
Pressure on original equipment manufacturers (OEMs) to produce more complex parts faster, without sacrificing quality, has created a cascading effect on foundries. To meet OEM needs, GF Precicast is offering metal additive manufacturing (AM) technologies.
Headquartered in Novazzano, Switzerland, the turbine engine rotating and structural parts supplier uses 3D Systems’ DMP Factory 500 and DMP Factory 350 metal additive manufacturing systems as an efficient, cost-effective alternative to super alloy investment casting.
The collaboration between the two companies has influenced how to leverage additive technologies for complex parts.
Cast or additive?
“We offer rotating and structural parts manufactured additively,” explains Paolo Gennaro, managing director, GF Precicast Additive SA. “For rotating parts, we focus on titanium-aluminum (TiAl) blades made by electron beam melting (EBM) technology, while for structural parts we offer nickel-based turbine rear frames and vanes together with a large family of bearing houses. The combustor – with its liners and nozzles – is also part of the offer. These structural parts are produced by large powder bed multi-laser machines.”
The AM materials are like those GF Precicast uses in casting.
“We began with conventional castable alloys such as 718 and 625 nickel super alloys, as well as aluminum alloy AlSi10,” Gennaro says. “With the evolution of advanced manufacturing applications, we are moving to difficult-to-cast materials such as titanium or cobalt-based alloys.”
While AM can use a broad range of metals, not every material is suited for 3D printing, explains Mark Cook, vice president, metals products, 3D Systems.
“Others are difficult or impossible to print due to the physics behind the process. For example, 6000 series aluminum is highly desirable but difficult to process in a way that results in end parts with high quality properties. The thermal dynamics of the AM process tend to form microcracks that are difficult to eliminate. Research continues into the list of desirable materials that are difficult to process, including 6000 series aluminum.”
However, AM can make parts with features impossible to obtain through casting.
“The advantages of AM include design without limitations and the ability to improve part functionality,” Gennaro says. “The redesign of a part for additive is typically focused on thin walls and integration of fluid channels. In some cases, we find it necessary to adopt new alloys to increase the part’s operating temperature.”
However, not all parts can directly replace investment-cast parts.
“AM parts are not replacing casted parts 1-to-1 in terms of geometry and materials,” Gennaro adds. “The move to additive from traditional manufacturing must yield a cost savings. If the transition makes sense financially, then the part must be redesigned – or designed for additive – to help realize additional benefits such as lightweighting and part-count reduction.”
AM offers another advantage by significantly shortening product development time. Gennaro notes, “With design for additive, we can iterate part design quickly without costly tooling. This dramatically reduces time-to-part, and ultimately time to market – by as much as one year.”

Workflow
As an early adopter of the DMP Factory 500, GF Precicast has successfully incorporated it into its production workflow to produce structural components.
Cook says, “A key benefit of the partnership between 3D Systems and GF Machining Solutions and the collaboration with GF Precicast is the focus on integrating all steps in the workflow. 3D Systems’ focus has been the AM workflow from design to printed part. The partnership with GF Machining Solutions brings the ability to design features into DMP systems that integrate the AM workflow with the subtractive workflow.”
AM can also save time in post-processing. “With the introduction of newer metal-capable platforms, we are seeing integration of automated post-processing technologies,” Cook says. “GF Machining Solutions and 3D Systems partnered to develop the DMP Factory 500 powder bed fusion platform, which includes GF Machining Solutions’ System 3R referencing and clamping system. Zero-point clamping enables optimal positioning of the build plate, facilitating a quick transition from the 3D printer to post-processing steps.”
Cook explains this integrated feature reduces setup times and enhances flexibility by quickly transitioning the build plate from the additive process, sending it along for post-processing, saving time and money.
“To specifically address the post-processing steps in the workflow,” adds Cook, “GF Machining Solutions developed tools for high speed milling as well as the AgieCharmilles CUT AM 500 wire EDM machine. The CUT AM 500 is able to cut even the smallest, most fragile metal parts from the build plate without causing damage, contamination, or alteration of the material. Being able to redefine this post-processing step is essential to reducing time-to-market and decreasing costs.”
Quality assurance methods for AM are still evolving but still resemble those used for casting. “We inspect the additive parts the same way we do cast parts,” Gennaro says. “We’re in the process of certifying components produced with additive technology using super alloys that can improve performance while reducing costs. In the future, we plan to implement the in situ monitoring available with DMP machines. As a result, we anticipate being able to reduce the standard inspection time by 80%, resulting in significant cost savings.
Building for tomorrow
The current GF Precicast AM build envelope is 500mm x 500mm x 500mm. But plans include producing 1m3 parts.
Increasing production capacity is also top of mind.
“Today, we produce hundreds of structural parts and several thousand rotating parts annually. In the next three years, our goal is to achieve an annual production of thousands of large structural parts and more than 10,000 rotating parts.”
The company is also focusing on opportunities to use AM for low-volume production in space propulsion for cryogenic turbo pumps and injection systems.

Synergies
Working with 3D Systems generated benefits and some synergies for GF Precicast, Gennaro notes.
“3D Systems and GF Machining Solutions brought together additive and traditional manufacturing expertise to develop a new platform for metal manufacturing. The integrated solutions deliver a new concept in factory automation that includes software for enhanced part design, 3D printers, materials, automated material handling, part separation by electrical discharge machining (EDM), milling equipment, and in situ data collection capabilities.”
Cook adds, “Over the course of our collaboration, 3D Systems and GF Machining Solutions have made great strides in the development of complete application-focused workflows and have consistently demonstrated this expertise in both the healthcare and aerospace industries.”
And, Cook says, 3D Systems is learning a lot from its early adopters. “The combined experience between the two companies is helping identify the right applications and develop the end-to-end workflow. From 3D Systems’ perspective, GF Precicast provides critical feedback about real-world high-value applications as well as key system performance requirements in the production environment; particularly for large parts (0.5m x 0.5m x 0.5m) that the company could not make with traditional casting methods. This feedback is used to directly impact the direct metal printing (DMP) solutions that 3D Systems provides to all customers.”
3D Systems
https://www.3dsystems.com
GF Casting Solutions
https://tinyurl.com/gfcs-precision-casting
GF Machining Solutions
https://tinyurl.com/gfms-additive-manufacturing
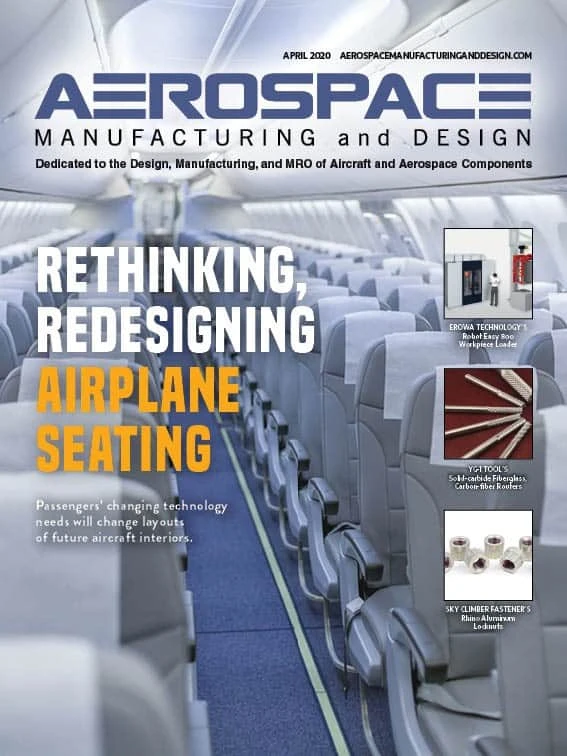
Explore the April 2020 Issue
Check out more from this issue and find your next story to read.
Latest from Aerospace Manufacturing and Design
- AIX shows aircraft interiors are a strategic priority for global airlines
- Machine Tool Builders Roundtable: Turn equipment into expertise
- No time to waste: How to machine MedTech parts more efficiently
- The 5 Best and Fastest Spindle Repair Services
- Mill smarter, not harder: How collaboration optimizes production
- Be proactive – stay ahead of tariffs and other economic and supply chain curveballs!
- Taiwan’s China Airlines orders Boeing 777X passenger, freighter jets
- Reamer re-tipping extends life of legacy tooling