Turbine blades in aircraft engines help extract energy from hot gas. Exposure to harsh conditions degrades them, and periodically the worn-out turbine blades must be repaired. Traditional repair involves cutting and scraping the worn area for each blade, which takes time and generates waste. The blade is manually welded for repair and grinding restores the part to its ideal shape.
The LM300A and SB100 are a solution to reduce lead times up to 65% of the conventional welding process and minimize post-processing requirements.
A next-generation metal additive manufacturing system, the Lasermeister LM300A, uses directed energy deposition (DED) technology and the complementary 3D scanner, Lasermeister SB100.
The LM300A supports an expanded build area and is equipped with a 3D scanner, the SB100. Users can scan each workpiece with the click of a button, then the scanner automatically generates the tool path data for 3D printing. Pairing the LM300A and SB100 is useful for applications such as repairing turbine blades and molds.
Benefits
Seamless scanning and tool path generation – After placing a workpiece inside the SB100, a click of a button activates the module for scanning and measuring the workpiece. It compares its current shape with its ideal CAD model to extract the difference, automatically generating tool path data for repair specific to each workpiece. The process doesn’t require special skills or manual cutting. The tool path data is transferred to the LM300A to initiate high-precision additive manufacturing (AM). Once the additive process is completed, the workpiece can be placed back into the SB100 for scanning and inspection to confirm the repair was performed to its ideal model.
High-precision processing for various metals – LM300A performs high-precision processing by leveraging advanced optical and precision control technology. In turbine blade repair, the LM300A can process within the accuracy of 0mm to maximum +0.5mm difference for the X- and Y-axis and +0.5mm to maximum +1.5mm difference for the Z-axis. In addition, real-time laser power control by the melt pool feedback system delivers smooth surface finishing and precise part processing, achieving crack-less repair with optimal quality and stability.
Nikon Corp.IMTS 2024 booth #134150


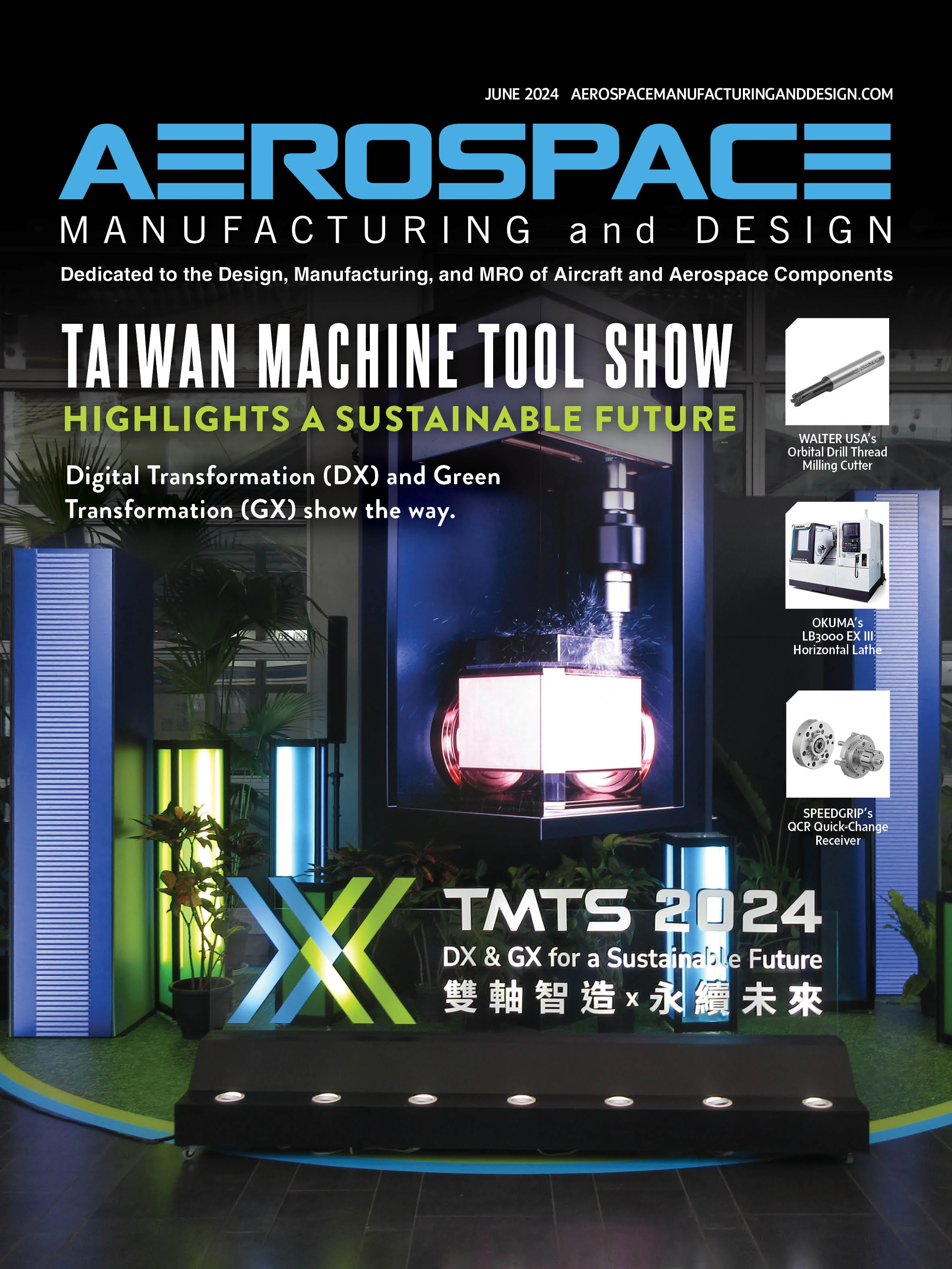
Explore the June 2024 Issue
Check out more from this issue and find your next story to read.
Latest from Aerospace Manufacturing and Design
- Piasecki acquires Kaman's KARGO UAV program
- PI Americas’ long-travel XY piezo nanopositioners-scanners
- AAMI project call submission deadline extended to May 12
- Jergens launches cast iron tooling column additions
- Airbus to acquire assets relating to its aircraft production from Spirit AeroSystems
- FANUC America's Cobot and Go web tool
- Chicago Innovation Days 2025: Shaping the future of manufacturing
- High-density DC/DC converters for mission-critical applications