
Developer, available in Flow 7.0 print 3D preparation software, simplifies migration of additive manufacturing projects to the company’s integrated metal 3D printing solution. Users can transfer their experience and knowledge from previous projects, develop new material processes, and control their optimization objectives.
Developer turns traditional design files into print files and grants editor-level access to print parameters so users can import parameters they’ve developed, optimize default parameters for application needs, and develop parameter sets supporting new material development. Once a part produced using Developer has been qualified, users can scale production leveraging the control, quality, and repeatability of the company’s Sapphire printers.
Toolholding system duo

The PGA 9500 provides a simple way to automate tool setup when using the powRgrip toolholding system, allowing tools to be set up unattended.
For seamless integration, the PGA 9500 connects via a robot to other equipment and tool storage areas. Its automatic door and controllable clamping device make the PGA 9500 suited for working within existing automation systems. Space-saving design, safe operation, and lack of heat or hazardous fumes make the clamping unit a solution for limited spaces.
The powRgrip Single toolholding system (pictured below) offers efficient and safe operation with a cycle time <5 seconds. While existing powRgrip loading/unloading units accommodate several toolholding collet sizes, the powRgrip Single is designed for one holder size series for shops requiring only one series of PG holders. The small-size powRgrip Single requires less room and allows the unit to be placed in tight areas close to the point of use.
REGO-FIX USA
IMTS 2024, booth #431822
Tooling for large spot facing, counterboring

SOLO-L back spot facing tool for large front or back counterboring operations has a capacity up to 1.95xD in bores from 25mm to 45mm diameter. It functions without an anti-rotation device, change in spindle rotation, coolant pressure, or contact mechanism. The sealed system prevents coolant contamination, and the pin-driven cutting blade prevents chips from jamming the system. It can be customized, with the tool’s blade housing, blade control, and blades designed to project requirements.
The system cuts nickel, titanium, and other exotic alloys, making it suitable for a wide range of CNC, transfer, multi-spindle, and conventional machining applications.
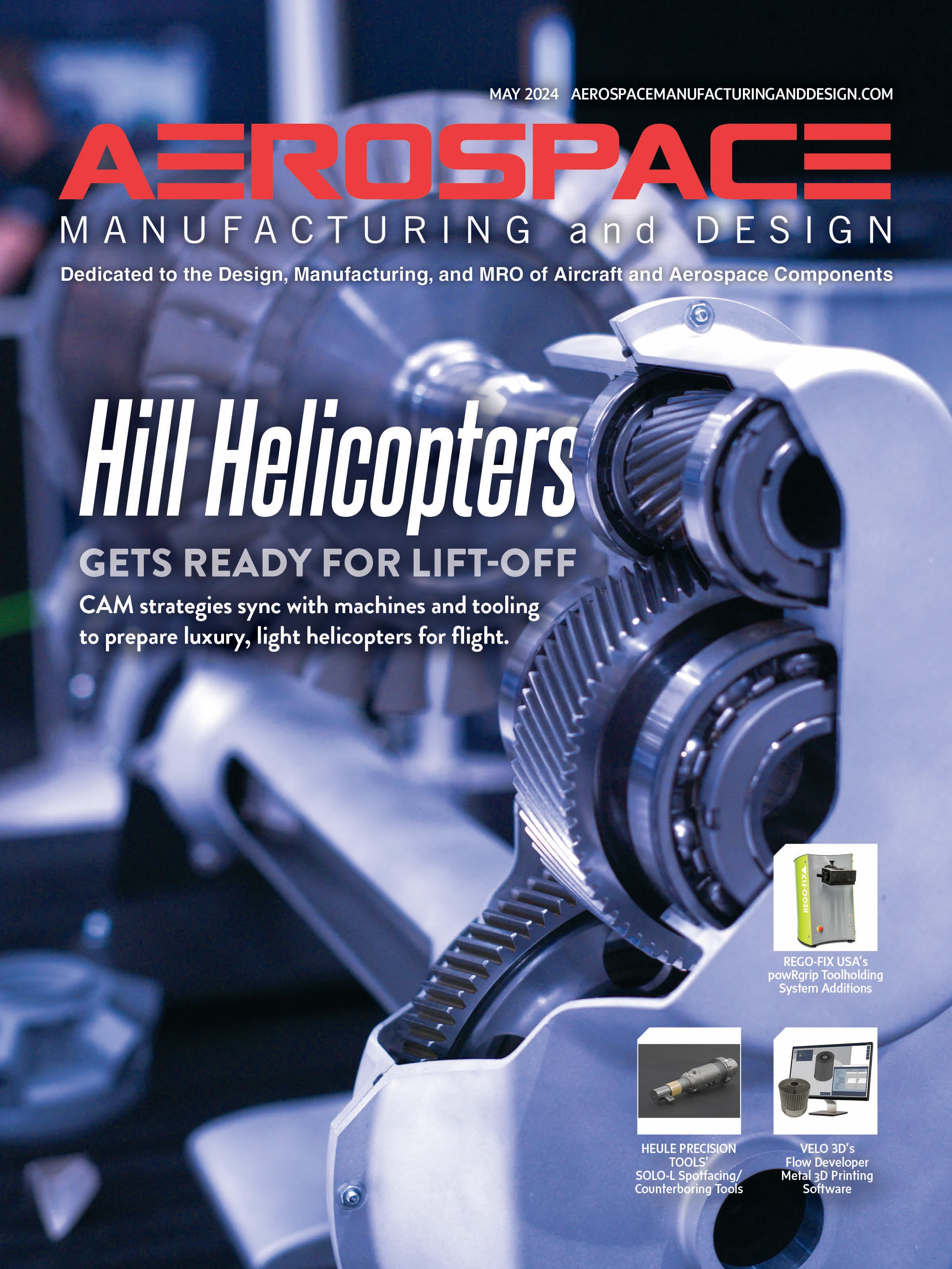
Explore the May 2024 Issue
Check out more from this issue and find your next story to read.
Latest from Aerospace Manufacturing and Design
- To the Smoothest Surfaces, Finishes, and Beyond | Okuma GA26W
- Extraordinary Starts Where Limits End | Okuma
- Satair, Champion Aerospace sign multi-year distribution agreement
- EMUGE-FRANKEN USA expands N. American solid carbide drill program
- AURA AERO unveils INTEGRAL R to the US market
- Creform Tite-Space AGV fleet
- Cyient Group, Deutsche Aircraft finalize multi-year contract
- High surface quality at high speed