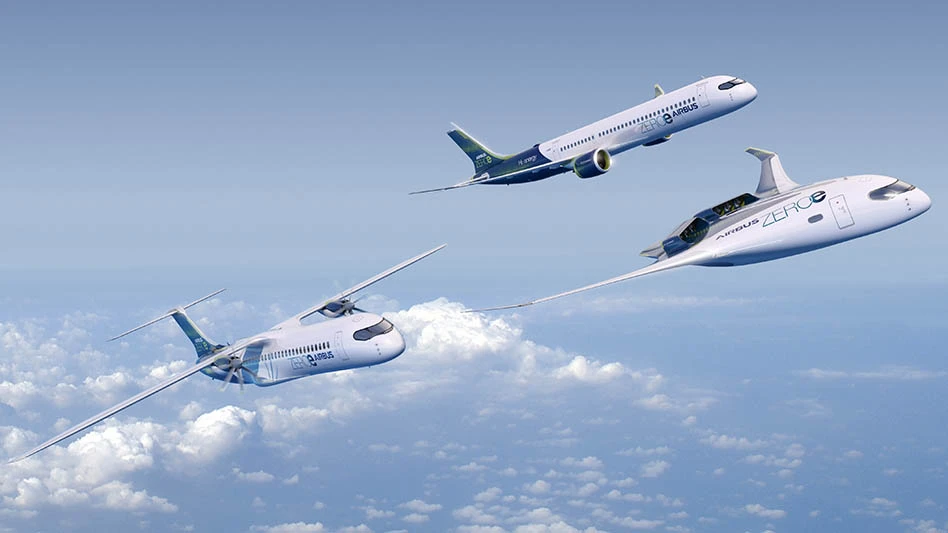

MIT engineers are creating a 1MW motor that could be a key stepping stone toward electrifying large aircraft. The team designed and tested the motor’s major components, which showed through detailed computations that the coupled components can work together to generate 1MW of power at a weight and size competitive with current small aero engines.
For all-electric applications, the team envisions the motor could be paired with a source of electricity such as a battery or fuel cell, turning the electrical energy into mechanical work to power a plane’s propellers. The electrical machine could also be paired with a traditional turbofan jet engine to run as a hybrid propulsion system, providing electric propulsion during certain phases of flight.
“No matter what we use as an energy carrier – batteries, hydrogen, ammonia, or sustainable aviation fuel – independent of all that, megawatt-class motors will be a key enabler for greening aviation,” says Zoltan Spakovszky, the T. Wilson Professor in Aeronautics and Director of the Gas Turbine Laboratory (GTL) at MIT, who leads the project.
The MIT team is composed of faculty, students, and research staff from GTL and the MIT Laboratory for Electromagnetic and Electronic Systems: Henry Andersen Yuankang Chen, Zachary Cordero, David Cuadrado, Edward Greitzer, Charlotte Gump, James Kirtley, Jr., Jeffrey Lang, David Otten, David Perreault, and Mohammad Qasim, along with Marc Amato of Innova-Logic LLC. The project is sponsored by Mitsubishi Heavy Industries (MHI).
“This is hard engineering, in terms of co-optimizing individual components and making them compatible with each other while maximizing overall performance,” Spakovszky says. “We have to push the boundaries in materials, manufacturing, thermal management, structures, rotordynamics, and power electronics.”
The MIT electric motor and power electronics are each about the size of a checked suitcase weighing less than an adult passenger.
The motor’s main components are: a high-speed rotor, lined with an array of magnets with varying orientation of polarity; a compact low-loss stator that fits inside the rotor and contains an intricate array of copper windings; an advanced heat exchanger that keeps the components cool while transmitting the torque of the machine; and a distributed power electronics system, made from 30 custom-built circuit boards, that precisely change the currents running through each of the stator’s copper windings, at high frequency.
To mitigate risk, the team built and tested the major components individually and showed they can operate as designed and at conditions exceeding normal operational demands. The researchers plan to assemble the first fully working electric motor and start testing in the fall.
The MIT team’s design could power regional aircraft, where multiple 1MW motors power multiple fans distributed along the wing of future aircraft.
Sponsored Content
Screen and density separate your B-line with one machine!
The multi-functional SUB-PAN FREE® TAPER-SLOT® Screen DENSE-OUT® Combo saves valuable space. It provides two processes in a single machine with screening and density separation for up to three fractions. The flow of material begins on our rugged TAPER-SLOT® Screens for size separation and then over DENSE-OUT® air knives to separate by density.
Sponsored Content
Screen and density separate your B-line with one machine!
The multi-functional SUB-PAN FREE® TAPER-SLOT® Screen DENSE-OUT® Combo saves valuable space. It provides two processes in a single machine with screening and density separation for up to three fractions. The flow of material begins on our rugged TAPER-SLOT® Screens for size separation and then over DENSE-OUT® air knives to separate by density.
Sponsored Content
Screen and density separate your B-line with one machine!
The multi-functional SUB-PAN FREE® TAPER-SLOT® Screen DENSE-OUT® Combo saves valuable space. It provides two processes in a single machine with screening and density separation for up to three fractions. The flow of material begins on our rugged TAPER-SLOT® Screens for size separation and then over DENSE-OUT® air knives to separate by density.
Sponsored Content
Screen and density separate your B-line with one machine!
The multi-functional SUB-PAN FREE® TAPER-SLOT® Screen DENSE-OUT® Combo saves valuable space. It provides two processes in a single machine with screening and density separation for up to three fractions. The flow of material begins on our rugged TAPER-SLOT® Screens for size separation and then over DENSE-OUT® air knives to separate by density.
Sponsored Content
Screen and density separate your B-line with one machine!
The multi-functional SUB-PAN FREE® TAPER-SLOT® Screen DENSE-OUT® Combo saves valuable space. It provides two processes in a single machine with screening and density separation for up to three fractions. The flow of material begins on our rugged TAPER-SLOT® Screens for size separation and then over DENSE-OUT® air knives to separate by density.
Sponsored Content
Screen and density separate your B-line with one machine!
The multi-functional SUB-PAN FREE® TAPER-SLOT® Screen DENSE-OUT® Combo saves valuable space. It provides two processes in a single machine with screening and density separation for up to three fractions. The flow of material begins on our rugged TAPER-SLOT® Screens for size separation and then over DENSE-OUT® air knives to separate by density.
Get curated news on YOUR industry.
Enter your email to receive our newsletters.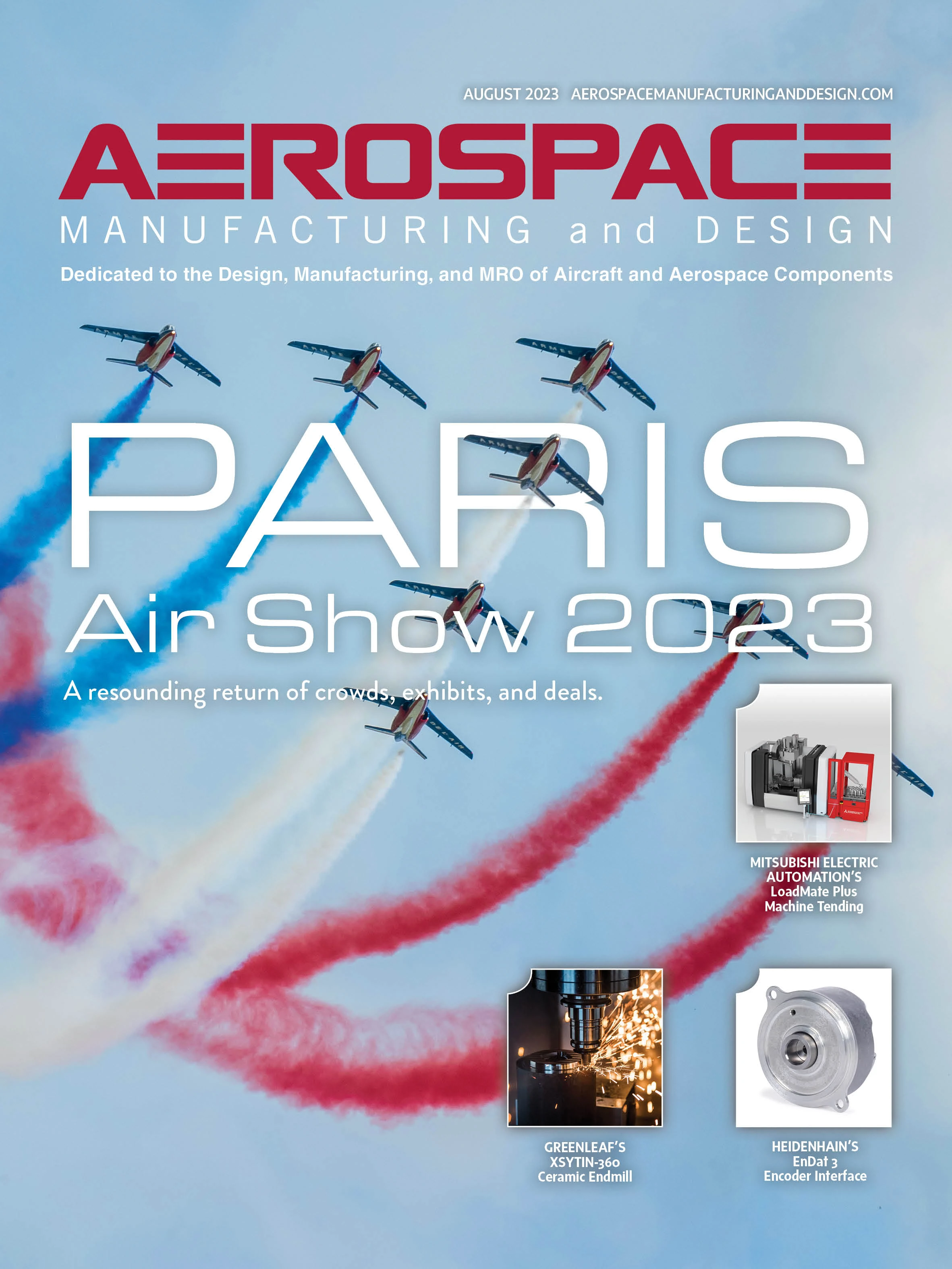
Explore the August 2023 Issue
Check out more from this issue and find your next story to read.
Latest from Aerospace Manufacturing and Design
- Lithuanian airline Jump Air orders 20 ERA aircraft
- Last call for July’s medical manufacturing Lunch + Learn!
- Piper Aircraft receives its largest ever domestic trainer order
- Miniature, high force-to-size linear voice coil servo motor
- MagniX, Robinson to develop battery electric R66 helicopter
- Zero-point clamping modules
- Hartzell electric engine propeller earns FAA approval for AAM
- Thin profile flame and thermal barrier