
All photos courtesy of Betatype

Laser powder bed fusion (PBF) metal additive manufacturing (AM) produces solid and porous geometries in the same process, saving time and material. Advantageous for orthopedic implants, PBF creates complex structures that simulate the mesh-like porous properties of bone while delivering strength and durability. Porous textures can be built into implants of any shape or size – from acetabular cups to lumbar cages – allowing serial production of a portfolio of implants.
Maximizing machine use
Optimizing porosity size and distribution in orthopedic implant designs can generate high volumes of data that often slow down build processors. Betatype’s Engine build processor provides supercomputing power to overcome this, rapidly creating scan data and enabling serial production. Its build generation scalability can optimize build data.
Betatype recently worked with a company to create serial production build data that produced files in excess of 50GB. The Engine was able to scale up to 640 virtual CPUs with 4.88TB of RAM, generating build data in a few hours. Special Engine algorithms for converting complex geometry enabled implant designers to work in file formats up to 96% lighter than traditional STL files, such as Betatype’s ARCH format or nTopology’s LTCX data. For example, a spinal cage model was only 8MB as an LTCX file compared to 235MB as an STL file. These conversions simplify and shorten the process, letting designers innovate without dealing with mesh data.
Improved use of overall build volume in AM lowers cost per part, unlocking serial production of orthopedic implants. Betatype can stack implant parts by designing lattice node matched supports, using the entire build envelope to produce multiple, complex implants in a single build. Engineered supports can be removed using standard media blasting.

Reducing build times
Three major components of PBF build time need to be addressed to speed up the process:
- Dosing – Applying powder to the machine bed
- Fusion – Applying energy to the powder bed
- Motion – Movement between fusion
To optimize laser firing times and reduce delay times, with or without multiple lasers, Betatype technologies can reduce overall build times by up to 40%.
One orthopedic manufacturer using this technology portfolio decreased implant build to 15.4 hours from 25.8 hours. Betatype technologies optimized the laser scan paths, reducing firing and movement time required for complex lattice structures. Galvo-driven path optimization reduces delay times to 3 hours from 13 hours by optimizing the delays on an exposure-to-exposure level, also reducing laser travel distances to 100km from 170km.
Using Betatype’s technologies with PBF maximizes machine use, optimizes data file sizes, and reduces build times, enabling faster, more cost-effective serial production of orthopedic implants.
Betatype Ltd.
http://www.betaty.pe
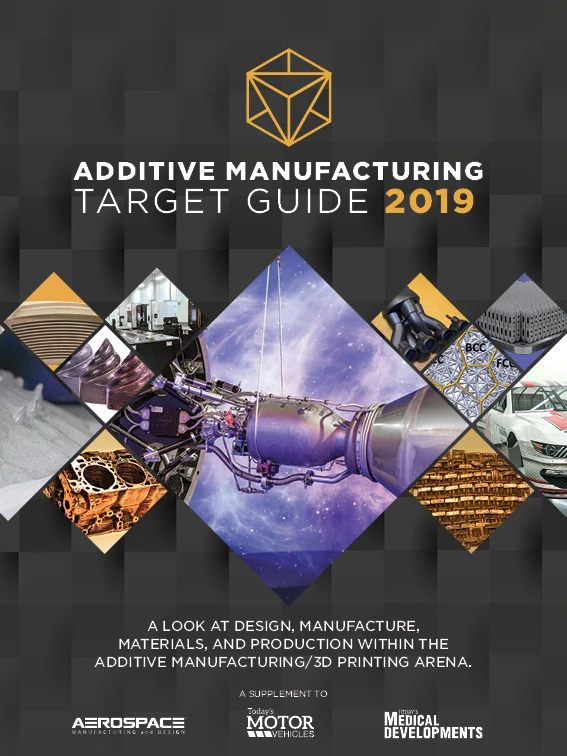
Explore the Additive Manufacturing Guide Issue
Check out more from this issue and find your next story to read.
Latest from Aerospace Manufacturing and Design
- Aerospace Industry Outlook returns for spring 2025
- Drop in for an interactive webinar on automation in manufacturing
- SW’s wing rib technology for the aerospace industry
- Mach Industries launches Mach Propulsion
- Murata Machinery USA's MT1065EX twin-spindle CNC turning center
- Electra reaches 2,200 pre-orders for its Ultra Short aircraft
- Heule's DL2 tooling for deburring of small bores
- Ralliant to establish global headquarters in North Carolina