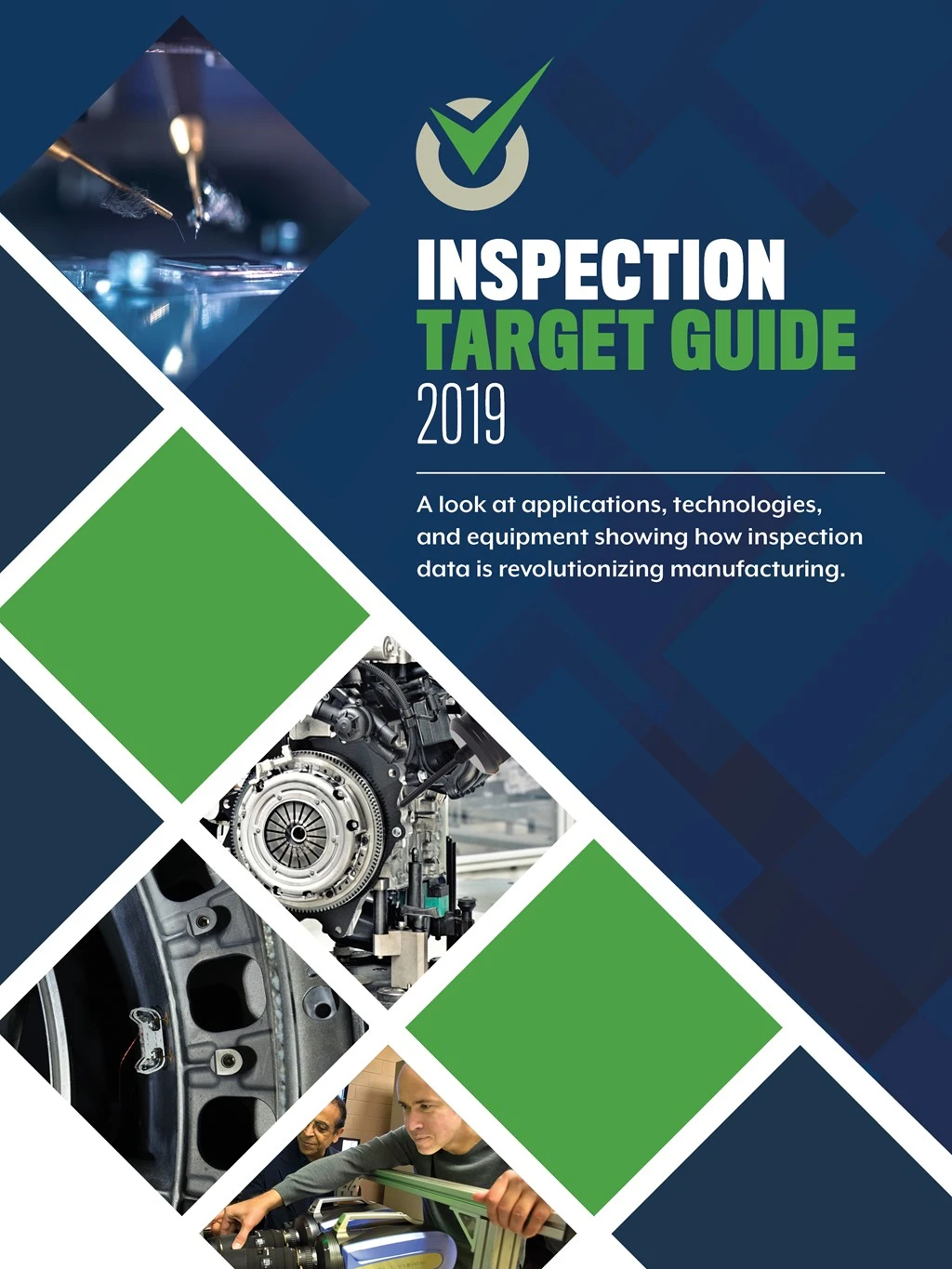
Explore the Inspection Target Guide Issue
Check out more from this issue and find your next story to read.
Latest from Aerospace Manufacturing and Design
- Safran Defense & Space opens US defense HQ
- Two miniature absolute encoders join US Digital’s lineup
- Lockheed Martin completes Orion for Artemis II
- Cylinder CMMs for complex symmetrical workpieces
- University of Oklahoma research fuels UAS development
- Motorized vision measuring system
- Everyone's talking tariffs
- Boom Supersonic to launch Symphony engine testing in Colorado