
As additive manufacturing (AM) moves out of design studios and laboratories to the manufacturing space, the technology can benefit greatly from the aerospace industry’s traditional focus on frequent inspection and tight tolerances. And, metrology systems can learn a thing or two from AM advances as well.
Aerospace AM
AM is more cost-effective in developing prototypes quickly, allowing organizations to bring products to market faster with higher quality and less expense. In aerospace, it benefits manufacturing of aircraft heating, ventilation, and air conditioning (HVAC) and air handling systems; aircraft instruments and controls; and turbine engine components.

It can make components with highly complex geometries, including internal features. Tooling isn’t necessary, which lowers the cost of small production runs of complex parts. Further advantages come from combining multiple components into one, so fewer machines are needed, reducing expenses, labor, and material costs.
Consolidating components can reduce regulatory costs because each aircraft mechanical part must undergo Federal Aviation Administration (FAA) review for design, documentation, production, and verification processes. If AM makes it possible to create one part instead of three individual pieces, verification time could fall by as much as half.
And, AM’s ability to cost-effectively produce complex parts for low-volume components improves part interchangeability through better dimensional control of component assemblies, improving fit when mating parts during final assembly.

AM improves metrology
Applying AM to metrology allows aerospace manufacturers to develop a faster, more refined measurement protocol that enables tighter quality management while allowing real-time measurements and results. This means less re-work or part re-creation, leading to greater integration and improved system design.
Custom measurement fixtures that were once too expensive, too heavy, or too time consuming to use become practical when made using a 3D printer. Individual test rigs for each employee become possible in some scenarios. Better positioning of workpieces can improve testing throughput, enabling 100% inspection for parts that formerly required too much handling.
And, because AM can produce fine internal features in components, custom measurement jigs allow manufacturers to choose between contact and non-contact measuring systems, depending on what best suits the workpiece.
Metrology improves AM
When producing critical AM parts, manufacturers must meet stringent tolerances – a role metrology systems have always played in manufacturing. Metrology sensors allow process monitoring and in-process measurement, optimizing AM dimensional accuracy as systems build parts layer-by-layer.
The ability to combine multiple parts into a single part is a significant benefit, but creates part verification challenges – the unique internal features enabled by AM are useless if producers can't assure customers that they’ll work consistently. Metrology technology providers are expanding capacity for computed tomography (CT) scanning systems for parts with less access to internal features.

Ensuring AM quality
Measurement applications differ between polymer and metal, so manufacturers printing in either should plan quality checks accordingly. Fixturing can account for differences in coefficient of expansion values for the materials and temperature compensation in the article, which determine whether contact or non-contact measuring.
Material differences also determine the choice of contact or non-contact measuring.
AM materials may be different from those used previously, possibly requiring other verification or different strength tests. This could extend the process, but given AM’s savings, it still could lower time overall. Manufacturers should evaluate issues such as surface finish – increasing measurement resolution on AM parts to detect more void defects, improving product and part quality, lowering production cost, and improving time to market.
CT scanning may be needed for parts combined into one component, as internal measurements may be out of reach for contact sensors. While laser scanners can provide the highest accuracy of all sensors, they can’t measure with precision inside a part as well as a coordinate measuring machine.

AM’s future
AM system demand will continue to grow. MarketWatch analysts expect the global AM market to exceed $6.50 billion by 2024 and grow at a compound annual growth rate (CAGR) of more than 13%.
More service providers will likely enter the market with the goal of refining and improving existing AM technologies. From CT scanning to robots with embedded image processing metrology, precision, real-time, in-line measurement appears to be as hot as the AM market, with improved usability, repeatability, and accuracy main goals for both.
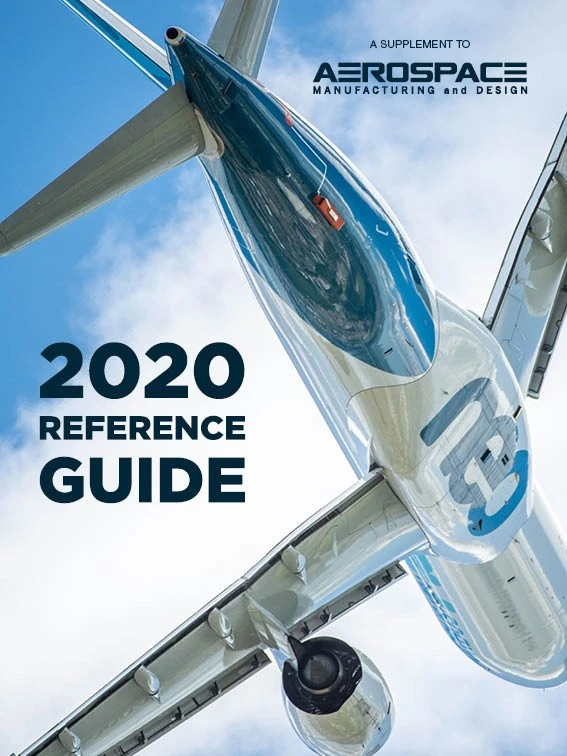
Explore the AMD Reference Guide 2020 Issue
Check out more from this issue and find your next story to read.
Latest from Aerospace Manufacturing and Design
- Doncasters’ Groton expansion reaches major milestone
- Hardware-encrypted drive with trusted supply chain
- Titanium drop bottom furnace installation underway
- Solid carbide taps for demanding materials
- The Partner Companies acquires Precision Eforming
- Hall Effect angle sensors
- July is for learning – so drop in for this month’s second Manufacturing Lunch + Learn
- Essential strategies to protect your data