
A metal alloy composed of niobium, tantalum, titanium, and hafnium has shocked materials scientists with its strength and toughness at extremely hot and cold temperatures. Its strength is defined as how much force a material can withstand before it’s permanently deformed from its original shape, and toughness is its resistance to fracturing. The alloy’s resilience to bending and fracture across a wide range of conditions could open the door for a novel class of materials for next-generation aero engines that can operate at higher efficiencies.
A team led by Robert Ritchie at Lawrence Berkeley National Laboratory and UC Berkeley, with groups led by professors Diran Apelian at UC Irvine and Enrique Lavernia at Texas A&M University, discovered surprising properties of the metal alloy.
The alloy is from a new class of metals known as refractory high- or medium-entropy alloys (RHEAs/RMEAs) made by mixing near-equal quantities of metallic elements with very high melting temperatures, giving them unique properties scientists are still unraveling.
According to first author David Cook, a Ph.D. student in Ritchie’s lab, most RMEAs have a fracture toughness less than 10MPa√m, making them some of the most brittle metals on record. The best cryogenic steels, specially engineered to resist fracture, are about 20x tougher than these materials. Yet the Nb45Ta25Ti15Hf15 RMEA alloy beat cryogenic steel, being more than 25x tougher than typical RMEAs at room temperature.
The scientists evaluated strength and toughness at five temperatures: -196°C (the temperature of liquid nitrogen), 25°C (room temperature), 800°C, 950°C, and 1,200°C.
The team found the alloy had the highest strength in the cold and became slightly weaker as the temperature rose, but still boasted impressive figures throughout the range. Fracture toughness, calculated from how much force it takes to propagate an existing crack in a material, was high at all temperatures.
Many elements with high melting temperatures and their alloys remain brittle up to 800°C. However, this RMEA withstands snapping at temperatures as low as -196°C.
Electron microscopy data revealed the alloy’s unusual toughness comes from an unexpected side effect of a rare defect called a kink band forming in a crystal when an applied force causes strips of the crystal to collapse on themselves and abruptly bend. The direction in which the crystal bends in these strips increases the force that dislocations experience, causing them to move more easily. This phenomenon causes the material to soften (less force has to be applied to the material as it’s deformed). The team knew kink bands formed easily in RMEAs, but assumed the softening would make the material less tough by making it easier for a crack to spread through the lattice. But this isn’t the case.
“We show, for the first time, that in the presence of a sharp crack between atoms, kink bands actually resist the propagation of a crack by distributing damage away from it, preventing fracture and leading to extraordinarily high fracture toughness,” Cook says.
Lawrence Berkeley National Laboratory
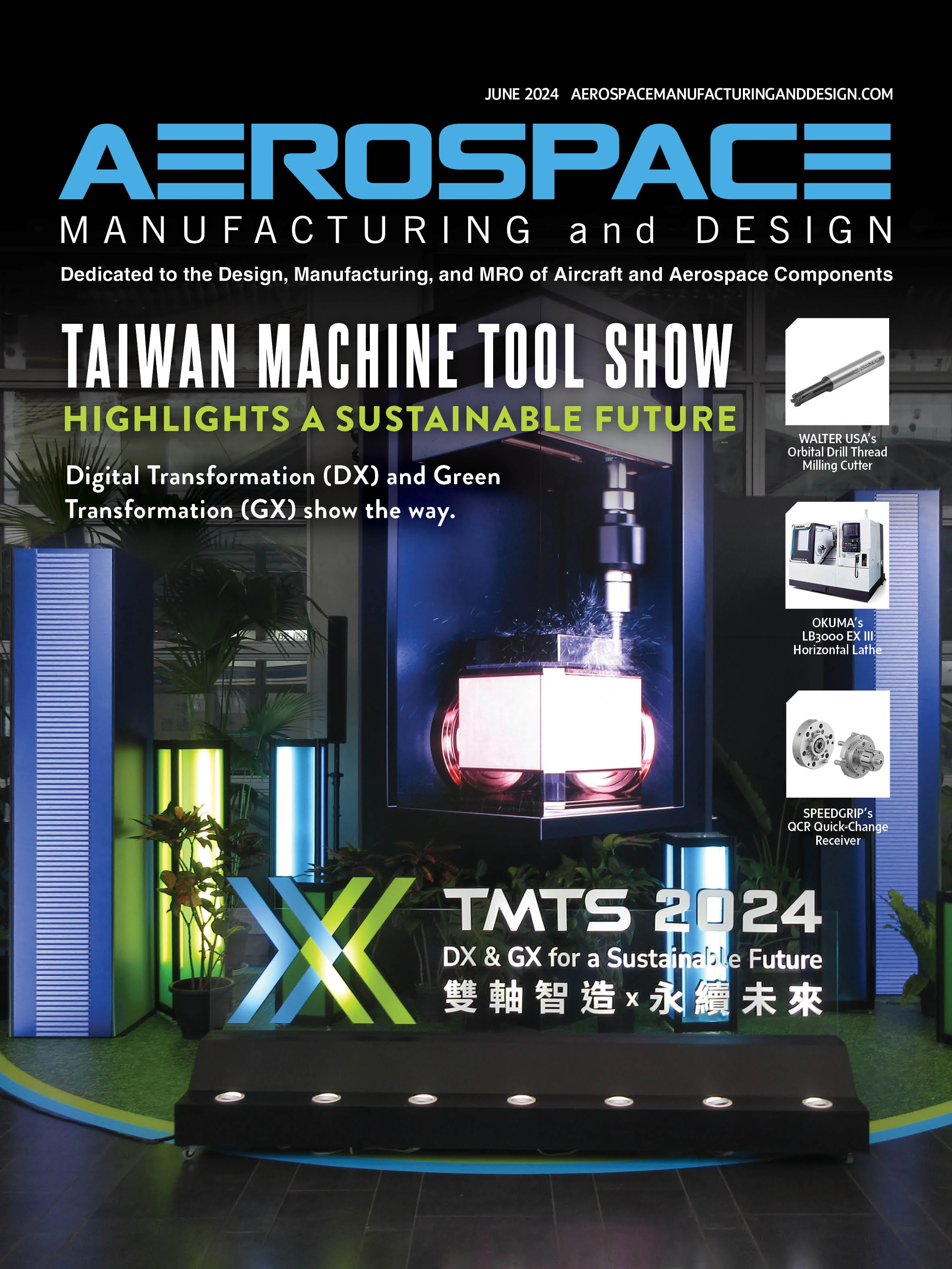
Explore the June 2024 Issue
Check out more from this issue and find your next story to read.
Latest from Aerospace Manufacturing and Design
- Heart Aerospace relocates to Los Angeles
- Fixtureworks introduces Stablelock Clamps
- Piasecki acquires Kaman's KARGO UAV program
- PI Americas’ long-travel XY piezo nanopositioners-scanners
- AAMI project call submission deadline extended to May 12
- Jergens launches cast iron tooling column additions
- Airbus to acquire assets relating to its aircraft production from Spirit AeroSystems
- FANUC America's Cobot and Go web tool