
Liability for defects, inconsistent quality, fluctuating supplier costs, increased globalization, and device regulations all pose challenges for the medical device industry. The margin of error approaches zero for medical devices being brought to market. If defects are not discovered and corrected during development, patient injury or death can result, and disastrous legal ramifications could face the company.
This means medical manufacturers must comply with the U.S. Food and Drug Administration’s (FDA) current good manufacturing practice (CGMP) requirements that assure proper design, monitoring, and control of manufacturing processes and facilities.
With so much riding on achieving perfection, every step of the development process must be optimized for quality through repeatability, reproducibility, and traceability. Zeiss Industrial Quality Solutions provides medical device and medical component manufacturers with high-performance equipment necessary for quality assurance (QA).

Concept to market
CGMP requirements govern the methods used in – and the facilities and controls used for – the design, manufacture, packaging, labeling, storage, installation, and servicing of all finished medical devices intended for human use. That means manufacturers of medical parts must establish and maintain procedures for identifying parts during all stages of receiving, production, distribution, and installation.
Each manufacturer of a device intended to be life-sustaining, life-supporting, or implanted into the human body must establish and maintain procedures for traceability. This follows a part’s origin backward in the supply chain and forward along the distribution chain, using identifying characteristics and records on each unit, lot, or batch of finished medical devices and the appropriate components.
Gaining certainty
Reporting requirements for collecting quality and metrology data under FDA oversight are even higher for medical device manufacturers than aerospace and automotive parts manufacturers. Zeiss equipment that can be calibrated to ISO 10360 standards for coordinate measuring machines (CMMs) can assist companies in complying with these stringent requirements.
This international standard of measurement verification specifies acceptance tests for the performance of a CMM used for measuring linear dimensions as stated by the manufacturer.
Zeiss chooses to work by this – the strictest standard – because it ensures comparability worldwide.
The ISO 10360 performance evaluation includes testing repeatability and reproducibility. Repeatability of measurements refers to the variation in repeat measurements taken by a single person or instrument made on the same subject under identical conditions. This is vital when it comes to gaining certainty in your standardization processes and relies on defining measurement conditions and then replicating the process.
The goal must be to maintain the same conditions with the measurement process and then repeat it until the desired number of samples is recorded.
When performing a repeatability test, collect data using the same:
- Method
- Operator
- Equipment
- Environmental conditions
- Location
- Item or unit under test
The aim is to collect repeatable results throughout a short period of time without changing anything (if possible).
Whereas repeatability is the random uncertainty of results under the same conditions, reproducibility is random uncertainty under changed conditions. Reproducible conditions, for instance, include the change of operator and subsequent changes in time and environment.
Options to meet ISO requirements
As production capacity grows and efficiencies increase, manufacturers must adhere to product compliance standards with proof, such as Zeiss metrology solutions that use ISO-compliant validation methodology and documentation.
While a CMM may be compliant to ISO 10360-7, Zeiss offers additional technologies for meeting ISO standards, such as the Zeiss O-Select optical measuring system that satisfies three requirements: Equipment: Artifacts used to calibrate, qualify O-Select measuring machines use DKD-certified scales Analysis: ISO 10360-7 methodology to calibrate, qualify O-Select machines Documentation: Records provided on each calibration to prove when, how calibrations, qualifications were completed.
The O-Select’s maximum permissible error is 4.5 + L/100µm and repeatability is 0.9µm.
“Quickly and reliably obtaining ISO-compliant, traceable, and reproducible measured values was a key aspect for us in development” of the O-Select, says Andrzej Grzesiak, Zeiss’ senior director of metrology systems.
Conclusion
By complying with FDA and ISO 10360 standardization processes for medical parts, manufacturers can improve productivity and cost savings, delivering a competitive edge in the medical component manufacturing supply chain. Solutions, such as O-Select, offer an alternative to CMMs and provide value to customers through repeatability, reproducibility, and traceability with comprehensive historical data and reports.
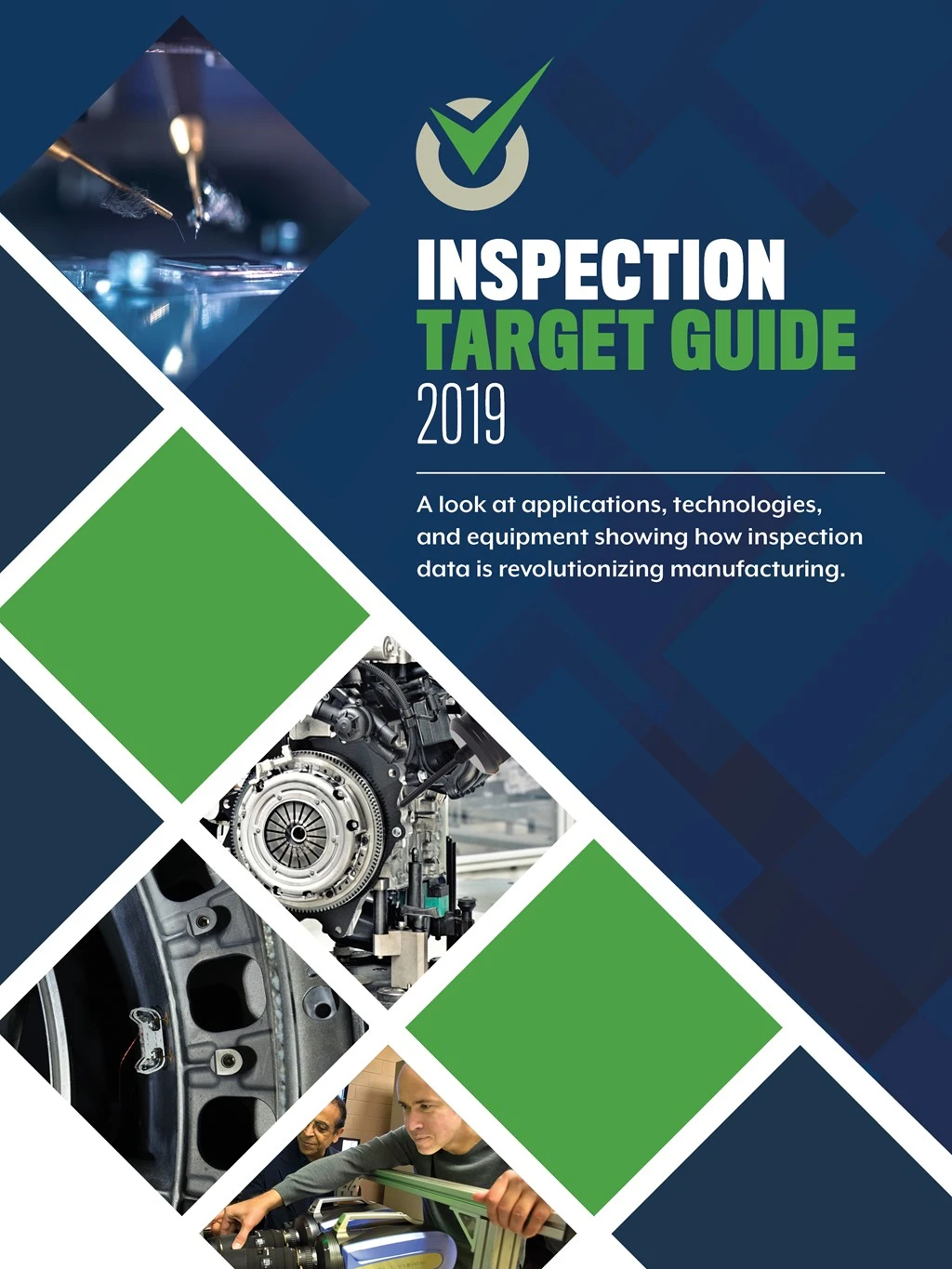
Explore the Inspection Target Guide Issue
Check out more from this issue and find your next story to read.
Latest from Aerospace Manufacturing and Design
- Lithuanian airline Jump Air orders 20 ERA aircraft
- Last call for July’s medical manufacturing Lunch + Learn!
- Piper Aircraft receives its largest ever domestic trainer order
- Miniature, high force-to-size linear voice coil servo motor
- MagniX, Robinson to develop battery electric R66 helicopter
- Zero-point clamping modules
- Hartzell electric engine propeller earns FAA approval for AAM
- Thin profile flame and thermal barrier